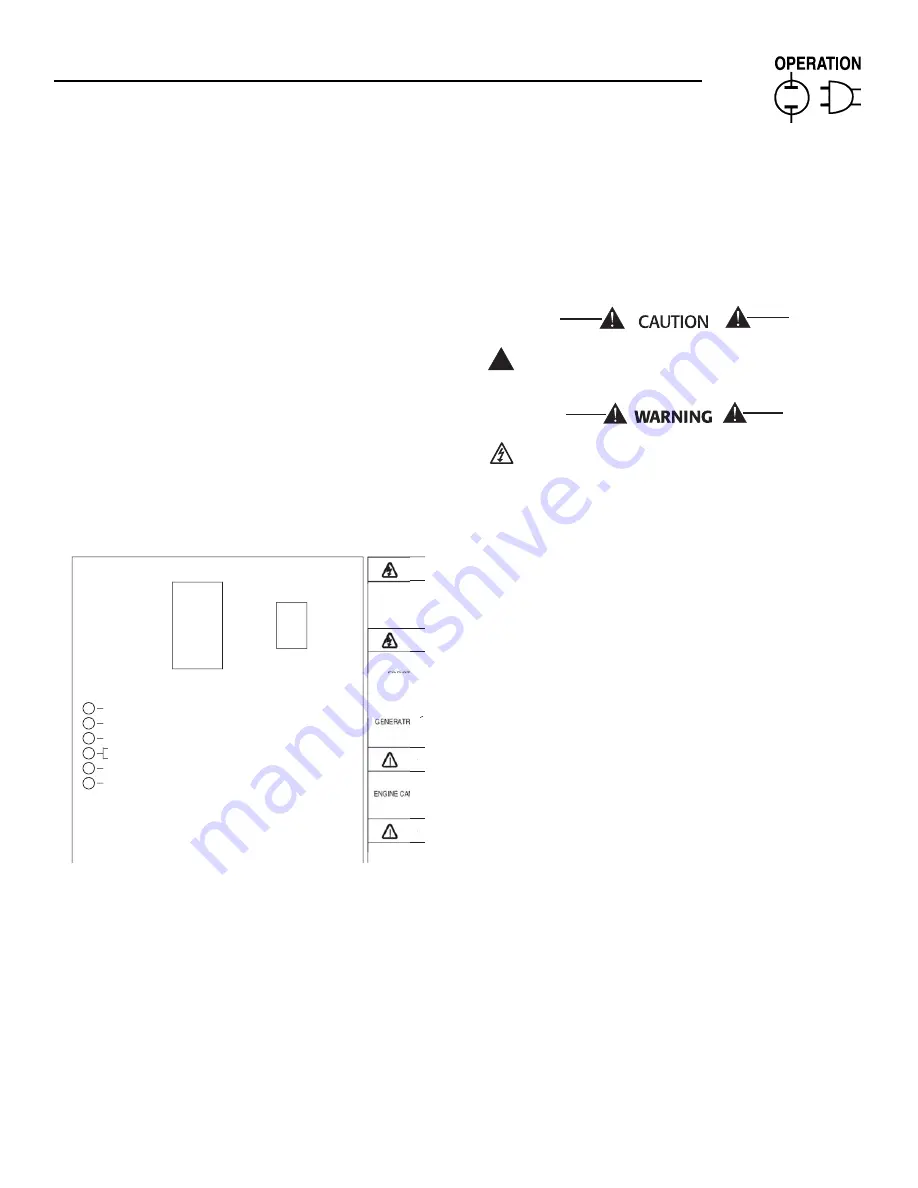
Carrier
15
Section 3 - Operation
Carrier Liquid-cooled 25 kW Generator
3.6
WEEKLY EXERCISE CYCLE
The engine control board will start and run the gen-
erator once every seven days for approximately 12
minutes. If utility should fail during this exercise
period, the engine control board will transfer the load
to the generator output and continue to run until util-
ity returns.
On the day, and at the time of day chosen for the gen-
erator to exercise, set the weekly exercise cycle as fol-
lows:
1. Place the AUTO/OFF/MANUAL switch in the auto
position (Figure 3.3).
2. Press and hold the “Set Exercise” switch for five
seconds, then release.
At this time all five red LEDs will flash for approxi-
mately 10 seconds, then the engine will start and run
for it’s 12 minute exercise period, then shut down.
The generator will now start and run each week at the
same time.
Figure 3.3 - “Set Exercise Time” Switch
If DC power to the control board is lost, the weekly
exercise setting will be lost. This is indicated by all
five red LEDs continually flashing. In this state the
generator will still start and run in manual mode, or
automatically start and run if utility is lost while in
Auto mode, but it will not perform a weekly exercise
cycle.
If a failure occurs while running in this mode, the five
red LEDs will stop flashing, the individual fault LED
will turn on and the engine will shut down. Once the
AUTO/OFF/MANUAL switch has been switch to OFF,
the individual fault LED will turn OFF and the five
red LEDs will begin flashing to show exercise has still
not been set.
3.7
CONTROL BOARD DIP SWITCH
SETTINGS
Located on the control board is an eight position DIP
switch (see Figure 3.2). The eight different switches,
are used to configure the control board for the spe-
cific engine and governor being used and are pre-set
at the factory.
If the DIP switch settings are not set correctly,
the generator may not start or operate correct-
ly.
240 VAC can be present within the control
panel.
If it is necessary to select an alternate switch position,
move the AUTO/OFF/MANUAL switch to the OFF
position. Remove the 5 amp and 15 amp fuses in the
generator control panel. Move the DIP switch position
that needs to be changed to its new position. Wait five
seconds, then re-install the 5 and 15 amp fuses.
The ON position is marked on the switch and the fac-
tory settings are also shown in Figure 3.3.
Switch Position 1
— Selects the generator alternator
output frequency and is factory pre-set for 60 Hz.
Switch Position 2
— Selects the type of transfer
switch and is factory pre-set for the prepackaged
transfer switch.
Switch Position 3
— Selects the type of governor
control used and is factory pre-set for stepper motor
control.
Switch Position 4
— Selects the type of fuel being
used and is factory pre-set for natural gas (NG).
Switch Position 5
— Selects the engine displacement
and is factory pre-set for a 2.5 liter (2.5L) engine.
Switch Position 6
— Selects the number of engine
cylinders and is factory pre-set for four cylinders.
Switch Position 7
— Selects the direction of rotation
of the governor stepper motor and is factory pre-set
for CCW rotation (rotation is observed looking at the
stepper shaft as it move from closed throttle to open
throttle).
Switch Position 8
— Selects whether the control is
in the Normal Mode of operation or Test Mode. In the
Normal Mode of operation, pre-determined governor
gains are used and the gain trimpots on the control
board (Gain, Stability, and Differential) are not active
and have no effect on the gains. In Test Mode the gain
trimpots are active and can be adjusted. See Section
3.4.
!
FOR STAND-B
TRANSFER S
ATTENTION:
ICE A
RISK OF ELE
PARTS
THIS E
N AUT
INJUR
LOW COOLANT LEVEL
HI COOLANT TEMPERATURE
FLASHING GREEN LED = NO UTILITY SENSE
5 FLASHING RED LED'S = EXERCISER NOT SET
(IN AUTO MODE ONLY) SOLID GREEN LED = SYSTEM READY, UTILITY POWER ON
(SEE OWNER'S MANUAL FOR COMPLETE DETAILS)
LED INDICATORS:
RED LED'S = INDIVIDUAL FAULT
OVER CRANK
SYSTEM READY
LOW BATTERY
LOW OIL PRESSURE
OVER SPEED
OFF
MANUAL
AUTO
START, RUN THROUGH THE EXERCISE
CYCLE AND SHUTDOWN.
TIME
SET
EXERCISE
TO AUTO POSITION.
SWITCH IN "ON" POSITION FOR
1) PLACE AUTO/OFF/MANUAL SWITCH
2) HOLD "SET EXERCISE TIME"
TO SET EXERCISER TIME
10 SECONDS. THEN THE UNIT WILL
THE EXERCISER IS NOW SET. ALL
FIVE RED LED'S WILL FLASH FOR
THREE SECONDS AND RELEASE.
ON
0F0653
OFF