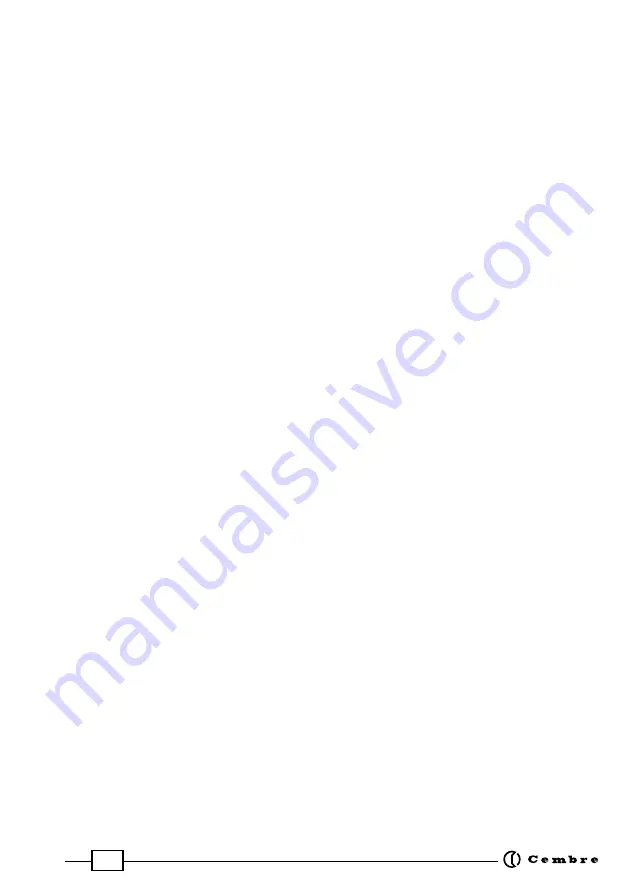
29
APPENDIX “B” FOR LD-2E AND LD-2E-110 DRILLS
Air noise
(Directive
2006/42/EC
, Annexe 1, point 1.7.4.2, letter u)
–
The continuous equivalent weighted level (A)
of noise pressure at the working place L
pA
is equal to .............................................................85,8 dB (A)
– The maximum value of instantaneous weighted noise
pressure C at the working place L
pCPeak
is lower than .................................................................130 dB (C)
– The level of noise force produced by the machine L
WA
is equal to .................................................................................................................................................96,6 dB (A)
Protection of operators against risksof exposure to noise during work.
Cembre
drills type
LD-2E
and
LD-2E-110
are designed and constructed according to EEC
directives 80/1107 and 86/188 relating to the protection of operators against risks arising from
exposure to chemical, physical and biological agents during work, and with particular regard to
the risk of exposure to noise.
This has enabled a range of drills to be manufactured for drilling rails and track equipment, at
reduced noise levels.
The degree of exposure of an operator to noise produced from this equipment depends on the
duration of the loading times and the intervals between exposures, and finally on the number
of holes made within the space of one working day.
For example, an operator using the drill correctly for making holes 19 mm in diam., with a type
RCV 190 broach cutter on rails classified as UIC 60, quality 900, producing up to 400 holes/day,
the daily personal exposure to noise, due solely to the use of the drill, is less than 80 dB (A); under
similar conditions producing 700 holes/day, the daily exposure to noise would be 82.1 dB(A).
Since noise levels vary according to the many different operating conditions,
Cembre
engineers
are available to give further details on the correct use of the drills.
Risks due to vibration
(Directive
2006/42/EC
, Annexe 1, point 2.2.1.1)
The weighted root mean square acceleration value to which the arms of an operator are subjected
when using the drill machine does not exceed 2,5 m/s
2.