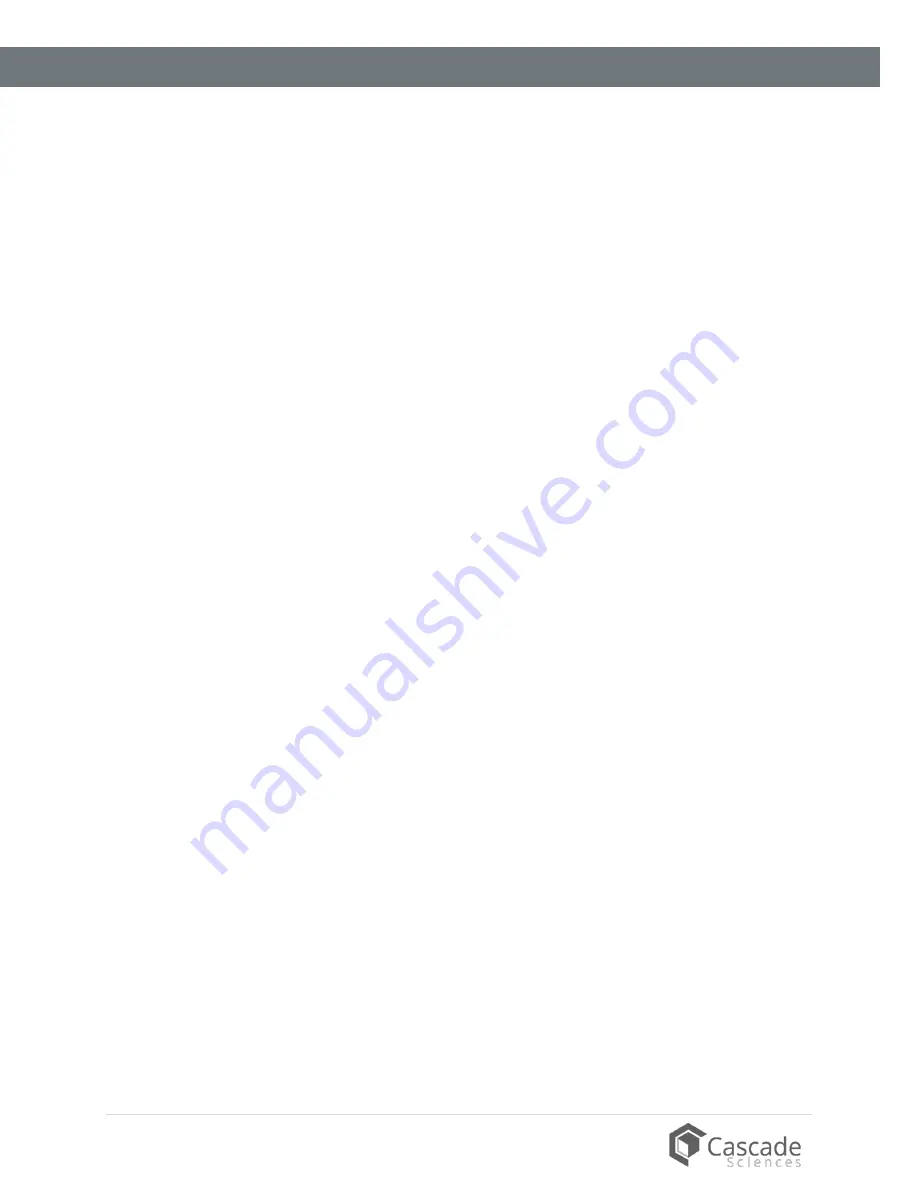
2 |
P a g e
cascadesciences.com
|
Tel. 503 847-9047
Depicted on the front cover:
CVO-5-EX-SS
User Manual Limitation
This manual is designed to provide general information as it relates to the safe operation and
understanding of the vacuum oven. It does not cover all possible applications and use. Cascade
Sciences will not be held liable or responsible for damages resulting from the use of this manual or
the vacuum oven.
Power Cord Plug-In Location Requirement
CVO-5-EX-SS ovens that come with power cords must plug into a power outlet located safely
outside of the hazardous location zone the oven will be installed in. This is to prevent the possibility
of sparking in the presence of potentially explosive concentrations of hazardous gases or vapors.
The outlet must also meet the other electrical safety requirements described in this manual. The
supplied power cord is 15-feet long (4.6 meters).
Hardwire Connection Location Requirements
CVO-5-EX-SS ovens with hardwire power feeds may be wired to a power source inside the
hazardous location Zone. However, this connection must meet all applicable electrical safety
standards requirements Zone 2 or Class 1 Zone 2 or Class 1 Division 2 hazardous (classified)
locations. Additionally, the connection must be made by a qualified electrical service technician who
is competent to work in the hazardous location zone and with these equipment types.
Summary of Contents for CVO-5-EX Series
Page 1: ...Flammable Solvent Ovens Installation Operation Manual CVO 5 EX Oven Series...
Page 6: ...6 P a g e cascadesciences com Tel 503 847 9047 Special Conditions Of Use 131...
Page 7: ...7 P a g e cascadesciences com Tel 503 847 9047 TABLE OF CONTENTS...
Page 11: ...11 P a g e cascadesciences com Tel 503 847 9047 SAFETY CERTS AND STATEMENTS...
Page 17: ...17 P a g e cascadesciences com Tel 503 847 9047 SPECIFICATIONS...
Page 22: ...22 P a g e cascadesciences com Tel 503 847 9047...
Page 24: ...24 P a g e cascadesciences com Tel 503 847 9047 These groups include propane and n butane...
Page 29: ...29 P a g e cascadesciences com Tel 503 847 9047 Continued next page...
Page 37: ...37 P a g e cascadesciences com Tel 503 847 9047 INTRODUCTION...
Page 39: ...39 P a g e cascadesciences com Tel 503 847 9047...
Page 44: ...44 P a g e cascadesciences com Tel 503 847 9047 RECEIVING...
Page 51: ...51 P a g e cascadesciences com Tel 503 847 9047 Continued next page...
Page 54: ...54 P a g e cascadesciences com Tel 503 847 9047 Continued next page...
Page 61: ...61 P a g e cascadesciences com Tel 503 847 9047 End of Procedure...
Page 65: ...65 P a g e cascadesciences com Tel 503 847 9047 INSTALLATION...
Page 67: ...67 P a g e cascadesciences com Tel 503 847 9047 SYMBOLS...
Page 69: ...69 P a g e cascadesciences com Tel 503 847 9047 Continued next page...
Page 72: ...72 P a g e cascadesciences com Tel 503 847 9047 Continued next page...
Page 95: ...95 P a g e cascadesciences com Tel 503 847 9047 End of Procedure...
Page 104: ...104 P a g e cascadesciences com Tel 503 847 9047 End of Procedure...
Page 116: ...116 P a g e cascadesciences com Tel 503 847 9047 End of Procedure...
Page 123: ...123 P a g e cascadesciences com Tel 503 847 9047 Continued next page...
Page 125: ...125 P a g e cascadesciences com Tel 503 847 9047 Continued next page...
Page 127: ...127 P a g e cascadesciences com Tel 503 847 9047 End of Procedure...
Page 128: ...128 P a g e cascadesciences com Tel 503 847 9047 MAINTENANCE...
Page 130: ...130 P a g e cascadesciences com Tel 503 847 9047 REPLACEMENT PARTS...
Page 132: ......