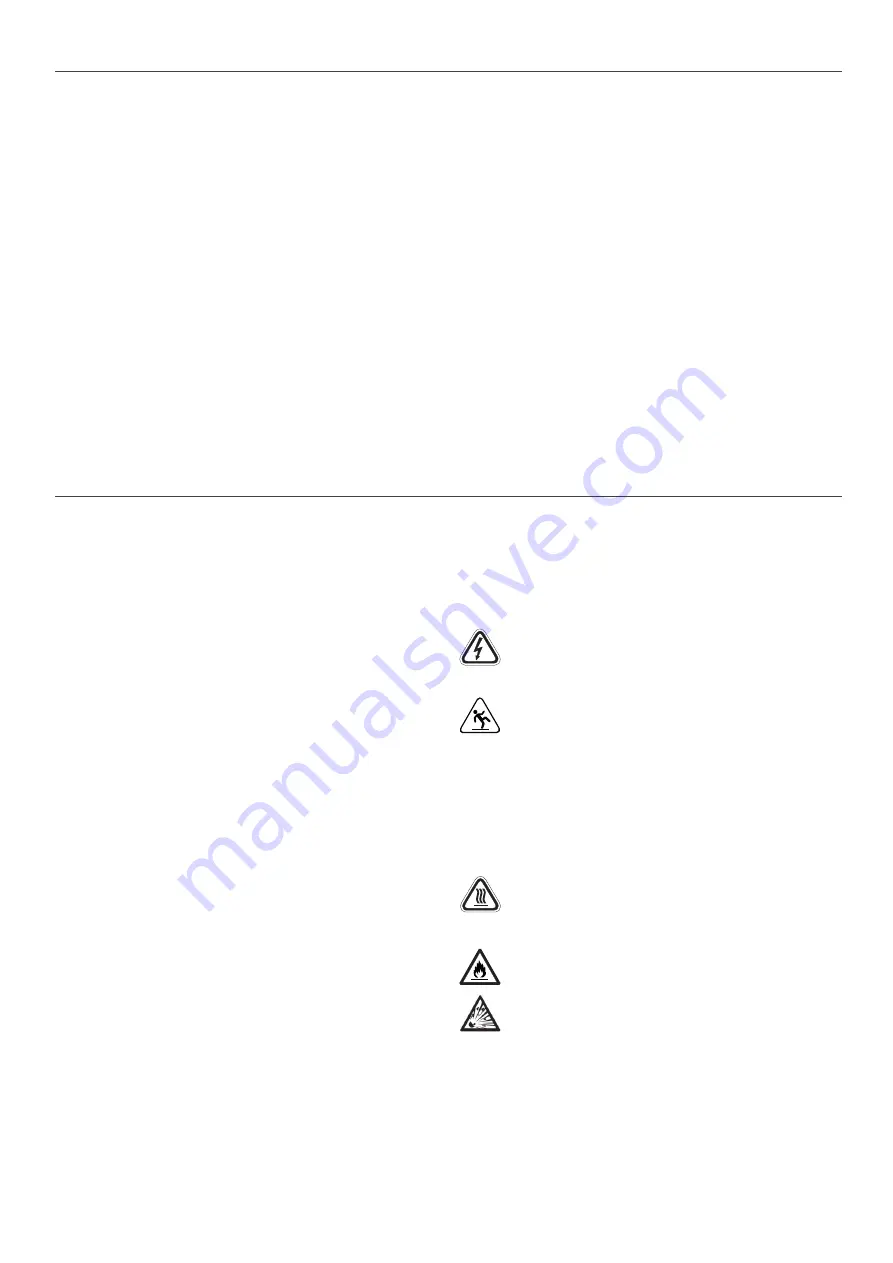
3
1 - INTRODUCTION
The
50FF/FC
packaged rooftop range consists of autonomous
compact air-air units of horizontal design, rooftop type.
■
50FF R-454B series:
Units for
cooling
operation.
■
50FC R-454B
and
R-410A series:
Units for
reversible heat
pump
operation.
These units are designed to be installed outdoors, in a free
fi
eld-
type, well ventilated area. It is user’s responsibility to ensure that
the
fi
nal installation respects all local, national and international
regulations.
The unit is connected directly to an air distribution ductwork without
additional elements or equipment, pipes, cables, etc. taking no
fl
oor space at all. This design reduces the cost of installation,
facilitates a quick connection and ensures reliable operation.
■
The units comply with European Directives:
- Machinery Directive 2006/42/EC (MD)
- Pressure Equipment Directive 2014/68/EU (PED):
• R-410A: Category 2
• R-454B: Category 3
- Electromagnetic Compatibility Directive 2014/30/EU (EMC)
- RoHS Directive 2011/65/EU (RoHS)
- Eco-design Directive 2009/125/EC (ECO-DESIGN)
- Energy Labelling Directive 2017/1369/EU (ECO-
LABELLING)
- Harmonised Standard: EN 378-2:2012 (Refrigerating systems
and heat pumps - Safety and environmental requirements).
After manufacturing, all units are charged with the selected
refrigerant: R-410A or R-454B, and are tested at the factory,
verifying the correct operation of all their components within
the operating range for which they are intended.
Note: These units are prepared for the replacement of R-410A
refrigerant by R454B on site. The necessary elements for this
change are supplied in a kit. All the instructions for carrying out
this retro
fi
t are explained in a separate document (No.10692).
Technicians who install, commission, operate and service the unit
must possess the necessary training and certi
fi
cations, understand
the instructions given in this manual and be familiar with the
speci
fi
c technical characteristics of the installation site.
2 - SAFETY ADVISE
2.1 - General safety advise
Units are designed to provide a very high level of safety during
installation, start-up, operation and maintenance.
They will provide safe and reliable service when operated within
their application range.
It is required to follow the recommendations and instructions
in this brochure, the labels, and the speci
fi
c instructions.
Compliance with the norms and regulations in e
ff
ect is mandatory.
It is recommended to consult the competent authorities regarding
the applicable regulations for users of units or components under
pressure. The characteristics of these units or components are
included on the plates of characteristics or in the regulatory
documentation provided with the product.
To avoid any risk of accident during installation, commissioning
or maintenance, it is obligatory to take into consideration the
following speci
fi
cations for the units: refrigerated circuits under
pressure, refrigerant presence, electrical voltage presence and
implantation place.
All operations on the unit must be carried out by authorized,
quali
fi
ed and trained people to do it using appropriate tools.
All refrigerant charging, removal and draining operations
must be carried out by a quali
fi
ed technician and with the
correct equipment for the unit. Any inappropriate handling
can lead to uncontrolled
fl
uid or pressure leaks.
All persons who have to work with the equipment must wear
personal protective equipment adapted to the intervention on
the unit:
■
Safety shoes.
■
Safety gloves or speci
fi
c hand protection (cut resistant gloves,
chemical gloves, thermic gloves, …).
■
Head protection.
■
Ears protection.
■
Eyes or face protection (safety glasses, goggles, facial shed).
■
A2L detector, in units with A2L gas (R-454B).
Additional equipment may be required, depending on the risk
analysis that must be done prior to any intervention.
The unit must be installed in a place that is not accessible
The compressor and line surfaces can reach temperatures
above 100ºC causing burns to the body. In the same
fashion, under certain conditions these surfaces can reach
very cold temperatures that can cause freezing risks.
Caution: Before intervening in the unit, verify that the
main power to the unit is cut o
ff
. An electric shock can
cause personal damage. The main disconnect switch is
located in the unit’s electrical cabinet.
No combustible matter should be placed within 6.5
metres of the unit.
Risk of explosion: Never exceed the speci
fi
ed maximum
operating pressures.
Verify the allowable maximum high-side and low-side test
pressures by checking the instructions in this manual and
the pressures given on the unit name plate.
to the public or protected against access by non-authorized
persons.
Do not modify or bypass any of the safety guards or switched
in the system.
Risk of falling: No part of the unit must be used as a
walk-way, rack or support. Use a platform, or staging to
work at higher levels.
It is mandatory to use all required PPE for work at height.
Pay special attention to units with lower supply and/or
return.
Periodically check and repair or if necessary replace any
component or piping that shows signs of damage. The
refrigerant lines can break under the weight and release
refrigerant, causing personal injury.
Important: These units are prepared to withstand a maximum
available pressure of 800 Pa. If there is a higher pressure,
deformation, breakage, etc., may occur.
In the case of an installation
fi
re test, the unit can be deformed
and/or broken. It is necessary to foresee this test and to take
appropriate measures.
Summary of Contents for 50FC Series
Page 63: ......