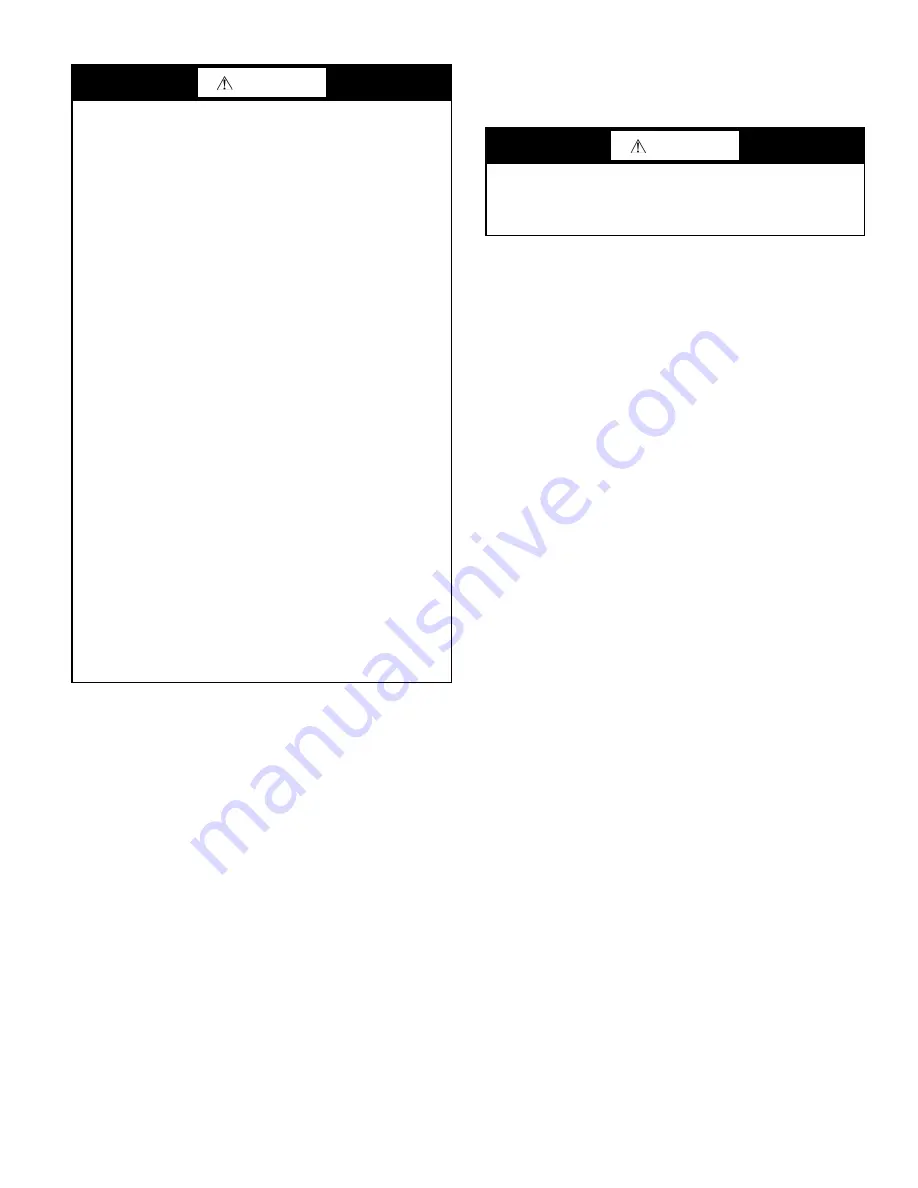
3
INTRODUCTION
The 23XRV machine is factory assembled, wired, and leak tested.
Installation (not by Carrier) consists primarily of establishing wa-
ter and electrical services to the machine. The rigging, installation,
field wiring, field piping, and insulation of waterbox covers are
the responsibility of the contractor and/or customer. Carrier has no
installation responsibilities for the equipment.
Job Data
Necessary information consists of:
• job contract or specifications
• machine location prints
• rigging information
• piping prints and details
• field wiring drawings
• starter manufacturer’s installation details
• Carrier certified print
INSTALLATION
Step 1 — Receive the Machine
INSPECT SHIPMENT
1. Inspect for shipping damage while machine is still on ship-
ping conveyance. If machine appears to be damaged or has
been torn loose from its anchorage, have it examined by
transportation inspectors before removal. Forward claim
papers directly to transportation company.
Manufacturer is
not responsible for any damage incurred in transit.
2. Check all items against shipping list. Immediately notify the
nearest Carrier representative if any item is missing.
3. To prevent loss or damage, leave all parts in original packages
until beginning installation. All openings are closed with cov-
ers or plugs to prevent dirt and debris from entering machine
components during shipping. A full operating oil charge is
placed in the oil sump before shipment.
IDENTIFY MACHINE (FIG. 1-8)
Refer to machine nameplate in Fig. 1. The machine model num-
ber, serial number, and heat exchanger sizes are stamped on the
Refrigeration Machine nameplate located on the side of the VFD
(variable frequency drive) enclosure. Check this information
against shipping papers and job data.
Identifying Drive by Part Number
The VFD drive can be identified by its part number (Fig. 9). This
number appears on the shipping label and on VFD nameplate.
Drive Input Component Location
Figure 10 identifies the control center components for the LiquiFlo
2.0 (LF-2) VFD. Figure 11 identifies the control center compo-
nents for the Std Tier VFD.
Identifying Power Module by ID Number
Each LF-2 AC power module can be identified by its ID number.
See Fig. 9. This number appears on the shipping label and on the
power module’s nameplate. Power ratings for LF-2 VFDs are pro-
vided in Table 1. Power ratings for Std Tier VFDs are provided in
Table 2.
INSTALLATION REQUIREMENTS
Certain installation requirements should be checked before con-
tinuing with the chiller’s electrical installation. Input power wire
sizes, branch circuit protection, and control wiring are all areas
that need to be evaluated.
Determining Wire Size Requirements
Wire size should be determined based on the size of the conduit
openings and applicable local, national, and international codes
(e.g., NEC [National Electric Code]/CEC [California Energy
Commission] regulations). General recommendations are includ-
ed in the Carrier field wiring drawing.
Conduit Entry Size
It is important to determine the size of the conduit openings in the
enclosure power entry plate so that the wire planned for a specific
entry point will fit through the opening. Do NOT punch holes or
drill into the top surface of the control center enclosure for field
wiring. Knockouts are provided in the back of the control center
for field control wiring connections.
CAUTION
BE AWARE that certain automatic start arrangements CAN
ENGAGE THE STARTER, TOWER FAN, OR PUMPS.
Open the disconnect ahead of the starter, tower fan, and
pumps. Shut off the machine or pump before servicing
equipment.
USE only repaired or replacement parts that meet the code
requirements of the original equipment.
DO NOT VENT OR DRAIN waterboxes containing industrial
brines, liquid, gases, or semisolids without the permission of
your process control group.
DO NOT LOOSEN waterbox cover bolts until the waterbox
has been completely drained.
DOUBLE-CHECK that coupling nut wrenches, dial
indicators, or other items have been removed before rotating
any shafts.
DO NOT LOOSEN a packing gland nut before checking that
the nut has a positive thread engagement.
PERIODICALLY INSPECT all valves, fittings, and piping for
corrosion, rust, leaks, or damage.
PROVIDE A DRAIN connection in the vent line near each
pressure relief device to prevent a build-up of condensate or
rain water.
DO NOT re-use compressor oil or any oil that has been
exposed to the atmosphere. Dispose of oil per local codes and
regulations.
DO NOT leave refrigerant system open to air any longer than
the actual time required to service the equipment. Seal circuits
being serviced and charge with dry nitrogen to prevent oil
contamination when timely repairs cannot be completed.
Chiller must be installed in an indoor environment where the
ambient temperature is between 40 to 104°F (4 to 40°C) with a
relative humidity (non-condensing) of 95% or less. To ensure
that electrical components operate properly and to avoid
equipment damage, do not locate chiller in an area exposed to
dust, dirt, corrosive fumes, or excessive heat and humidity.
CAUTION
Do not open any valves or loosen any connections. The
23XRV machine may be shipped with a full refrigerant charge.
Some machines may be shipped with a nitrogen holding
charge as an option.
Summary of Contents for AquaEdge 23XRV
Page 53: ...53 Fig 58 23XRV Controls Schematic ...
Page 54: ...54 Fig 58 23XRV Controls Schematic cont FROM 2000767952 SHEET 3 ...
Page 55: ...55 Fig 58 23XRV Controls Schematic cont ...
Page 56: ...56 Fig 59 23XRV Controls Schematic Rockwell Standard Tier VFD Shown ...
Page 57: ...57 Fig 60 23XRV LF2 VFD Wiring Diagram ...
Page 65: ...65 Fig 70 23XRV Insulation Area Units with P Compressor ...