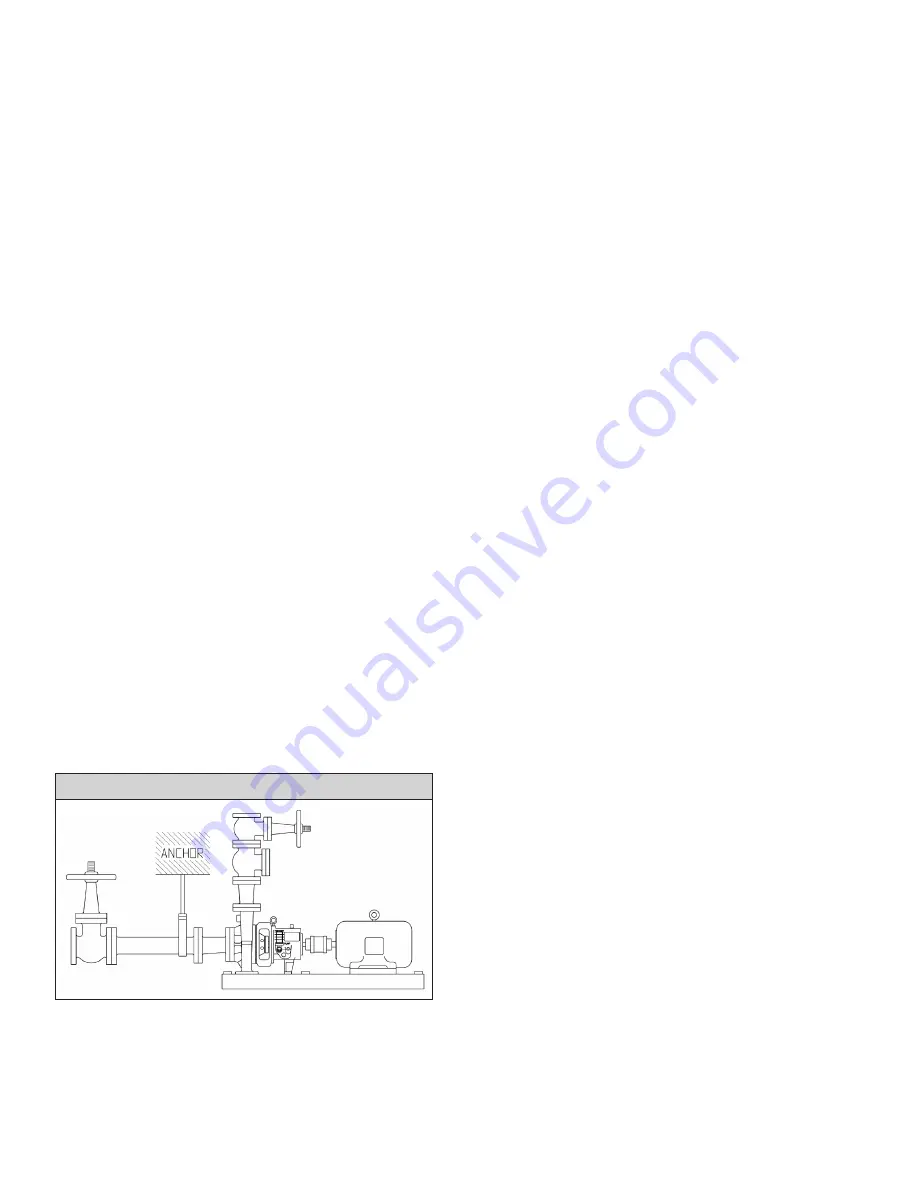
may have forced the pump out of alignment. If so, correct the
piping to remove the distorting load, and realign the pump
and driver.
9) The pump and driver alignment must again be checked at the
operating temperature and alignment corrected under the hot
condition.
10) After about two weeks of normal pump operation the pump
and driver alignment should again be checked under the hot
condition. If alignment is still correct, the driver feet may be
doweled to the baseplate. If the alignment has changed,
realign the unit and recheck after two weeks.
SUCTION AND DISCHARGE PIPING
Suction and discharge nozzle sizes of Dean pumps are selected for
proper performance of the pumping unit and are not intended to
determine the suction and discharge pipe sizes. Pipe sizes must be
determined by the user based on the system requirements.
Suction piping should have a minimum friction loss and thus should
be as short and straight as possible with a pipe diameter as large as
economically feasible for the flow rate handled. Suction piping
should never be smaller in diameter than the suction nozzle size.
When the suction piping is larger than the suction nozzle size an
eccentric reducer is required at the suction flange and must be
installed with the taper located on the underside to eliminate air or
vapor pockets. The section of piping attached to the suction flange
of the pump should be straight for a length of eight pipe diameters
or more.
Discharge piping may be the same size as, larger, or smaller than
the discharge nozzle as the system flow may demand.
In new installations or rebuilt systems, dirt, pipe scale, welding slag,
and general construction debris may get into the piping. It is impor-
tant to prevent this material from entering the pump and damaging
pump parts, mechanical seal faces, or seal chamber packing.
Mechanical seal parts are especially subject to damage even by
very small particles. To prevent damage, a strainer or filter installed
in the suction line is recommended. Commercially available strainers
or filters as recommended by their manufacturers can do an excel-
lent job. In addition, special filtering and mechanical seal flushing
may be required. Consult your Dean representative. Suction line
screens or strainers may usually be removed when, after several
days of use, no dirt has been collected and the system is clean.
of the pump shaft when the unit is running. Although pumps and
drivers are check aligned at the factory, this is only to confirm that
the unit can be aligned in the field and handling during shipment
and installation will cause the alignment to change.
The pump and
driver alignment must always be checked and corrected before the
baseplate is grouted to the foundation and again before the pump
is first started.
If the baseplate mounting instructions have been
carefully fol lowed, no difficulties in making the alignment should
be experi enced.
Failure to properly align the unit will result in
vibra tion, short bearing life,
and reduced mechanical seal or shaft
packing life.
Pumps are not constructed to be used as pipe anchors. Both suc-
tion and discharge piping must be supported independently of the
pumping unit and thermal expansion joints provided to guard
against expansion loads on the pump. Pipes should be anchored
between the expansion joint and the pump and as closely to the
pump as possible. Failure to provide proper piping support and
expansion joints may impose strains on the pump ing unit which
will result in serious misalignment. Maximum allowable piping
loads are shown on page 5 in this manual.
No allowance for thermal expansion is made for motor driven
units in mounting the driver. Allowance for turbine mounting
should be in accordance with the turbine manufacturer’s recom-
mendations.
Final alignment must always be checked and correct-
ed at the operating temperatures of the pump and driver.
Misalignment of the two shafts is of two kinds. The first of these is
angular misalignment where the axis of one shaft is at an angle
from the other. The other is offset alignment where the center of
one shaft is offset from the center of the other shaft. These effects
usually occur together so that both angular and offset misalignment
are present.
Coincident alignment of the driver and pump shaft is measured at
the faces of the coupling hubs. Because of the variety of coupling
types furnished at customer’s request, the procedure here given is
general in nature but may be applied by simple adaption to most
coupling types.
The first step is to remove the spacer from the coupling. To one of
the remaining coupling hubs, firmly seated on the shaft, attach a
dial indicator. Let the indicator button ride on the face of the other
coupling hub and near the outside diameter. See illustration on
page 5. Rotate the shaft on which the dial indicator is mounted,
allowing the indicator button to move on the stationary coupling
hub. The indicator dial movement will show the difference in dis-
tance between the two hubs. This indicates the amount of angular
misalignment between the hubs and therefore the shaft axes.
Good practice suggests alignment to within 0.002" T.l.R.
T
YPICAL
P
UMP
P
IPING
Remember that screens and filters in the suction line are restrictive
devices which reduce the net positive suction head (NPSH) available
to the pump and should be considered at the time the system is
designed.
PUMP AND DRIVER ALIGNMENT
Proper running life of a pump and driver unit depends on the accu-
racy with which the axis of the driver shaft coincides with the axis
4