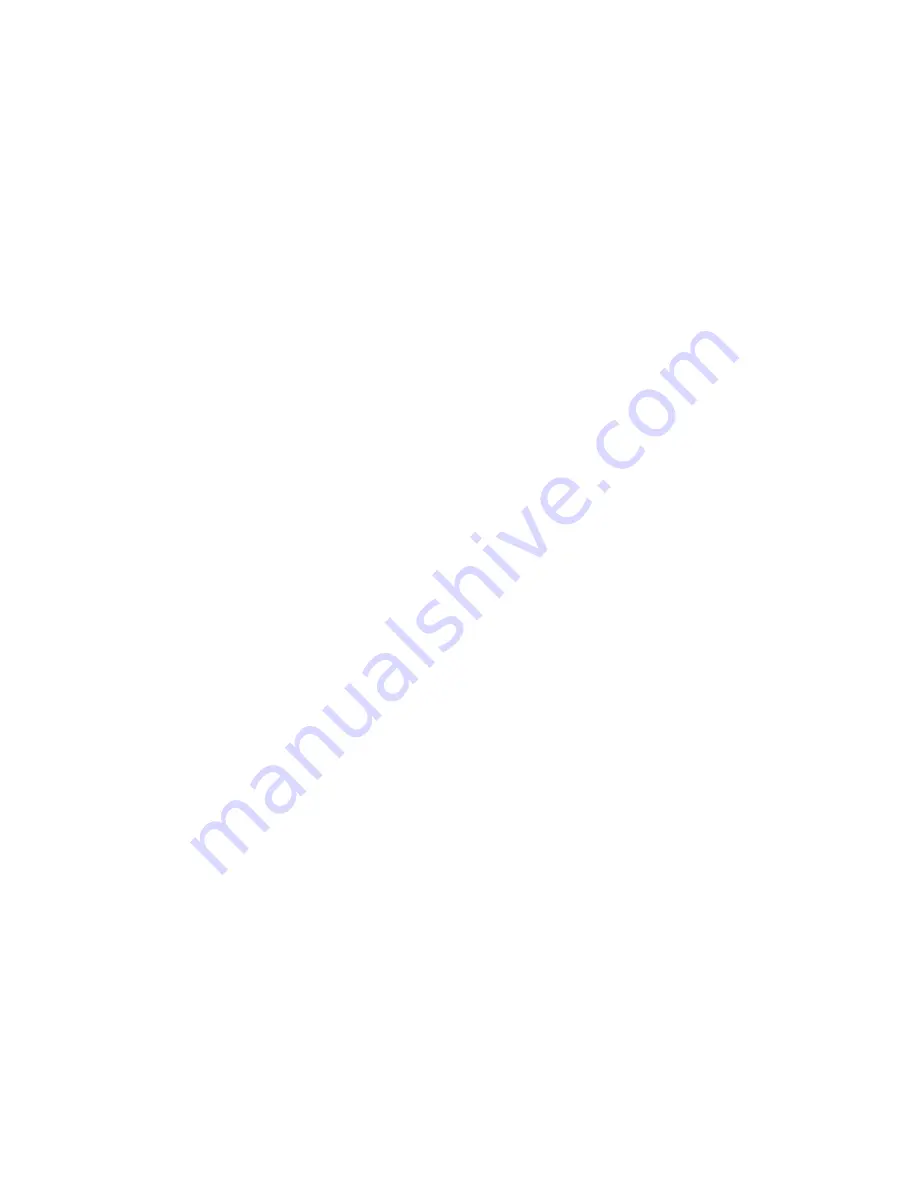
45
5.27 - Common point sensor usage and installation
Lead/lag operation does not require a common chilled water
point sensor. However, common point sensors (Spare Temp
#1 and #) may be added to the CCM module, if desired.
NOTE: If the common point sensor option is chosen on a
chilled water system, each chiller should have its own
common point sensor installed. Each chiller uses its own
common point sensor for control when that chiller is
designated as the lead chiller. The PIC III cannot read
the value of common point sensors installed on the other
chillers in the chilled water system.
If leaving chilled water control (
ECW CONTROL OPTION
is set to 0 [DSABLE] TEMP_CTL screen) and a common
point sensor is desired (
COMMON SENSOR OPTION
in
LEADLAG screen selected as 1) then the sensor is wired
in Spare Temp #1 position on the CCM (terminals J4-5
and J4-6).
If the entering chilled water control option (
ECW CON-
TROL OPTION
) is enabled (configured in TEMP_CTL
screen) and a common point sensor is desired (
COMMON
SENSOR OPTION
in LEADLAG screen selected as 1)
then the sensor is wired in Spare Temp # position on the
CCM (terminals J4-7 and J4-8).
When installing chillers in series, either a common point
sensor should be used (preferred), or the
LEAVING
CHILLED WATER
sensor of the upstream chiller must be
moved into the leaving chilled water pipe of the downstream
chiller. In this application the
COMMON SENSOR
OPTION
should only be enabled for the upstream chiller
if that chiller is configured as the Lead.
If
ENTERING CHILLED WATER
control is required on
chillers piped in series, either the common point return
chilled water sensor should be used (preferred), or the
LEAVING CHILLED WATER
sensor of the downstream
chiller must be relocated to the
LEAVING CHILLED
WATER
pipe of the upstream chiller. In this application, the
COMMON SENSOR OPTION
should only be enabled
for the downstream chiller if that chiller is configured as
the lead. Note that
ENTERING CHILLED WATER
control is not recommended for chillers installed in series
due to potential control stability problems.
To properly control the
LEAVING CHILLED WATER
TEMPERATURE
when chillers are piped in parallel, the
water flow through the shutdown chiller(s) should be isolated
so that no water bypass around the operating chiller occurs.
However, if water bypass around the operating chiller is
unavoidable, a common point sensor in the mixed
LEAV-
ING CHILLED WATER
piping should be provided and
enabled for the Lead chiller.
5.27.1 - Chiller communication wiring
Refer to the chiller’s Installation Instructions, Carrier
Comfort Network Interface section for information on
chiller communication wiring.
5.27.2 - Lead/lag operation
The PIC III not only has the ability to operate chillers in
lead/lag, but it can also start a designated standby chiller
when either the lead or lag chiller is faulted and capacity
requirements are not met. The lead/lag option only operates
when the chillers are in CCN mode. If any other chiller
configured for lead/lag is set to the LOCAL or OFF modes,
it will be unavailable for lead/lag operation.
Lead/lag chiller configuration and operation
•
A chiller is designated the lead chiller when its
LEAD-
LAG: CONFIGURATION
value on the LEADLAG
screen is set to “1.”
•
A chiller is designated the lag chiller when its
LEAD-
LAG: CONFIGURATION
value is set to “.”
•
A chiller is designated as a standby chiller when its
LEADLAG: CONFIGURATION
value is set to “3.”
•
A value of “0” disables the lead/lag designation of a
chiller. This setting should also be used when “normal”
operation without regard to lead/lag rules is desired
(in LOCAL or CCN mode).
When configuring the LAG ADDRESS value on the LEAD-
LAG screen of chiller “A” enter the address of the chiller
on the system which will serve as lag when/if chiller “A” is
configured as lead. For example, if you are configuring
chiller A, enter the address for chiller B as the lag address.
If you are configuring chiller B, enter the address for chiller
A as the lag address. This makes it easier to rotate the lead
and lag chillers. Note that only the lag and standby chiller
addresses specified in the configured lead chiller’s table
are relevant at a given time.
If the address assignments in the
LAG ADDRESS
and
STANDBY ADDRESS
parameters conflict, the lead/lag
function is disabled and an alert (!) message displays. For
example, if the
LAG ADDRESS
matches the lead chiller’s
address, the lead/lag will be disabled and an alert (!) message
displayed. The lead/lag maintenance screen (LL_MAINT)
displays the message ‘INVALID CONFIG’ in the
LEAD-
LAG: CONFIGURATION
and
CURRENT MODE
fields.
The lead chiller responds to normal start/stop controls such
as the occupancy schedule, a forced start or stop, and remote
start contact inputs. After completing start-up and ramp
loading, the PIC III evaluates the need for additional capa-
city. If additional capacity is needed, the PIC III initiates
the start-up of the chiller configured at the
LAG ADDRESS
.
If the lag chiller is faulted (in alarm) or is in the OFF or
LOCAL modes, the chiller at the
STANDBY ADDRESS
(if configured) is requested to start. After the second chiller
is started and is running, the lead chiller monitors conditions
and evaluates whether the capacity has been reduced enough
for the lead chiller to sustain the system alone. If the capa-
city is reduced enough for the lead chiller to sustain the
CONTROL POINT
temperatures alone, then the operating
lag chiller is stopped.
If the lead chiller is stopped in CCN mode for any reason
other than an alarm (*) condition, the lag and standby chillers
are also stopped. If the configured lead chiller stops for an
alarm condition, the configured lag chiller takes the lead
chiller’s place as the lead chiller, and the standby chiller
serves as the lag chiller.