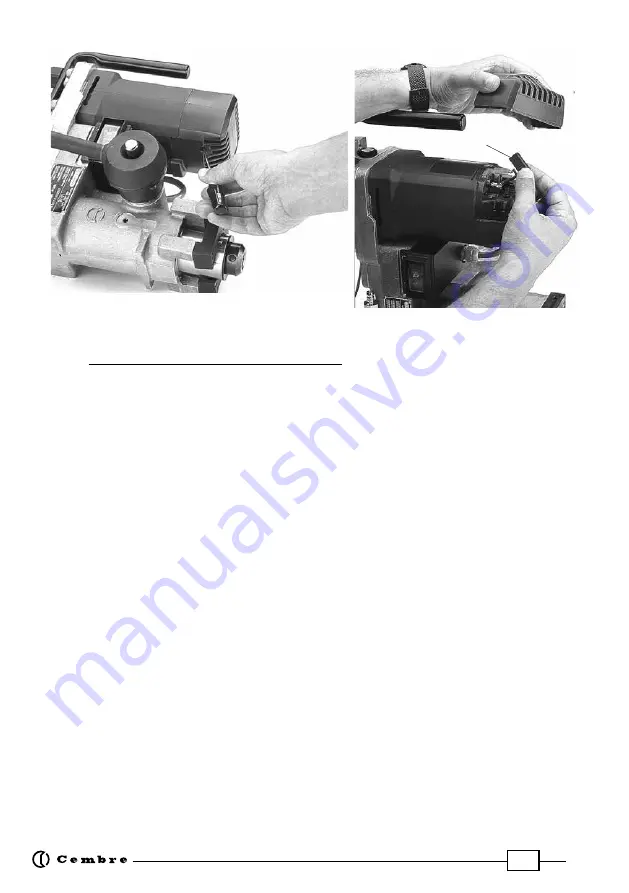
28
APPENDIX “A”
Factors which influence the number of holes that can be made according to the tool used.
– Hardness of the material to be drilled.
– Thickness to be drilled.
– Stability of the drill clamp
and correct assembly of the cutter/bit.
– Suitable lubrocooling (lubrication/cooling)
to keep the temperature of the tool low so as
not to compromise the efficiency of the cutting edges, whilst at the same time facilitating the
removal of the swarf.
– Contact time of the cutting edges of the cutter/bit with the material to be drilled;
bear in mind that the faster the hole is made the greater the efficiency.
– Observance:
1) Commence drilling by exerting light pressure on the advancing lever, progressively
increasing and then relaxing it when the tool is in the exit phase.
2) Avoid pressure jolts and only advance according to the drilling diameter to avoid scratching
the material or damaging the cutting edges of the cutter/bit.
3) Remember that a tool with efficient cutting edges requires a pressure lower than that ap-
plied to one with which a certain number of holes have already been made.
4) When holes are made close to raised lettering on the rails, commence drilling with very
light pressure
until the lettering disappears, to avoid possible breakage of the tool.
5) Bear in mind that when operating on very hard rails, as in the case of quality 1100 steel, it
is advisable to increase the lubrocoolant flow rate.
FIG. 28 – CHANGING THE BRUSHES
Brush
11.3) SPECIAL MAINTENANCE OF THE DRILL
The special maintenance operations require the intervention of qualified personnel only, Please
contact
Cembre
(See
§ 13
).