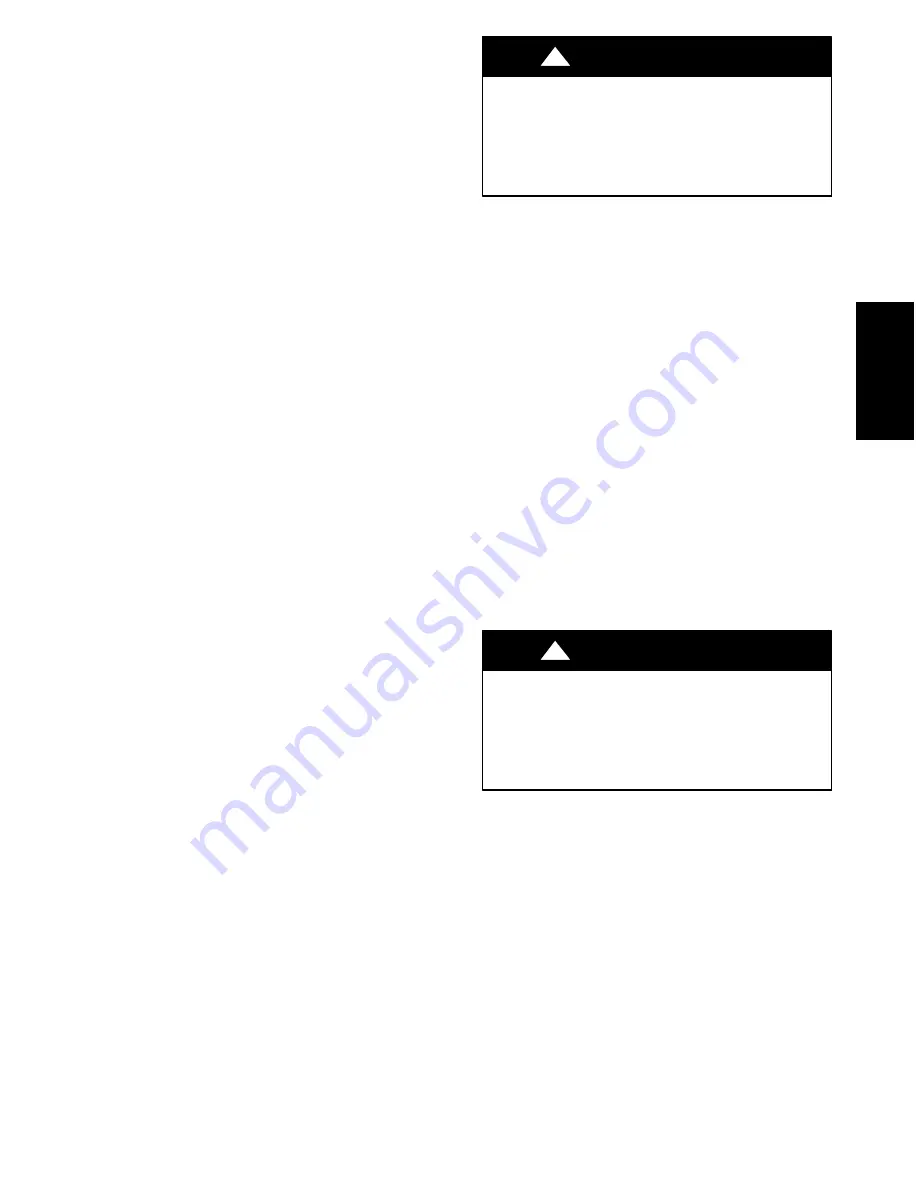
13
23. Reconnect the blue wires removed in item 5 to the rollout
switch and reinstall the rollout switch.
24. Reconnect orange sparker cable to sparker and reconnect
the yellow flame sensor wire to the flame sensor.
25. Reconnect the gray and brown wires removed in item 5 to
the gas valve.
26. Slide burner rack assembly into base pan. Align burner rack
with screws on sheet metal partition and slide assembly
back tight to the partition. Replace the screw attaching the
burner rack to the base pan removed in step 4. If the fan
partition mounting bracket was removed, slide bracket back
into place and fasten with 2 screws (see Fig. 2).
27. Reconnect the brown wire from the burner assembly to the
fan partition panel, using the ground screw saved from step
8.
28. Remove the 1/8 in. pipe plug on the gas manifold and
connect a pressure manometer (see Fig. 17).
29. Reconnect electrical power and gas supply to the unit. For
propane applications, the gas pressure must not be less than
11.0 IN. W.C. or greater than 13 IN. W.C. at the unit
connection. A 1/8--in. NPT plugged tapping, accessible for
test gauge connection, must be installed immediately
upstream of the gas supply connection to the gas valve and
downstream of manual equipment shutoff valve.
The newly installed low gas pressure switch is a safety device used
to guard against adverse burner operating characteristics that can
result from low gas supply pressure. Switch opens at not less than
6.5 IN. W.C. and closes at not greater than 10.2 IN. W.C.
This switch also prevents operation when the propane tank level is
low which can result in gas with a high concentration of impurities,
additives, and residues that have settled to the bottom of the tank.
Operation under these conditions can cause harm to the heat
exchanger system.
This normally open switch closes when gas is supplied to gas valve
under normal operating pressure. The closed switch completes
control circuit. Should an interruption or reduction in gas supply
occur, the gas pressure at switch drops below low gas pressure
switch setting, and switch opens. Any interruption in control
circuit (in which low gas pressure switch is wired) quickly closes
gas valve and stops gas flow to burners.
FIRE AND EXPLOSION HAZARD
Failure to follow this warning could result in personal
injury and/or property damage.
Never test for gas leaks with an open flame. Use a
commercially available soap solution made specifically for
the detection of leaks to check all connections.
!
WARNING
IMPORTANT
: Restart unit and leak check all gas connections
including the main service connection, gas valve, gas spuds, and
manifold pipe plug. All leaks must be repaired before firing unit.
30. Fire unit and verify proper ignition and proper sequence of
operation (Table 6). See Table 4 for proper manifold pres-
sure setting for your unit. Adjust the gas valve setting by
turning the plastic adjustment screws clockwise to increase
pressure and counter--clockwise to decrease pressure. Refer
to Table 7 for required rated heating input rates. Replace
regulator cover screws when finished (see Fig. 14).
31. With control access panel removed, observe unit heating
operation. Watch burner flames to see if they are blue in ap-
pearance, and that the flames are approximately the same for
each burner (see Fig. 18).
32. Turn off unit, remove pressure manometer and replace the
1/8 in. pipe fitting on the gas manifold (see Fig. 17).
33. Attach warning label (P/N 48DU500076) to visible side of
gas valve.
34. Attach conversion label (P/N 48VL500206) above unit
rating plate on exterior of unit.
35. Attach completed conversion responsibility label (see Fig.
10, P/N 48VL500207) inside control access panel.
IMPORTANT
: Restart unit and leak check all gas connections
including the main service connection, gas valve, gas spuds, and
manifold pipe plug.
FIRE AND EXPLOSION HAZARD
Failure to follow this warning could result in personal
injury and/or property damage.
Never test for gas leaks with an open flame. Use a
commercially available soap solution made specifically for
the detection of leaks to check all connections.
!
WARNING
36. After all leaks are eliminated, replace control access panel.
CPL
P
CONV