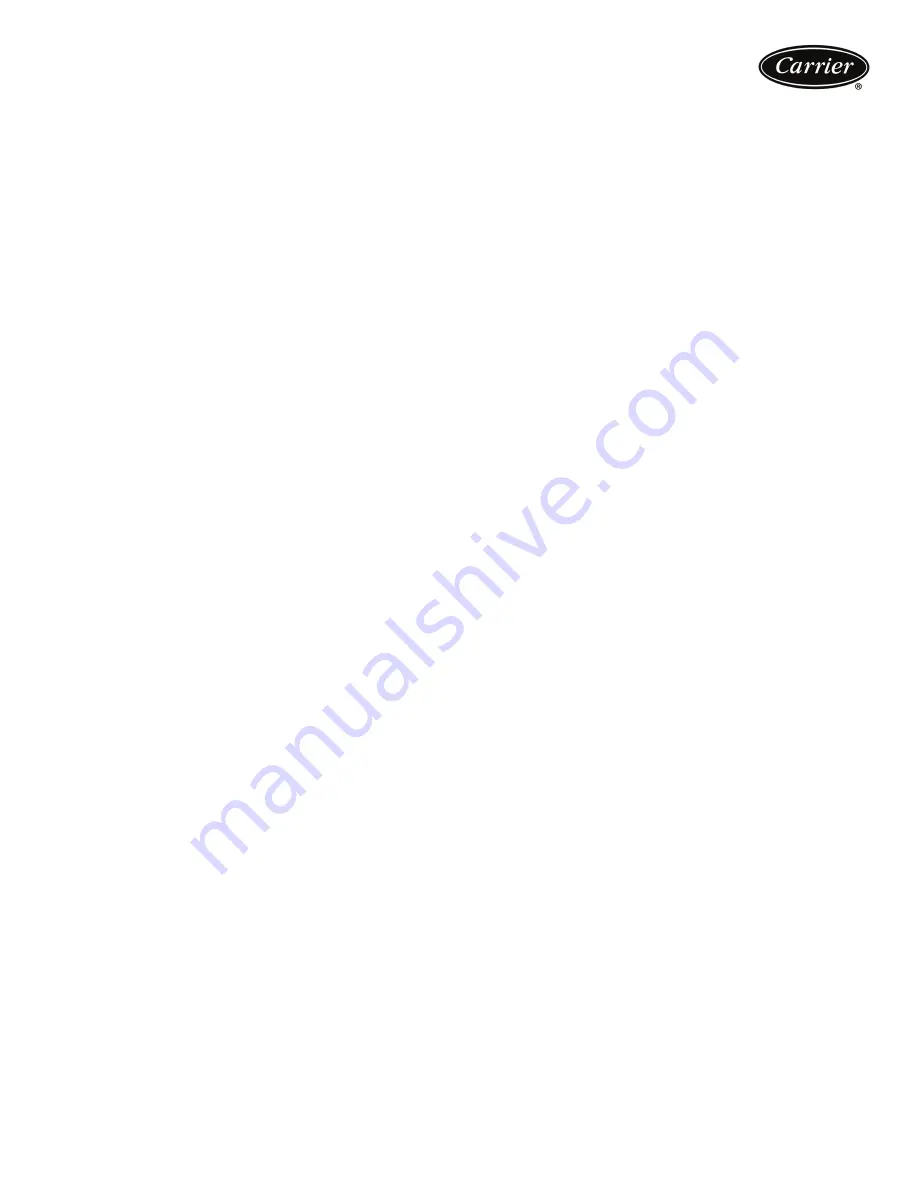
47
without material bridging between fins.
Coating process shall ensure complete coil
encapsulation. Color shall be high gloss
black with gloss — 60° of 65 to 90% per
ASTM ID523-89. Uniform dry film
thickness from 0.8 to 1.2 mil on all surface
areas including fin edges. Superior hardness
characteristics of 2H per ASTM D3363-
92A and cross hatch adhesion of 4B-5B per
ASTM D3359-93. Impact resistance shall be
up to 160 in./lb (ASTM D2794-93). Humid-
ity and water immersion resistance shall be
up to minimum 1000 and 250 hours respec-
tively (ASTM D2247-92 and ASTM D870-
92). Corrosion durability shall be confirmed
through testing to no less than 3000 hours
salt spray per ASTM B117-90. Coil con-
struction shall be aluminum fins mechani-
cally bonded to copper tubes.
d. E-coated copper-fin coils:
Shall have a flexible epoxy polymer coating
uniformly applied to all coil surface areas
without material bridging between fins.
Coating process shall ensure complete coil
encapsulation. Color shall be high gloss
black with gloss — 60° of 65 to 90% per
ASTM D523-89. Uniform dry film thickness
from 0.8 to 1.2 mil on all surface areas
including fin edges. Superior hardness char-
acteristics of 2H per ASTM D3363-92A
and cross hatch adhesion of 4B-5B per
ASTM D3359-93. Impact resistance shall be
up to 160 in./lb (ASTM D2794-93). Humid-
ity and water immersion resistance shall be
up to minimum 1000 and 250 hours respec-
tively (ASTM D2247-92 and ASTM D870-
92). Corrosion durability shall be confirmed
through testing to no less than 3000 hours
salt spray per ASTM B117-90. Coil con-
struction shall be copper-fins mechanically
bonded to copper tube sheets. Galvanized
steel tube sheets shall not be acceptable. A
polymer strip shall prevent coil assembly
from contacting sheet metal coil pan to
maintain coating integrity and minimize cor-
rosion potential between the coil and pan.
4. Liquid Line Solenoid Kit:
Unit shall be provided with a field-installed liquid
line solenoid (per refrigerant circuit) to be used
in low ambient and medium temperature brine
applications.
5. Wind Baffle Kit:
Field-installed accessory kit shall provide wind
baffles for use with low ambient operation.
6. Remote Enhanced Display:
Unit shall be supplied with indoor-mounted,
remote, 40-character per line, 16-line display
panel for field installation.
7. Medium Temperature Brine:
Unit shall be factory modified to start and oper-
ate at leaving chilled fluid temperatures between
15 F (–9 C) and 40 F (4.4 C).
8. Chillervisor System Manager III Multi-Unit
Control:
Field-installed control shall sequence between 2
and 8 chillers in parallel in a single system.
System shall control chilled water pumps.
9. Minimum Load Control:
Unit shall be equipped with factory (or field)
installed, microprocessor-controlled, minimum-
load control that shall permit unit operation
down to a minimum of 15% capacity (varies
with unit size).
10. Energy Management Module:
A factory or field-installed module shall provide
the following energy management capabilities:
4 to 20 mA signals for leaving fluid temperature
reset, cooling set point or demand limit control;
2-point demand limit control (from 15% to
100%) activated by a remote contact closure;
and discrete input for “Ice Done” indication for
ice storage system interface.
11. Security Grilles:
Unit shall be supplied with factory (or field)
installed painted grilles to protect the con-
denser, cooler, and compressor from physical
damage.
12. Hail Guards:
Field-installed accessory kit shall consist of hail
guards for the protection of the condensing
coils from hail damage.
13. Vibration Isolation:
Vibration isolation pads shall be supplied for
field installation at unit mounting points. Pads
shall help to reduce vibration transmission into
the occupied space.
14. Control Display Access Door:
Unit shall be provided with a transparent con-
trol box door that allows see-through viewing of
control display without opening the control
box.
15. Chilled Water Storage Tank:
a. Fluid storage tank shall be rated for a maxi-
mum of 150 psig (1034 kPa).
b. Shall provide a minimum 6 gallon per ton
(6.5 L per kW) fluid storage capacity.
c. Shall fit under the chiller to minimize system
footprint requirements. Tanks fitted out-
side of the chiller footprint shall not be
acceptable.
d. Tank shall be constructed a cold rolled car-
bon steel shell.