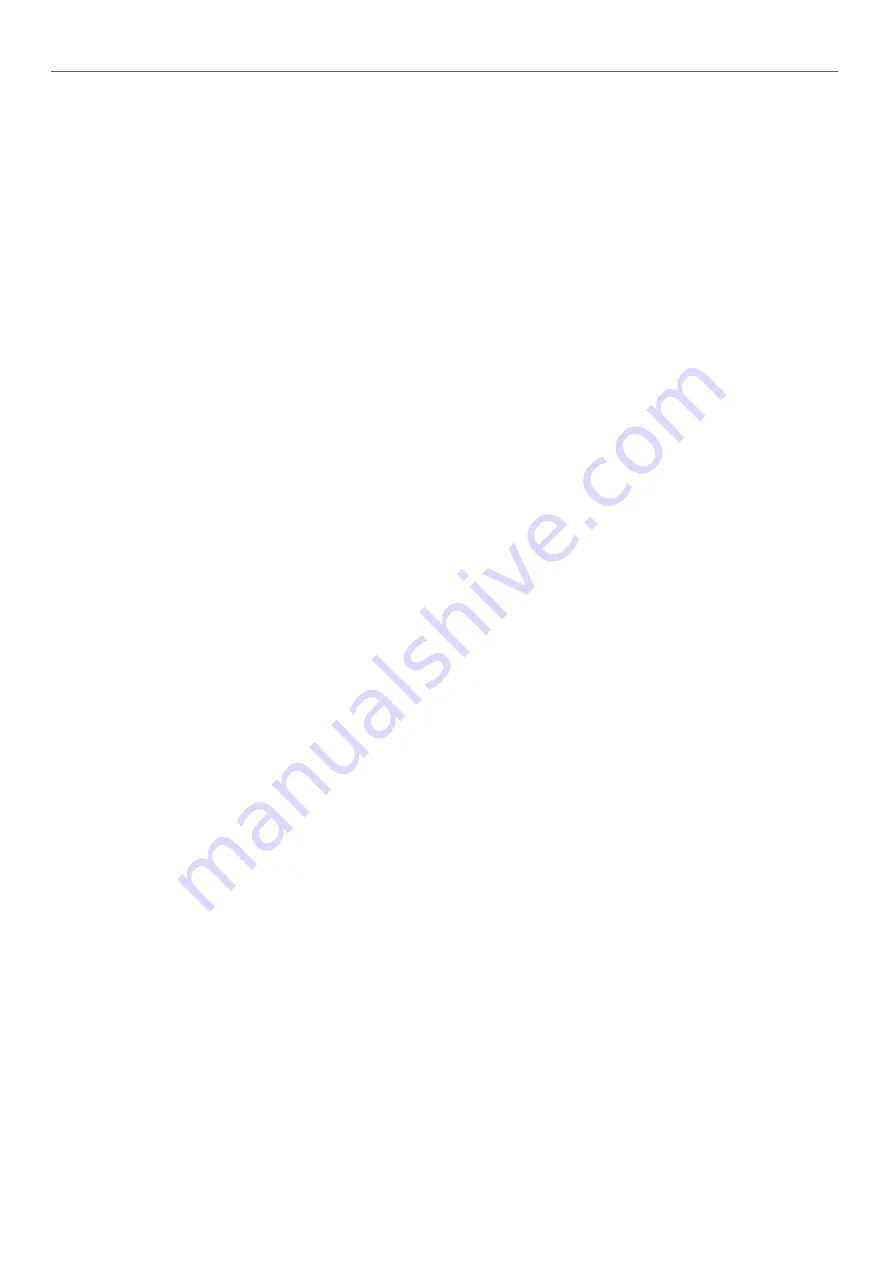
2 - PRELIMINARY CHECKS
2.1 - Check equipment received
■
Check that the unit has not been damaged during transport
and that no parts are missing. If the unit has been damaged or
the shipment is incomplete, send a claim to the shipping
company.
■
Compare the name plate data with the order. The name plate
is attached in two places to the unit:
-
On one of the unit sides on the outside
-
On the control box door on the inside.
■
The unit name plate must include the following information:
-
Model number - size
-
CE marking
-
Serial number
-
Year of manufacture and pressure and leak tightness test
date
-
Fluid being transported
-
Refrigerant used
-
Refrigerant charge per circuit
-
PS: Min./max. allowable pressure (high and low pressure
side)
-
TS: Min./max. allowable temperature (high and low pressure
side)
-
Pressure switch cut-out pressure
-
Unit leak test pressure
-
Voltage, frequency, number of phases
-
Maximum current drawn
-
Maximum power input
-
Unit net weight
■ Confirm that all accessories ordered for on-site installationhave
been delivered, are complete and undamaged.
■
- The unit must be checked periodically, if necessary removing
the insulation (thermal, acoustic), during its whole operating
life to ensure that no shocks (handling accessories, tools, etc.)
have damaged it. If necessary, the damaged parts must be
repaired or replaced. See also chapter “Maintenance”.
2.2 - Moving and siting the unit
2.2.1 - Moving
See chapter 1.2 - “Installation safety considerations”.
2.2.2 - Siting the unit
The machine must be installed in a place that is not accessible to
the public or protected against access by non-authorised persons.
In case of extra-high units the machine environment must permit
easy access for maintenance operations.
Always refer to the chapter “Dimensions and clearances” to confirm
that there is adequate space for all connections and service
operations. For the centre of gravity coordinates, the position of
the unit mounting holes, and the weight distribution points, refer
to the certified dimensional drawing supplied with the unit.
Typical applications of these units do not require earthquake
resistance. Earthquake resistance has not been verified and the
units are not explosion-proof.
ATTENTION : Ne pas élinguer ailleurs que sur les points
d'ancrage prévus et signalés sur l'unité.
-
Before siting the unit check that:
-
the permitted loading at the site is adequate or that
appropriate strenghtening measures have been taken.
-
if the heat pump is required to operate in temperatures below
0°C it must be raised at least 300 mm from the ground. This
is necessary to avoid ice build-up on the unit chassis and
also to permit correct unit operation in locations where the
snow level may reach this height.
-
the unit is installed level on an even surface (maximum
tolerance is 5 mm in both axes).
-
there is adequate space above the unit for air flow and to
ensure access to the components (see dimensional
drawings).
-
the number of support points is adequate and that they are
in the right places.
-
the location is not subject to flooding.
-
Baffles may be necessary to deflect strong winds. They must
not restrict air flow into the unit..
CAUTION: Before lifting the unit, check that all casing panels
are securely fixed in place. Lift and set down the unit with
great care. Tilting and jarring can damage the unit and impair
unit operation.
If 61AF units are hoisted with rigging, it is advisable to protect coils
against crushing while a unit is being moved. Use struts or a lifting
beam to spread the slings above the unit. Do not tilt a unit more than
15°.
WARNING: Never push or lever on any of the enclosure panels
of the unit. Only the base of the unit frame is designed to
withstand such stresses.
2.3 - Checks before system start-up
Before the start-up of the refrigeration system, the complete
installation, including the refrigeration system must be verified against
the installation drawings, dimensional drawings, system piping and
instrumentation diagrams and the wiring diagrams.
For these checks national regulations must be followed. If the national
regulation does not specify any details, refer to standard EN 378 as
follows:
External visual installation checks:
-
Ensure that the machine is charged with refrigerant, Verify
on the unit nameplate that the ‘fluid transported’ is R407C
and is not nitrogen.
-
Compare the complete installation with the refrigeration
system and power circuit diagrams.
-
Check that all components comply with the design
specifications.
-
Check that all protection documents and equipment provided
by the manufacturer (dimensional drawings, P&ID,
declarations etc.) to comply with the regulations are present.
-
Verify that the environmental safety and protection and
devices and arrangements provided by the manufacturer to
comply with the regulations are in place.
-
Verify that all documents for pressure containers, certificates,
name plates, files, instruction manuals provided by the
manufacturer to comply with the regulations are present.
-
Verify the free passage of access and safety routes.
-
Verify the instructions and directives to prevent the deliberate
removal of refrigerant gases.
-
Verify the installation of connections.
-
Verify the supports and fixing elements (materials, routing
and connection).
-
Verify the quality of welds and other joints.
-
Check the protection against mechanical damage.
-
Check the protection against heat.
-
Check the protection of moving parts.
-
Verify the accessibility for maintenance or repair and to check
the piping.
-
Verify the status of the valves.
-
Verify the quality of the thermal insulation and of the vapour
barriers.
-
Ensure that the ventilation in the machine room is sufficient.
-
Check the refrigerant detectors.
Summary of Contents for AquaSnap 61AF 022
Page 43: ......