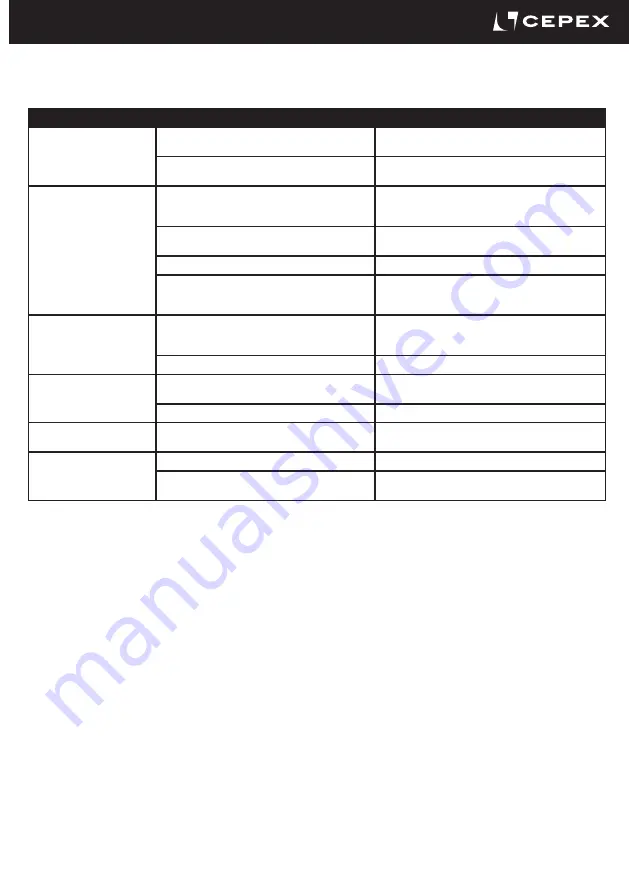
11
10.
TROUBLESHOOTING
T 9.1
FAULT
POSSIBLE CAUSE
FAULT CLEARANCE
The disc does not fully open
or close.
The sockets were not correctly bevelled.
Disassemble the valve and bevel the sockets as indicated
in table T6.2.
Foreign materials in the compartment (adhesive, etc.).
Disassemble the valve and check for obstructions in the
disc and gasket contact area.
Excessive opening or closing
torque.
The valve has been inactive for a long time.
Operate with an auxiliary release key (not the plastic
handle).
Disassemble the valve and lubricate the sealing gasket.
High temperatures or chemicals can cause damage to
the gasket.
Check the chemical compatibility of the liquid with the
disc and the working temperature. Replace the gasket.
Excessive flange torque.
Tighten flanges as indicated in table T5.1.
Misalignment between sockets and valve.
Disassemble the valve and reassemble with concentric
alignment (observe the correct tightening sequence and
torque).
The valve is not completely
watertight in the sockets.
Misalignment between sockets and valve.
Disassemble the valve and reassemble with concentric
alignment (observe the correct tightening sequence and
torque).
Flange screws not tight enough.
Tighten flanges as indicated in table T6.1.
The valve is not completely
watertight at the sealing
gasket.
Inadequate chemical resistance.
Check compliance with the specifications in this
document.
Temperature out of range.
Replace the gasket.
The valve does not open or
close.
Lack of current.
Check power supply to the actuator.
The valve does not close
completely.
The actuator stroke is not well adjusted to the valve.
Check adjustment limits according to the actuator manual.
The torque of the valve has increased above the
calculated value.
Check the valve: obstructions in the disc or malfunction
of the valve.
EXTREME ELECTRIC BUTTERFLY VALVE