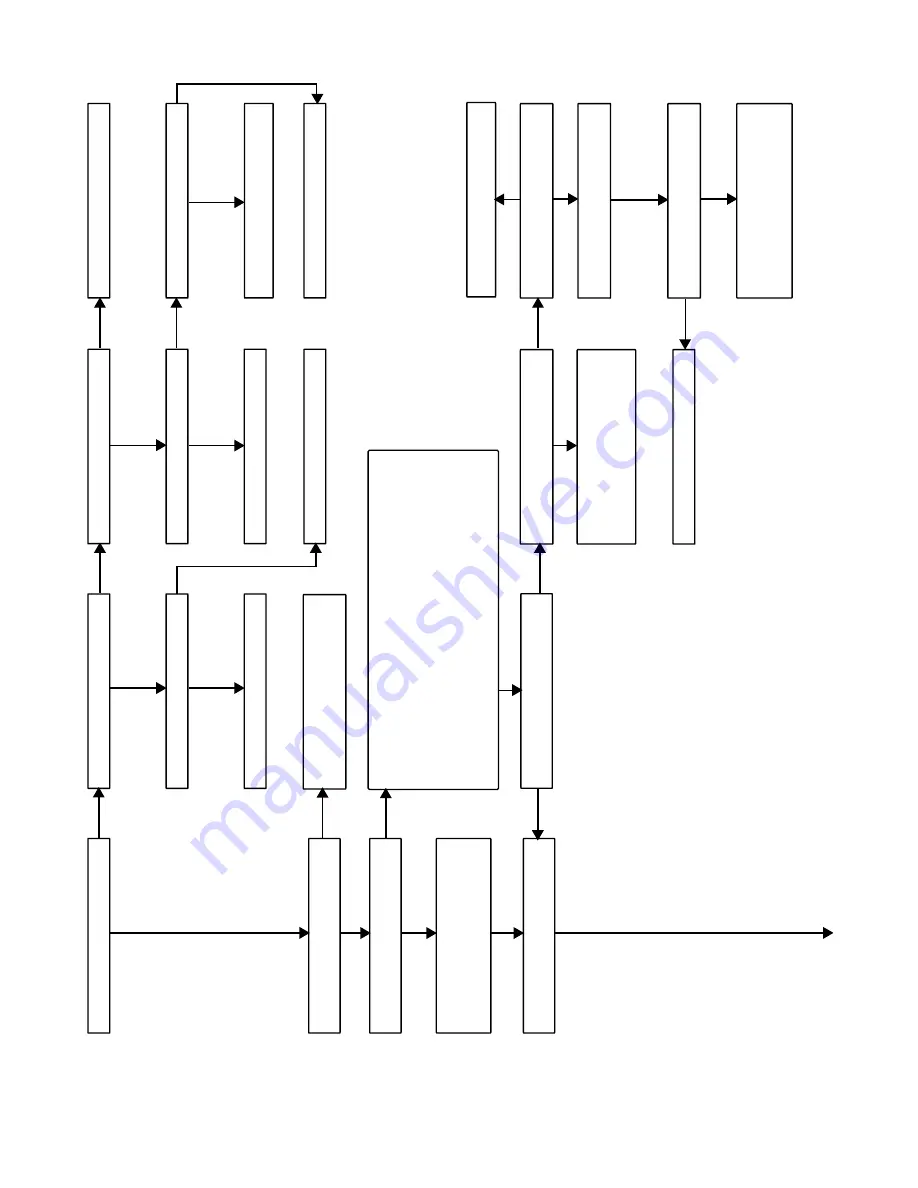
A02204a
Is LED status light on?
Is LED status light b
linking r
apidly without a
pause?
Is LED status light b
linking ON/OFF slo
wly
with a combination of shor
t and long flashes?
Deter
mine status code
.
The status code is a
2 digit n
umber with the first digit deter
mined
b
y
the n
umber of shor
t flashes and the second
digit b
y
the n
umber of long flashes?
Go to section belo
w f
or the status code that
w
as flashed.
Is there 115V at L1 and L2?
Is there 24V at SEC-1 and SEC-2?
Replace fur
nace control.
Chec
k f
or correct line v
oltage polar
ity
. If units
are twinned, chec
k f
or proper lo
w-v
oltage
(24V) tr
ansf
or
mer phasing.
T
o
recall status code br
iefly remo
v
e
and reconnect one RED wire from the Limit
Switch or Flame Rollout s
witch to displa
y stored status code
. On RED LED
control do not remo
v
e
po
w
er or b
lo
w
er access panel bef
ore initiating status
code recall.
Y
ou can also recall the pre
vious status code b
y
momentar
ily shor
ting
the
TEST/TWIN ter
minal to Com24V ter
minal until the LED goes out.
LED will
flash the pre
vious status code or status code #11 (1 shor
t and 1 long flash) if
there w
as no pre
vious code
. After the control repeats the code 4 times
, the
control will go through a br
ief component test sequence
.
The inducer will star
t
and r
un f
or the entire component test.
The HSI, b
lo
w
er motor F
AN speed
(AMBER LED boards only) HEA
T speed, and COOL speed will r
un f
or 10
–
15
seconds each.
Gas v
alv
e and humidifier will not be tur
ned on.
W
as there a pre
vious status code
other than #11?
Is door s
witch closed?
Is there 115V going to s
witch?
Replace door s
witch.
Replace tr
ansf
or
mer
.
Does the control respond to
W
, Y1 (if present),
Y/Y2, and G (24V) ther
mostat signals?
Run system through a heating or cooling cycle
to chec
k oper
ation.
Status codes are er
ased
after 72 hours
. On RED LED boards stored
status codes can also be er
ased whene
v
e
r
(115V or 24V) is interr
upted.
Replace fur
nace control.
Close door s
witch and go bac
k to ST
AR
T
.
Is circuit break
er closed?
Chec
k f
or contin
uity in wire from circuit break
er
to fur
nace
.
Close circuit break
er and go bac
k to ST
AR
T
.
Chec
k room ther
mostat or
interconnecting cab
le
.
Is 24V present at
W
,
Y1 (if present),
Y/Y2 or
G ther
mostat ter
minals on the fur
nace control?
Disconnect all the ther
mostat wires from the
fur
nace control.
Does the prob
lem repeat when using
a jumper wire?
The ther
mostat is not compatib
le with the
fur
nace control.
Either install a ballast resistor
,
connect the Com24V ther
mostat ter
minal to
the ther
mostat, or replace the ther
mostat.
NO
YES
YES
NO
NO
YES
YES
YES
YES
NO
YES
YES
NO
YES
NO
YES
NO
NO
NO
YES
NO
YES
NO
ST
AR
T
TR
OUBLESHOO
TING GUIDE
NO
14