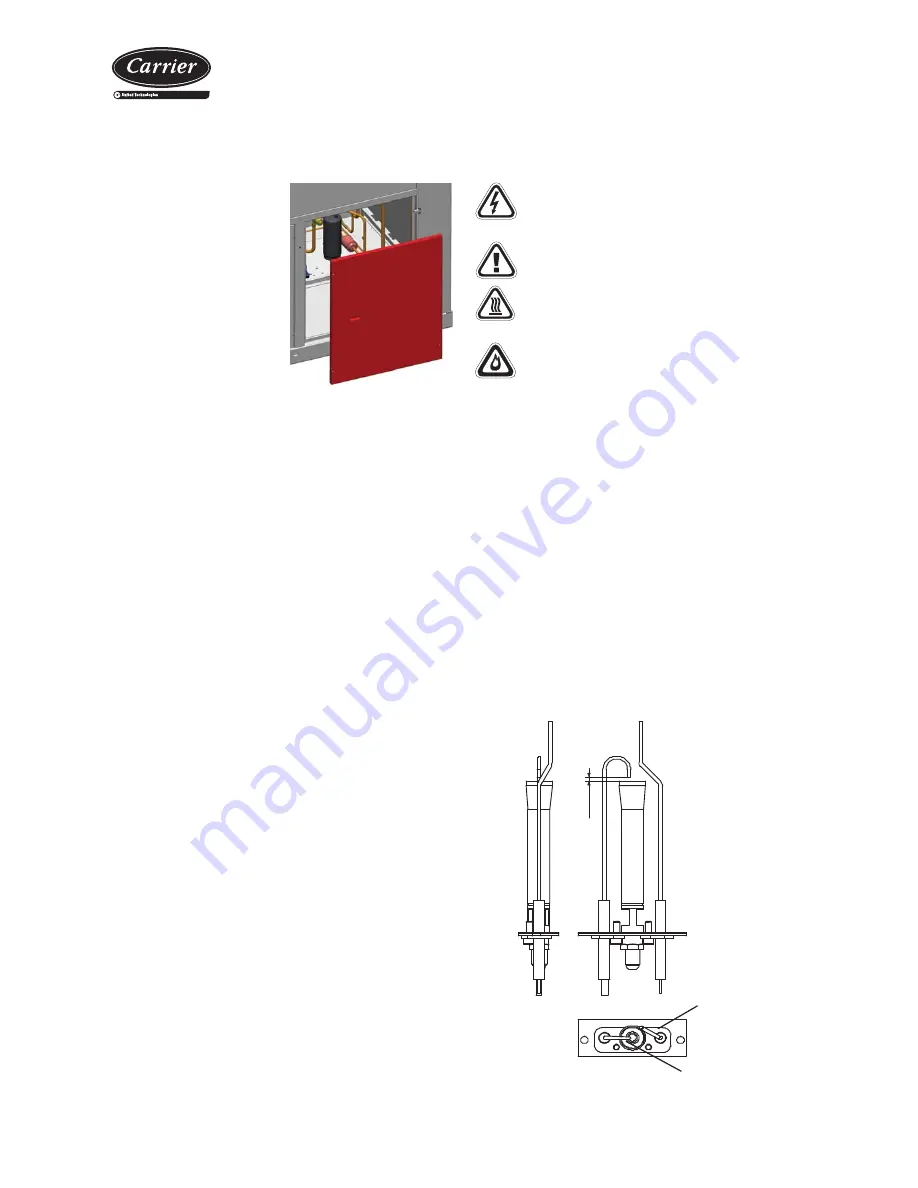
Packaged rooftop units
with integrated gas burner
20
Refrigerant
Qualifi ed personnel must perform a periodic control to air tightness
depending on the refrigerant load, in accordance with the regulation
(CE) Nº 842/2006.
It is important not to ever forget that the cooling systems contain
liquids and vapours under pressure. The service pressure of R-410A is
approximately 1.5 times higher than that of R-407c.
- All necessary precautions must be taken during the partial opening
of the cooling circuit. This opening entails the discharge of a certain
amount of refrigerant to the atmosphere. It is essential to limit to its
minimum this amount of lost refrigerant by pumping and isolating the
load in some other part of the circuit.
- The refrigerant fl uid at low temperature can cause infl ammatory
injuries similar to burns when contacting the skin or eyes. Always
use protection glasses, gloves, etc. when opening ducts that may
contain liquids.
- The refrigerant in excess must be stored in appropriate containers
and the amount of refrigerant stored at the technical rooms must be
limited.
- Refrigerant barrels and deposits must be handled with precaution
and visible warning signs must be placed to attract attention over
the risks of intoxication, fi re and explosion linked to the refrigerant.
- At the end of its useful life, the refrigerant must be retrieved and
recycled as per the current regulations.
Gas Burner
Oil
- Check the oil level and aspect. In case of a colour change, check
the oil quality using a contamination test.
- In the case of the presence of acid, water or metallic particles, replace
the affected circuit oil, as well as the dehydrant fi lter.
- In the event of an oil charge change, only new oil will be used, which
will be identical to the original oil and taken from a can tightly closed
until the moment of the charge.
Note:
Both the oil type as well as the volume needed for each model
are stated in the Technical characteristic tables in chapter 3.
Caution:
Before starting any maintenance operations
ensure that the supply of gas and electricity have been
turned off.
V-220004
Only qualifi ed staff are allowed to undertake maintenance
tasks or resolve a breakdown.
Pay attention to the temperatures of some components after
operation. They could be very high (exchanger, chimney,
etc).
Hazard:
Never use a naked fl ame whilst checking the burner.
Never store fl ammable material in the machine room.
1. The ignition, fl ame detector and the electrodes
Disassemble the set and clean the steel grille and the nozzle with a
blast of compressed air. Check that the ceramic is intact and remove
any oxide residue from the metal parts of the electrodes using emery
paper. Check the correct positioning of the electrodes (see diagram
below). Check that the detection electrode is positioned tangently
to the head of the burner, not inside it. The ignition electrode must
rest on the ignition pilot grille.
Check that the ignition
electrode is working between
the grille and the outer edge
2/3mm
Keep the detection
electrode tangent to
the ignition pilot head
The maintenance and checking of the combustion must be performed
in compliance with the legislation in force. Any modifi cation or change
in the material must be undertaken with the manufacturer's consent;
the replacement of a faulty component for another non-compliant
component could present a hazard for which CARRIER could not
accept liability.
These burners operate with minimum maintenance, however in order
to guarantee optimum performance when starting each warming stage
check:
Dehydrant fi lter
- The filter function is the
preserve the cooling circuit
clean and without humidity,
neutralizing the acids that can
be found in the cooling circuit.
Verify dirt by measuring the
difference in temperature at
the tubing level between the
inlet and the outlet of the
dehydrator.
- If necessary, replace.
Summary of Contents for 48EH
Page 23: ......