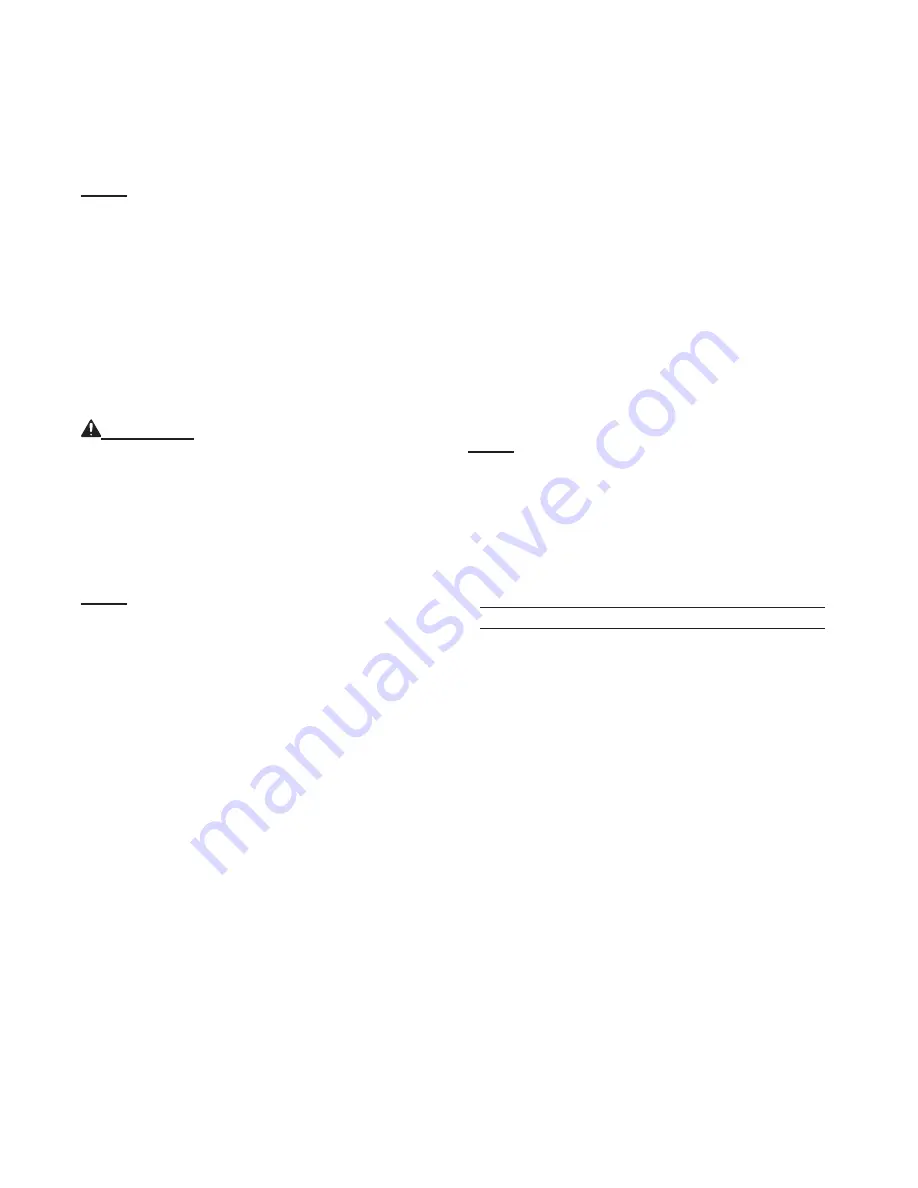
Page 10
For technical questions, please call 1‑800‑444‑3353.
SKU 68024
air hose is ruptured. The shutoff
valve should be a ball valve because
it can be closed quickly. See pages 8
and 9 for Air Tool Setup procedures.
Note:
If an automatic oiler system is not
used, add a few drops of Pneumatic
Tool Oil into the airline connection before
operation. Add a few more drops after
each hour of continual use.
2. Attach an air hose to the compressor’s
air outlet. Connect the air hose to the
air inlet of the tool.
Please note:
a
quick coupler will be needed for
proper connection.
WARNING! TO PREVENT SERIOUS
INJURY FROM ACCIDENTAL
OPERATION: Do not install a quick
coupler on the tool.
A coupler contains
an air valve that will allow the air tool to
retain pressure and operate accidentally
after the air supply is disconnected.
Note:
Air flow, and therefore tool
performance, can be hindered by
undersized air supply components.
3. The air hose must be long enough
to reach the work area with enough
extra length to allow free movement
while working.
4. Release the tool’s Trigger (44).
5. Close the in-line safety valve between
the compressor and the tool.
6. Turn on the air compressor according to
the manufacturer’s directions and allow it
to build up pressure until it cycles off.
7. Adjust the air compressor’s output
regulator so that the air output is enough
to properly power the tool, but the output
will not exceed the tool’s maximum
air pressure at any time. Adjust the
pressure gradually, while checking
the air output gauge to set the right
pressure range.
8. The air pressure setting must not exceed
job site regulations/restrictions. The air
pressure setting must not exceed 90 PSI
when being used with work pieces that
have a thickness of less than 1-3/4”.
9. Inspect the air connections for leaks.
Repair any leaks found.
10. If the tool will not be used at this time,
turn off and detach the air supply, safely
discharge any residual air pressure,
and release the trigger to prevent
accidental operation.
Note:
Residual air pressure should not be
present after the tool is disconnected
from the air supply. However, it is a
good safety measure to attempt to
discharge the tool in a safe fashion after
disconnecting to ensure that the tool is
disconnected and unpowered.
Nail Penetration Depth Adjustment
1. With the tool connected to its air supply
and with the nails loaded, test fire on a
scrap material (similar to the workpiece)
and note the depth of nail’s penetration.
2. To adjust nail depth penetration, rotate
the Depth Knob (52). Turn the Depth
Knob to the left (+) for deeper nail
penetration and to the right (-) for more
shallow penetration.
3.
CAUTION!
When working with asphalt
shingles in particular, the nail head
should not sink below the top face of
the shingle.