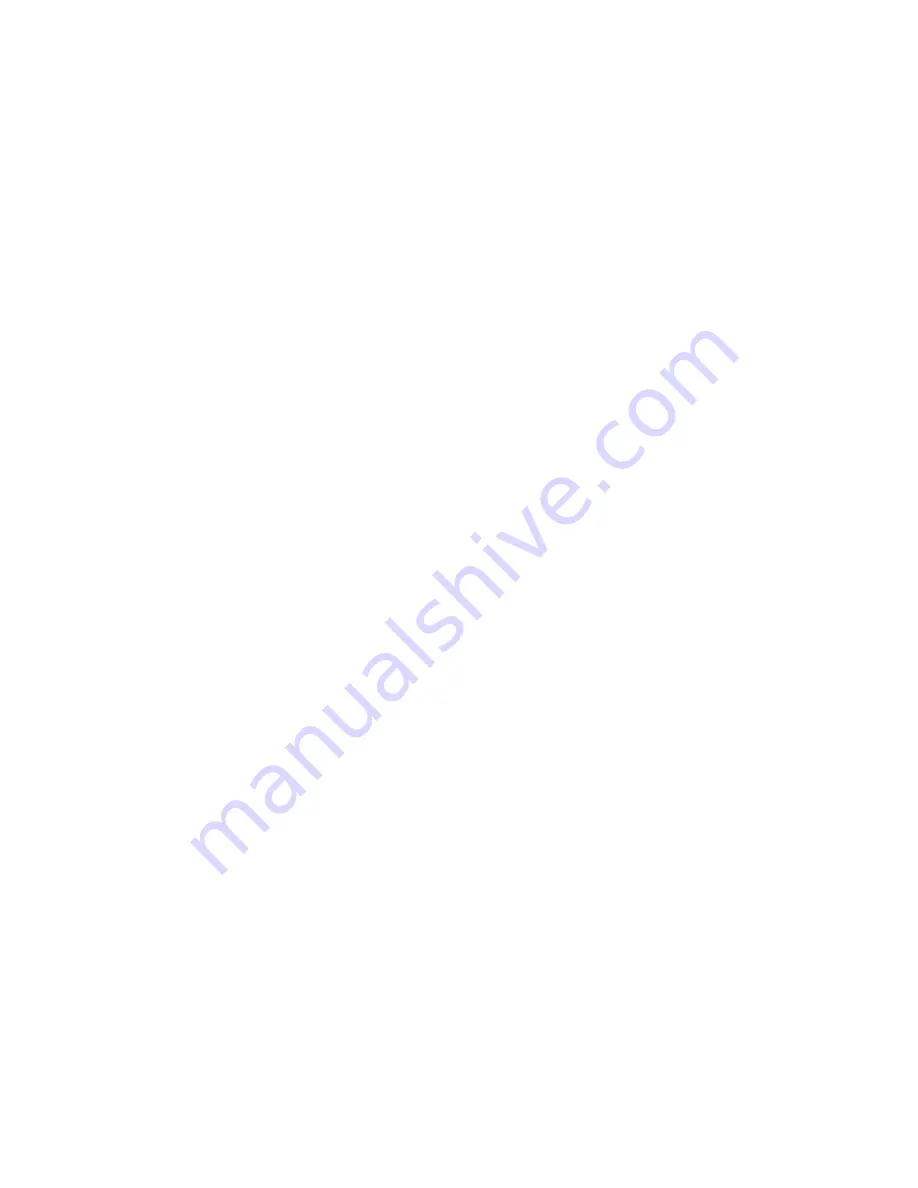
GRID DIGITIZING TIPS
Digitizing is, by its nature, a slow, precise process. The time it takes to digitize a part is
effected by four factors: feedrate, step size, detail density and over-all shape of the object.
The fast probing feedrate parameter setting controls the speed to find the surface. A second
approach to the surface after it is found is done at the slow probing or measuring feedrate.
This will provide the high accuracy required of part setup and measurement. The two hit
method optimizes speed and accuracy. The two hit method is not time efficient for digitizing.
Knowledge of the surface to be digitized is used to plan a grid approach at a fixed feedrate to
collect surface data. The speed selected for the digitizing run is a trade-off of time and
accuracy. Less time, less accuracy. More time, more accuracy. Additionally higher feedrates
induce vibration in the machine frame and add to the digitizing errors. A few short test runs
can determine the optimal feedrate.
The accuracy achieved digitizing 3 dimensions is dependent on stylus length and related
PTV (pre-travel variation) for the probe being used. See the performance characteristics
section for an example of PTV. Probing and part setup that is always done in a single
direction can be handled by a probe that simply has good repeatability. Good repeatability is
not a substitute for low PTV. The DP-7 was developed specifically for 3D digitizing accuracy
with long stylus assemblies. Determine the acceptable digitizing error for the project, the
probe PTV (3D) must be less than the acceptable error.
The X, Y, and Z stepover – The smaller the stepover distance, the longer the digitizing run.
For instance the typical time it takes to digitize a 1” by 1” grid with a step over of .010” in X,
and .010” in Y, (with parameters 14 and 15 set to 30ipm and 5ipm respectively), is 45 minutes
with 10,000 data points being recorded. By changing the X stepover to 0.005” and the Y
stepover to 0.005” the time increases to 3 hours with the number of data points recorded
increasing to 40,000. The trade off with time, is surface finish and detail. The finer the
stepover amount in the digitizing run the better the surface finish is going to be in the final part
and the more fine detail you will be able to capture. As the end user, it is up to you to find the
settings that give you the finish, and detail level you are looking for in the final part.
Remember, the Centroid control can digitize unattended, 24 hours a day, 7 days a week, if
you really need the detail and finish, (just remember to fill the automatic oiler tank!).
The third factor that affects the time it takes to digitize a part is the density and height of the
surface detail. The more vertical walls the probe stylus must climb, up and down over, the
longer the digitizing will take. This is not a factor you have much control over, except for
adjusting your Z stepup distance, but in general this will have little effect.
Finally, if the piece is odd shaped, you may want to patch several small digitizing runs
together and there by eliminate the wasted time that would be spent moving over areas that
are not pertinent to the data you want to collect.
Last Modified 2014-09-16 04:12:44 AM
Page 15 of 21
C:\Users\Keith\AppData\Local\Temp\7zO0E521723\DP7body20140916.odt