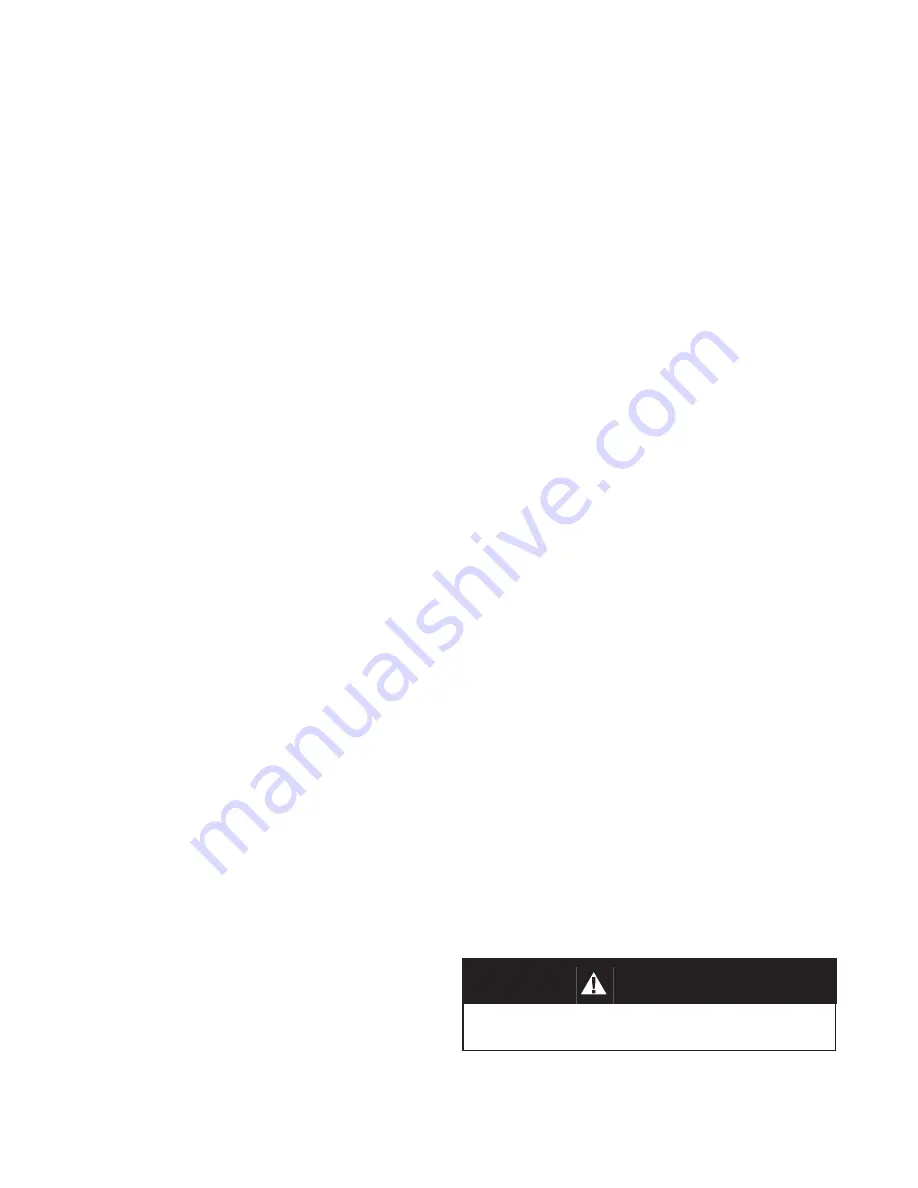
2
IOM-8311HP/LP
SECTION III
2. If the regulator and system are to both be shut down,
slowly close the inlet (upstream) block valve. Close the
outlet (down stream) valve only if regulator re mov al is
re quired.
Do not walk away and leave a bypassed regulator
unattended!
V. SHUTDOWN
1. On systems with a bypass valve, and where system
pressure is to be maintained as the reg u la tor is shut
down, slowly open the bypass valve while closing the inlet
(up stream) block valve. Fully close the inlet (up stream)
block valve. (When on bypass, the system pres sure
must be con stant ly ob served and manually regulated.)
Close the outlet (downstream) block valve.
SECTION V
IV. START-UP
1. Start with the block valves closed. A bypass valve may
be used to maintain inlet pressure in the upstream
system without chang ing the fol low ing steps.
2. Relax the range spring by turning the adjusting screw
counter clockwise (CCW) (viewed from above) a min-
i mum of three (3) full revolutions. This re duc es the inlet
(upstream) pres sure set point.
3. If it is a “hot” piping system, and equipped with a bypass
valve, slowly open the bypass valve to preheat the sys-
tem piping and to allow slow ex pan sion of the piping.
Ensure proper steam trap operation, if installed. Close ly
monitor inlet (upstream) pressure via gauge to ensure
not over-pres sur iz ing.
NOTE:
If no bypass valve is
in stalled, extra caution should be used in starting up a
cold system; i.e. do everything slowly.
4. Crack open the inlet (upstream) block valve.
5. Slowly open the outlet (downstream) block valve ob-
serv ing the inlet (upstream) pressure gauge. De ter mine if
the regulator is
fl
owing. If not, slowly rotate the regulator
adjusting screw counter clock wise (CCW) (viewed from
above) until
fl
ow be gins.
6. Continue to slowly open the outlet (downstream) block
valve until fully open.
7. Observing the inlet (upstream) pressure gauge, rotate
the adjusting screw clockwise (CW) slowly until the inlet
pressure begins to rise. Rotate CW until the desired
setpoint is reached.
8. Continue to slowly open the inlet (upstream) block valve.
If the inlet (upstream) pressure exceeds the desired
setpoint pressure, rotate the adjusting screw CCW until
the pressure decreases.
9. When
fl
ow is established steady enough that both the
outlet and inlet block valves are fully open, begin to
slowly close the bypass valve, if in stalled.
10. Develop system
fl
ow to a level near its expected normal
rate, and reset the regulator setpoint by turning the
adjusting screw CW (viewed from above) to increase
inlet pressure, or CCW to reduce inlet pressure.
11. Reduce system
fl
ow to a minimum level and observe
setpoint. Inlet pressure will rise from the set point of Step
10. The maximum rise in outlet pressure on decreas-
ing
fl
ow should not exceed the stated upper limit of the
range spring by greater than 10%; i.e. 10-40 psig (.69-
2.76 Barg) range spring, at low
fl
ow the outlet pressure
should not exceed 44 psig (3 Barg). If it does, consult
factory.
SECTION IV
III. PRINCIPLE OF OPERATION
1. Movement occurs as pressure variations register on
the diaphragm. The registering pressure is the inlet
P
1
, or upstream pressure. The range spring opposes
di a phragm movement. As inlet pressure drops, the range
spring pushes the di a phragm down, closing the ports;
as inlet pres sure increases, the di a phragm push es up
and the ports open.
2. A complete diaphragm failure will cause the reg u la tor
to fail closed.
11. Regulators are not to be direct buried un der ground.
12. For insulated piping systems, recommendation is to not
insulate regulator.
10. Basic Regulator - (Refer to Figure 1): Regulator may
be rotated around the pipe axis 360°. Rec om mend ed
position is with spring chamber ver ti cal upwards. Orient
such that the spring chamber vent hole does not collect
rainwater or debris.
CAUTION