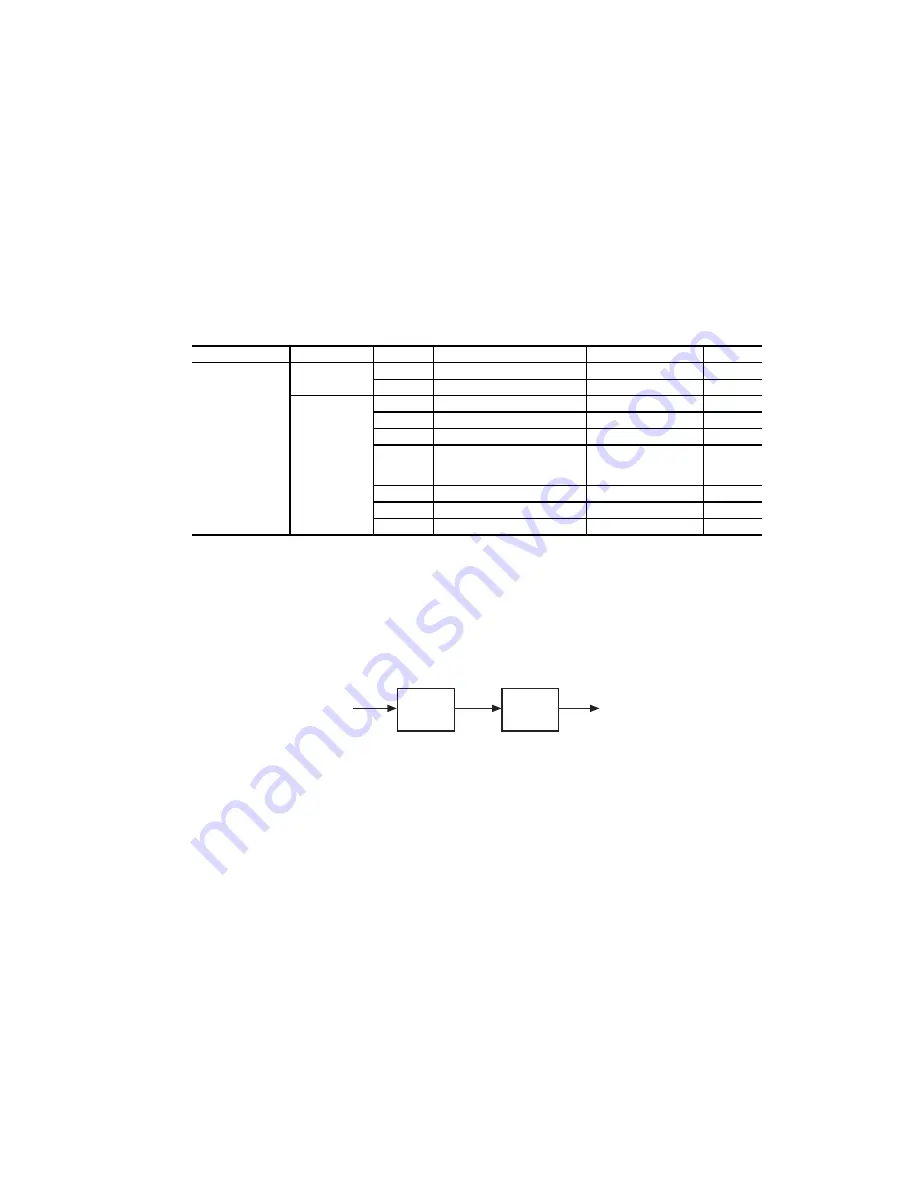
53
Duplex Chiller Control Configuration —
See
Fig. 36-39 and Table 6. The dual chiller routine is available for
the control of two units supplying chiller fluid on a common
loop. One chiller must be configured as the master chiller, the
other as the slave chiller. The module B chiller is the master
and the module A chiller is the slave.
NOTE: Chiller module B must be configured on site as the
master chiller and module A must be configured on site as the
slave chiller for all 30GXN,R duplex chiller applications. Field
installation of communication wiring is required. Connections
can be made to the CCN screw terminals on TB3 in both
chillers.
The master chiller will be configured with a slave chiller at
address 2. The chillers will be configured for series fluid flow.
The master and slave chillers cannot have the same CCN
address (CCNA, Configuration mode under OPT2). In addi-
tion, the chillers must reside on the same CCN bus. The master
chiller controls the slave chiller by changing its mode (STAT,
control mode) and its operating setpoint (CTPT, control point).
Any energy management functions need only be connected to
the Master chiller. The EMM accessory has to be installed in
the Master chiller only.
The master chiller is now configured for dual chiller opera-
tion. To configure the slave chiller, only the LLEN, MSSL, and
PARA variables need to be set. Set the Lead Lag Enable
(LLEN) variable to ENBL. Set the Master Slave Select
(MSSL) variable to SLVE. Set the Parallel (PARA) variable to
NO. The variables SLVA, LLBL, LLBD and LLDY are not
used by the slave chiller.
Table 6 — Duplex Configuration
LEGEND
N/R — Not Required
*Set to desired control method: switch (0); 7-day occupancy (1); CCN occupancy (2); CCN (3). Slave is
always configured to switch (0).
†Optional.
MODE
SUB-MODE
ITEM
DESCRIPTION
MASTER
SLAVE
Configuration
OPT2
CTRL
Controls Method
Switch*
Switch*
CCNA
CCN Address
1
2
RSET
LLEN
Lead/Lag Chiller Enable
ENBL
ENBL
MSSL
Master/Slave Select
MAST
SLVE
SLVA
Slave Address
2
N/R
LLBL†
Lead/Lag Balance Select
Master Leads - 0;
Slave Leads - 1;
Automatic - 2
N/R
LLBD†
Lead/Lag Balance Data
168 hrs.
N/R
LLDY†
Lag Start Delay
5 min.
N/R
PARA
Parallel Configuration
No
No
RETURN
FLUID
LEAVING
FLUID
SLAVE
CHILLER
(module A)
MASTER
CHILLER
(module B)
Fig. 39 — Dual Chiller Piping Arrangement,
Series Fluid Flow
Summary of Contents for ECOLOGIC 30GXN
Page 3: ...3 Fig 1 Dimensions 30GXN R080 090 Cast iron Steel ...
Page 4: ...4 Fig 2 Dimensions 30GXN R083 093 106 108 114 125 135 Cast iron Steel ...
Page 5: ...5 Fig 3 Dimensions 30GXN R118 128 138 150 160 Cast iron Steel ...
Page 6: ...6 Fig 4 Dimensions 30GXN R153 174 Cast iron Steel ...
Page 7: ...7 Fig 5 Dimensions 30GXN R163 178 Cast iron Steel ...
Page 8: ...8 Fig 6 Dimensions 30GXN R204 225 Cast iron Steel ...
Page 9: ...9 Fig 7 Dimensions 30GXN R208 228 Cast iron Steel ...
Page 10: ...10 Fig 8 Dimensions 30GXN R249 264 Cast iron Steel ...
Page 11: ...11 Fig 9 Dimensions 30GXN R253 268 Cast iron Steel ...
Page 12: ...12 Fig 10 Dimensions 30GXN R281 301 325 350 Cast iron Steel ...
Page 13: ...13 Fig 11 Dimensions 30GXN R283 ...
Page 14: ...14 Fig 12 Dimensions 30GXN R303 ...
Page 15: ...15 Fig 13 Dimensions 30GXN R328 ...
Page 16: ...16 Fig 14 Dimensions 30GXN R353 ...
Page 17: ...17 Fig 15 Dimensions 30GXN R370 ...
Page 18: ...18 Fig 16 Dimensions 30GXN R373 ...
Page 19: ...19 Fig 17 Dimensions 30GXN R390 ...
Page 20: ...20 Fig 18 Dimensions 30GXN R393 418 ...
Page 21: ...21 Fig 19 Dimensions 30GXN R415 ...
Page 22: ...22 Fig 20 Dimensions 30GXN R450 ...
Page 23: ...23 Fig 21 Dimensions 30GXN R453 ...
Page 24: ...24 Fig 22 Dimensions 30GXN R475 ...
Page 25: ...25 Fig 23 Dimensions 30GXN R478 ...
Page 26: ...26 Fig 24 Dimensions 30GXN R500 525 ...
Page 27: ...27 Fig 25 Dimensions 30GXN R503 528 ...
Page 73: ......