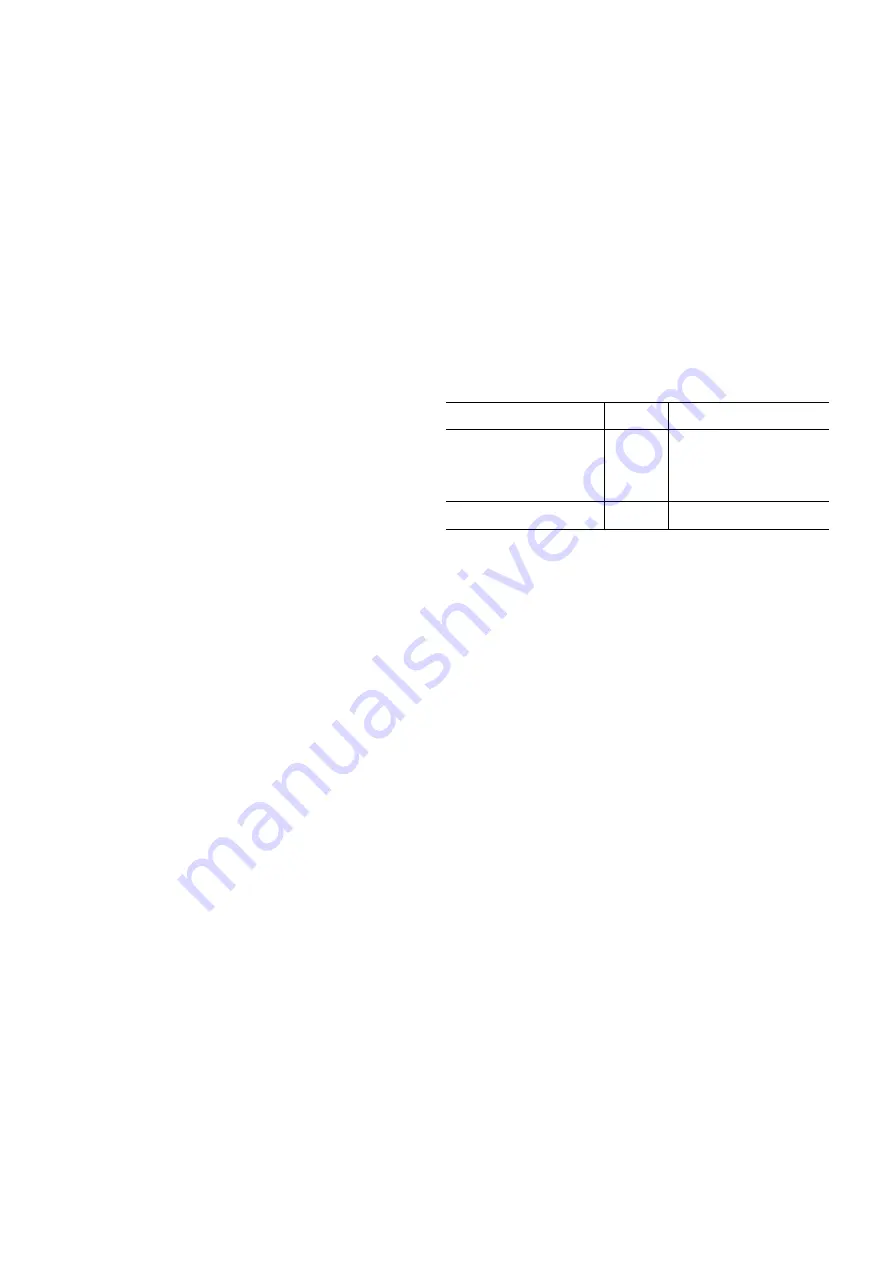
4
1 - INTRODUCTION
Prior to the initial start-up of the 30RW/30RWA units, the
people involved in the on-site installation, start-up, operation
and maintenance of this unit should be thoroughly familiar
with these instructions and the specific project data for the
installation site.
The 30RW/30RWA liquid chillers are designed to provide a
very high level of safety during installation, start-up, opera-
tion and maintenance. They will provide safe and reliable
service when operated within their application range.
This manual provides the necessary information to fami-
liarize yourself with the control system before performing
start-up procedures. The procedures in this manual are
arranged in the sequence required for machine installation,
start-up, operation and maintenance.
Be sure you understand and follow the procedures and
safety precautions contained in the instructions supplied
with the machine, as well as those listed in this guide.
To find out, if these products comply with European
directives (machine safety, low voltage, electromagnetic
compatibility, equipment under pressure etc.) check the
declarations of conformity for these products.
1.1 - Installation safety considerations
After the unit has been received, when it is ready to be
installed or reinstalled, and before it is started up, it must be
inspected for damage. Check that the refrigerant circuit(s)
is (are) intact, especially that no components or pipes have
shifted (e.g. following a shock). If in doubt, carry out a leak
tightness check and verify with the manufacturer that the
circuit integrity has not been impaired. If damage is detected
upon receipt, immediately file a claim with the shipping
company.
Do not remove the skid or the packaging until the unit is
in its final position. These units can be moved with a fork
lift truck, as long as the forks are positioned in the right
place and direction on the unit.
The units can also be lifted with slings, using only the
designated lifting points marked on the unit.
These units are not designed to be lifted from above. Use
slings with the correct capacity, and always follow the
lifting instructions on the certified drawings supplied with
the unit.
Safety is only guaranteed, if these instructions are carefully
followed. If this is not the case, there is a risk of material
deterioration and injuries to personnel.
DO NOT COVER ANY PROTECTION DEVICES.
This applies to fuse plugs and safety valves (if used) in the
refrigerant or heat transfer medium circuits. Check if the
original protection plugs are still present at the valve outlets.
These plugs are generally made of plastic and should not be
used. If they are still present, please remove them. Install
devices at the valve outlets or drain piping that prevent the
penetration of foreign bodies (dust, building debris, etc.) and
atmospheric agents (water can form rust or ice). These
devices, as well as the drain piping, must not impair
operation and not lead to a pressure drop that is higher
than 10% of the control pressure.
Classification and control
In accordance with the Pressure Equipment Directive and
national usage monitoring regulations in the European
Union the protection devices for these machines are
classified as follows:
Safety
accessory*
Damage limitation accessory**
in case of an external fire
Refrigerant side
High-pressure switch
x
External relief valve***
x
Rupture disk
x
Fuse plug
x
Heat transfer fluid side
External relief valve****
x
x
* Classified for protection in normal service situations.
** Classified for protection in abnormal service situations.
*** The instantaneous over-pressure limited to 10% of the operating pressure
does not apply to this abnormal service situation. The control pressure can be
higher than the service pressure. In this case either the design temperature or
the high-pressure switch ensures that the service pressure is not exceeded in
normal service situations.
**** The classification of these safety valves must be made by the personnel that
completes the whole hydronic installation.
Do not remove these valves and fuses, even if the fire risk
is under control for a particular installation. There is no
guarantee that the accessories are re-installed if the instal-
lation is changed or for transport with a gas charge.
All factory-installed safety valves are lead-sealed to
prevent any calibration change. If the safety valves are
installed on a reversing valve (change-over), this is
equipped with a safety valve on each of the two outlets.
Only one of the two safety valves is in operation, the other
one is isolated. Never leave the reversing valve in the
intermediate position, i.e. with both ways open (locate the
control element in the stop position). If a safety stop is
removed for checking or replacement please ensure that
there is always an active safety stop on each of the reversing
valves installed in the unit.
The external safety valves must always be connected to
drain pipes for units installed in a closed room. Refer to
the installation regulations, for example those of European
standard EN 378 and EN 13136.
These pipes must be installed in a way that ensures that
people and property are not exposed to refrigerant leaks.
As the fluids can be diffused in the air, ensure that the
outlet is far away from any building air intake, or that
they are discharged in a quantity that is appropriate for a
suitably absorbing environment.