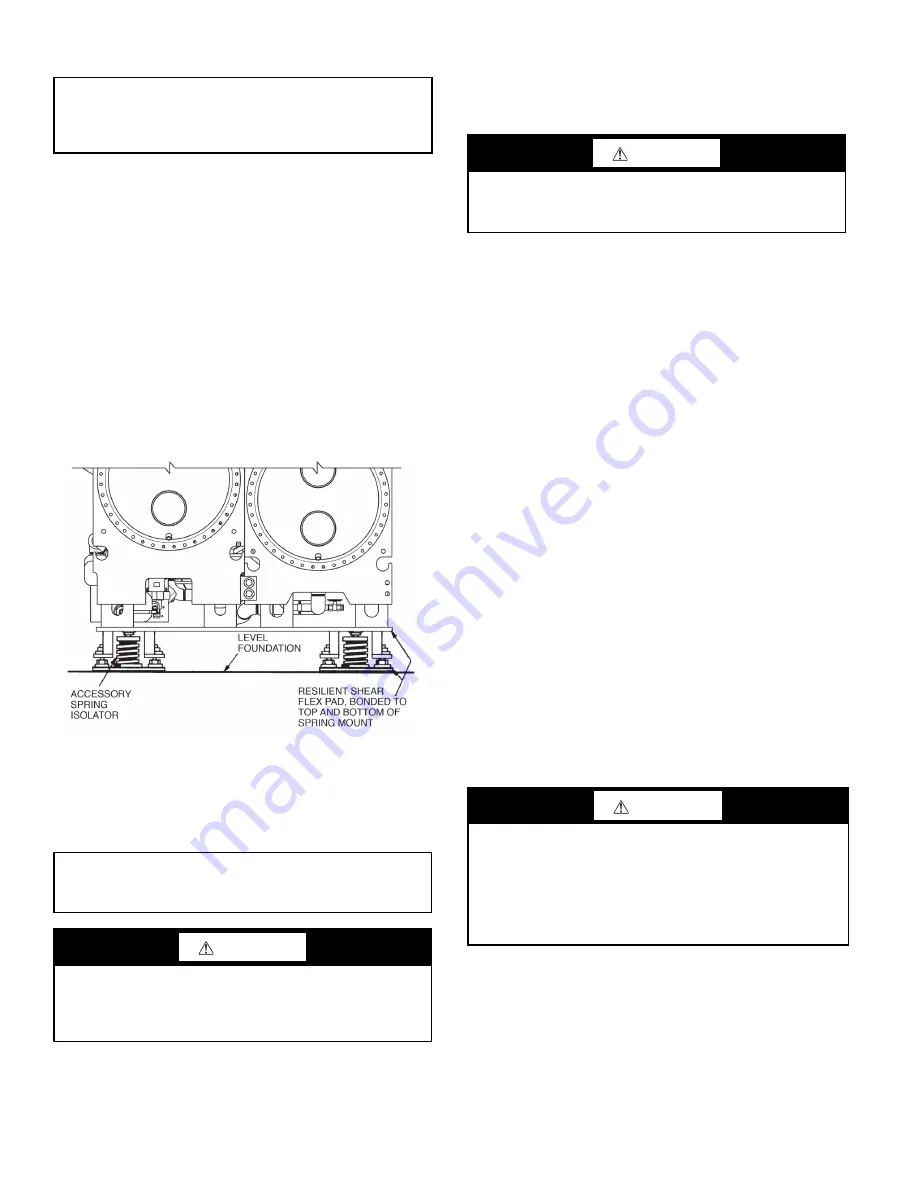
38
INSTALL SPRING ISOLATION
Spring isolation may be purchased as an accessory from Carrier
for field installation. It may also be field supplied and installed.
Spring isolators may be placed directly under machine support
plates or located under machine soleplates. See Fig. 45. Consult
job data for specific arrangement. Low profile spring isolation as-
semblies can be field supplied to keep the machine at a convenient
working height.
Obtain specific details on spring mounting and machine weight
distribution from job data. Also, check job data for methods to
support and isolate pipes that are attached to spring isolated
machines.
NOTE: These isolators are not intended for seismic duty, but are
intended to reduce the vibration and noise levels transmitted from
the chiller to the surrounding environment. For installations adja-
cent to areas that are sensitive to noise and/or vibration, use the
services of a qualified consulting engineer or acoustics expert to
determine whether these springs will provide adequate noise/
vibration suppression.
Fig. 45 — 23XRV Accessory Spring Isolation
(Shown with Accessory Soleplates)
Step 6 — Connect Piping
INSTALL WATER PIPING TO HEAT EXCHANGERS
Refer to Table 7 for nozzle sizes. Install piping using job data, pip-
ing drawings, and procedures outlined below. A typical piping in-
stallation is shown in Fig. 46.
1. Offset pipe flanges to permit removal of waterbox cover for
maintenance and to provide clearance for pipe cleaning. No
flanges are necessary with marine waterbox option; however,
water piping should not cross in front of the waterbox cover
or access will be blocked.
2. Provide openings in water piping for required pressure
gauges and thermometers. For thorough mixing and tempera-
ture stabilization, wells in the leaving water pipe should
extend inside pipe at least 2 in. (51 mm).
3. Install air vents at all high points in piping to remove air and
prevent water hammer.
4. Install pipe hangers where needed. Make sure no weight or
stress is placed on waterbox nozzles or flanges.
5. Water flow direction must be as specified in Fig. 47-49.
NOTE: Entering water is always the lower of the 2 noz-
zles. Leaving water is always the upper nozzle for cooler
or condenser.
6. Install waterbox vent and drain piping in accordance with
individual job data. All connections are 3/4-in. FPT.
7. Install waterbox drain plugs in the unused waterbox drains
and vent openings.
8. Install optional pumpout system or pumpout system and stor-
age tank as shown in Fig. 50-54.
9. Isolation valves are recommended on the cooler and con-
denser piping to each chiller for service.
10. Apply appropriate torque on the retaining bolts in a criss-
cross pattern for the waterbox covers before insulating the
waterbox cover. The gasket can relax during transportation
and storage, and the waterbox cover requires retightening of
the bolts.
IMPORTANT: Accessory spring isolation packages are intend-
ed solely for non-seismic applications. Seismic applications
must be designed by a registered professional in accordance
with all applicable national and local codes.
IMPORTANT: Chiller water nozzle connections to be designed
by others in accordance with all applicable national and local
codes.
CAUTION
Remove cooler and condenser liquid temperature and optional
pressure sensors before welding connecting piping to water
nozzles. Refer to Fig. 6-8. Replace sensors after welding is
complete.
NOTE: The accessory spring isolators are supplied by Carrier
for installation in the field.
a23-1537
CAUTION
Factory-supplied insulation is not flammable but can be dam-
aged by welding sparks and open flame. Protect insulation
with a wet canvas cover.
CAUTION
Never charge liquid R-134a refrigerant into the chiller if the
pressure is less than 35 psig (241 kPa). Charge as a gas only,
with the cooler and condenser pumps running, until 35 psig
(241 kPa) is reached using the pumpdown mode on the ICVC.
Terminate the pumpdown mode using the ICVC. Flashing of
liquid refrigerant at low pressures can cause tube freeze-up and
considerable damage.
Summary of Contents for AquaEdge 23XRV
Page 53: ...53 Fig 58 23XRV Controls Schematic ...
Page 54: ...54 Fig 58 23XRV Controls Schematic cont FROM 2000767952 SHEET 3 ...
Page 55: ...55 Fig 58 23XRV Controls Schematic cont ...
Page 56: ...56 Fig 59 23XRV Controls Schematic Rockwell Standard Tier VFD Shown ...
Page 57: ...57 Fig 60 23XRV LF2 VFD Wiring Diagram ...
Page 65: ...65 Fig 70 23XRV Insulation Area Units with P Compressor ...