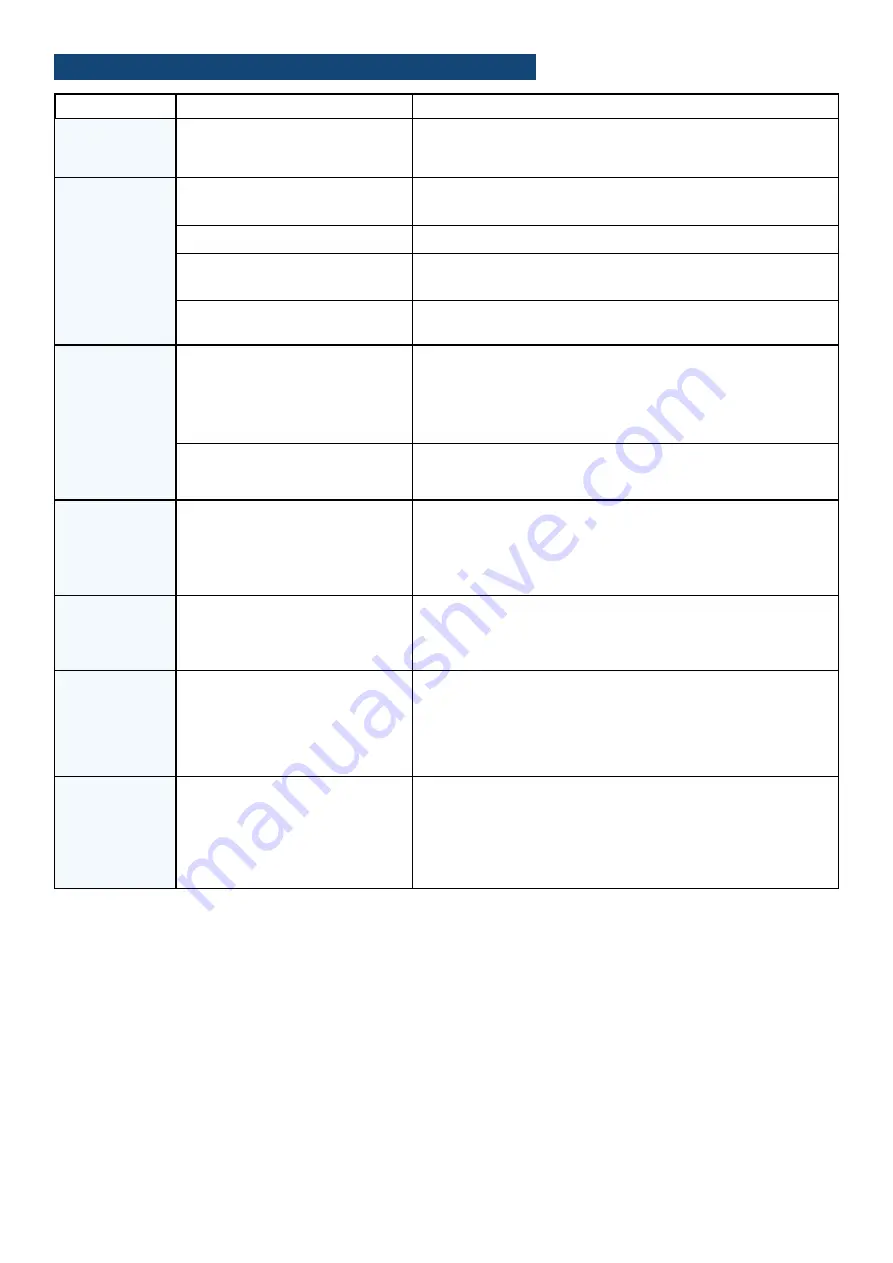
Every care has been taken to ensure the accuracy of the information contained in this publication, but due to continuous development and improvement the right is reserved to supply products
which may differ slightly from those illustrated and described in this publication.
19
www
.ceg.co
www
.ceg.co
www
.ceg.co
www
.ceg.co
www
.ceg.co
Faults
Causes
Solutions
Pump does not
run
Interruption of the power supply,
short circuit or an insulation fault in
the motor coil
Check power supply
Call an expert to check the pump unit
Pump runs,
but little or no
delivery
Pump or pipes are blocked due to
foreign matters
Lack of supply water
Primed incorrectly
Air in suction pipes
Check all filters/check valve for foreign matters
Ensure all taps are turned on
Repeat priming procedure (refer to page 8 for flooded suction or
page 9 for lift suction) to remove any air from the system
Check the tightness of the whole pipe up until the pump and
tighten it
Motor overheats
Low voltage
Ambient temperature above +40 °C
or insufficient ventilation
Ensure power supply is not running on an extended cable
exceeding 10m. Check voltage on terminals of the motor. It should
be within ± 10 % of 230V (this should be carried out only by
qualified personnel)
Relocate pump to a cooler, better ventilated environment
The flow is too
little
Length of pipe is excessive and
diameter is too small
Excessive head
Decrease pipe length and increase pipe size (diameter)
Decrease head on pump
Pump vibrates
Fuse blows or
circuit breaker
trips when pump
starts
Controller failure
light
Incorrectly mounted/fixed
Pump jammed.
Motor stator may be defective,
circuit leakage or insulation failure.
Fuse size or circuit breaker may be
too small
Loss of prime or no water in tank
Electronic controller faulty, maybe
damaged by power surge or spike
Ensure pump is fastened to a solid surface by two mounting
screws
Get pump serviced
Check pump is primed and water supply is sufficient
Replace controller
FAULTS, CAUSES AND SOLUTIONS