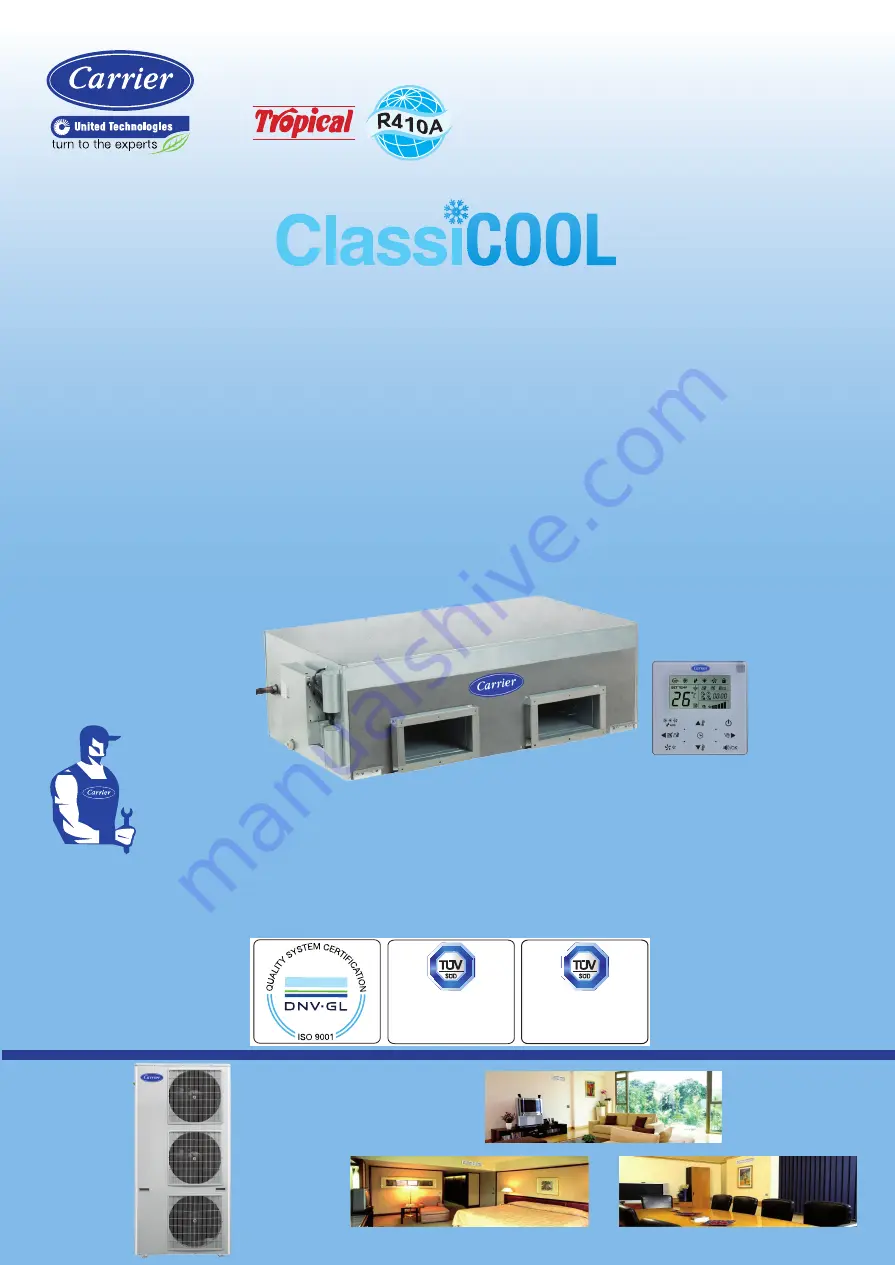
Rev. (0) - 2014
Rev. (0) - 2016
Enviromental
Management System
ISO 14001 : 2004
Certificate No : 12 104 30334 TMS
Safety
Management System
BS OHSAS 18001 : 2007
Certificate No : 12 116 30334 TMS
53KDHT60N-518
53KDHT72N-518
53KDHT84N-518
53KDHT90N-518
03504154
INSTALLATION MANUAL
Miraco
Miraco
MISR REFRIGERATION & AIR CONDITIONING MFG. CO.
380-420V ~ 50Hz 3Ph
Carrier is committed for continuous improvement of Carrier products according to national and international standards
to ensure the highest quality and reliability standards, and to meet market regulations and requirements.
All specifications subject to change without prior notice according to Carrier policy of continuous development.
Ceiling Concealed Ducted Split Systems
High Efficiency - Green
Cool Only
Summary of Contents for ClassiCOOL 53KDHT60N-518
Page 57: ......