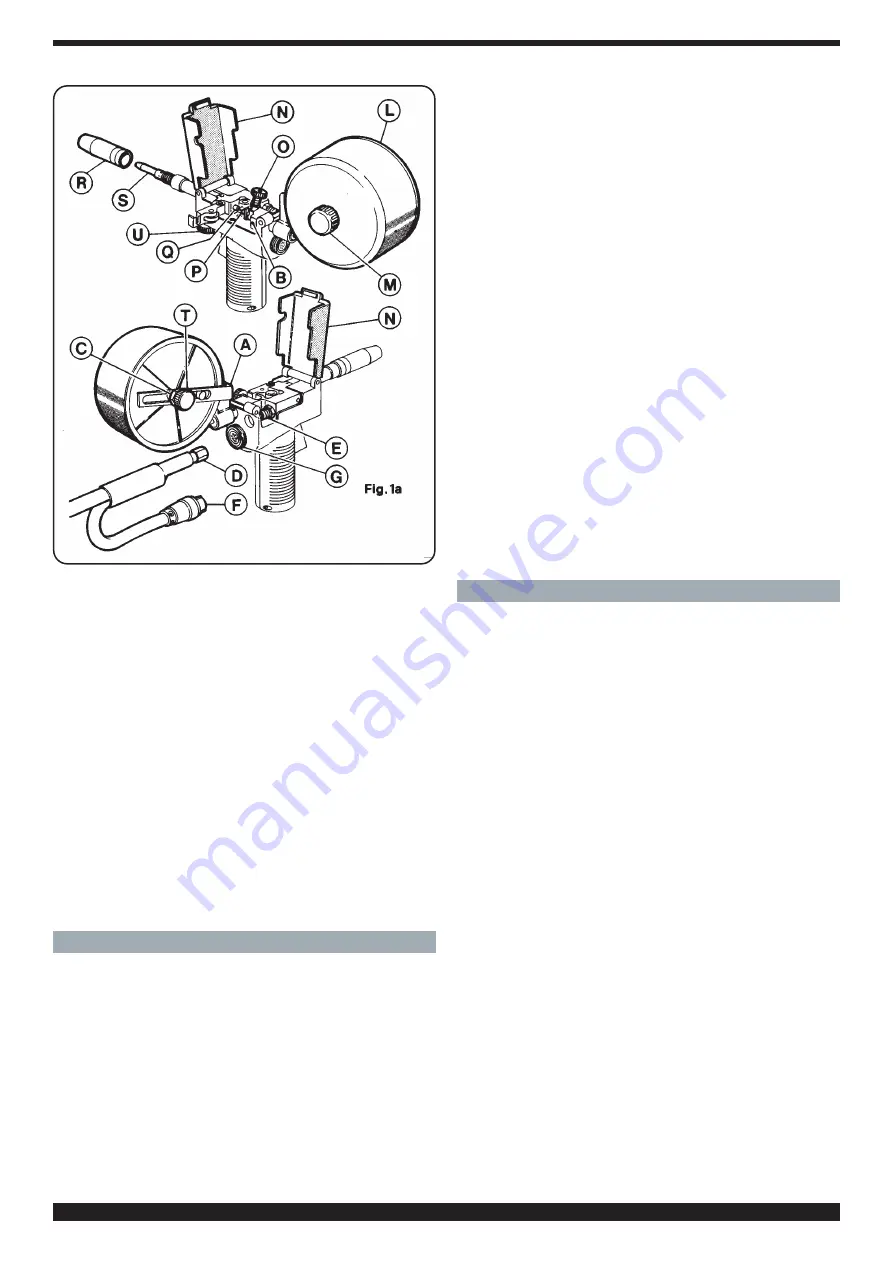
6
A)
Spool Support
B)
Lock screw
C)
Lock nut
D)
Fitting
E)
Fitting
F)
Connector
G)
Connector
H)
Fitting
I)
Connector
L)
Spool cover
M) Knob
N)
Spool cover
O)
Roller presser pin
P)
Teflon tube
Q)
Teflon tube
R)
Gas nozzle
S)
Contact tip
T)
Knob
U)
Wire speed control knob.
4. INSTALLATION
4.1 INSTALLING THE SPOOL-GUN ART 1562
This spool-gun has been designed for use with genera-
tors art. 582 and art. 584 using the extension cable art.
1324. Other set-ups may be used provided that the com-
ponents are compatible.
Turn the spool support (A) to the position required and
lock it in position using the lock screw (B).
Depending on the welding type and location, it may be
necessary to change the maximum rotation angle of the
spool support (A). To change the angle of the spool sup-
port, loosen the lock nut (C) and move the spool contain-
er along the support slot.
Using the spanner supplied, screw the fitting (D) of the
extension cable (art. 1324) to the union (E) of the spool-
gun. Connect the connector (F) of the extension cable to
the connector (G) of the spool-gun.
Connect the extension cable (art. 1324) to the generator
following the instructions given in section 3.5. E2. of the
generator instruction manual.
4.2 INSTALLING THE JAW-FEED WIRE FEED UNIT
ART 1428
This jaw-feed wire feed unit has been designed for exten-
sion to generators art. 582 and art. 584 using the exten-
sion cable art. 1324. Other set-ups may be used provid-
ed that the components are compatible.
Screw the fitting (D) of the extension cable (art 1324) to
the wire feed unit fitting (H). Plug the connector (G) of the
extension cable into the wire feed unit connector (I).
Connect the extension cable (art. 1324) to the generator
following the instructions given in section 3.5.E2. of the
generator instruction manual.
Select a wire-feed roller with a suitable groove. Fit the
wire spool. Insert the wire into the wire drive motor and
ensure that the wire-feed roller groove and the wire are
aligned.
Connect up the welding torch.
5. WELDING GUIDELINES
5.1
MILD STEEL WELDING
To weld mild steel use 75% Argon + 25% CO2 or 100%
CO2.
Select the welding voltage you require by means of the
welding voltage switch on the generator.
Approach the point to be welded and press the torch
push button (70).
• Adjust the potentiometer (U) (see figs. 1a and 1b) until
the welding noise is constant and continuous.
If the speed is too high, the wire will tend to get stuck on
the workpiece causing the torch to bounce back.
If the speed is too slow, the wire will melt irregularly or
else the arc will switch off.
When you have finished welding, switch off the machine
and shut off the gas bottle.
For the correct welding angle, see figure 2.
5.2 ALUMINIUM WELDING
The machine set-up for aluminium is the same as that for
mild steel with the following differences:
1.100% Argon as welding protection gas.
2. Wire of composition suitable for the material to be
welded.
- To weld ALUMAN, use 3÷5% silicon wire.
- To weld ANTICORODAL, use 3÷5% silicon wire.
- To weld PERALUMAN, use 5% magnesium wire.
- To weld ERGAL, use 5% magnesium wire.
Note for Jaw-feed wire feed unit art.1428
If you are using a torch suitable for steel wire welding, the
same must be modified as follows:
Summary of Contents for JAW-FEED
Page 19: ...19 SPOOL GUN ART 1562...
Page 21: ...21 JAW FEED ART 1428...
Page 23: ...23 JAW FEED ART 1428...
Page 24: ...24...