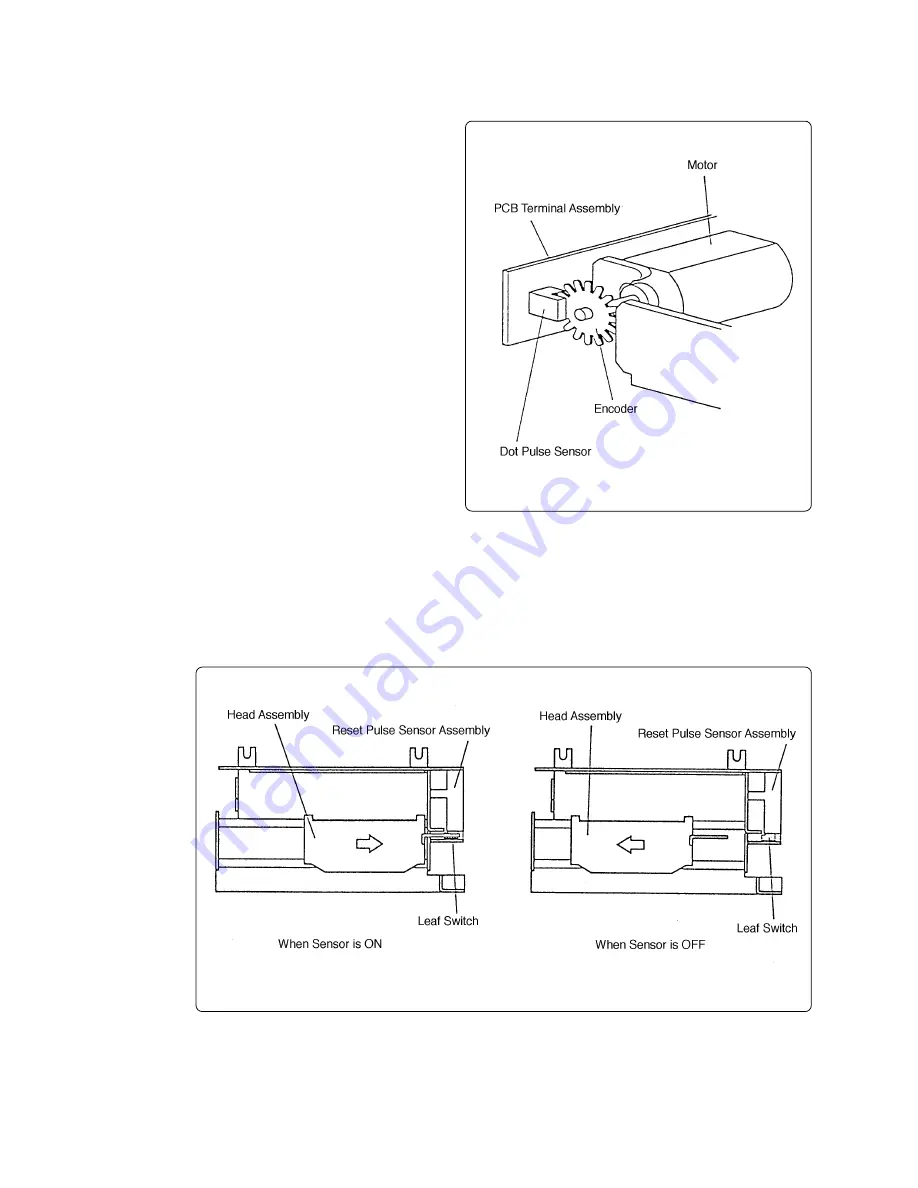
— 4 —
2-3-2 Sensor mechanisms
This mechanism has two sensors for de-
tection, a dot pulse sensor and a reset
pulse sensor.
(1) Dot pulse sensor
The dot pulse sensor consists of an
encoder (slit disk) directly connected
to the motor and a photointerrupter
reading the rotation. The rotation read
(number of slits counted) is treated as
the DP signal that is the core of the
printing control.
(2) Reset pulse sensor
The reset pulse sensor uses a leaf switch which turns ON/OFF according to the head assem-
bly position.
This sensor detection signal represents the RP signal that specifies the print head home posi-
tion and printing start base position.
Summary of Contents for MD-910
Page 1: ...DOT PRINTER JAN 1997 MD 910 without price TECHNICAL MANUAL ...
Page 32: ......
Page 33: ...MA0201571A ...