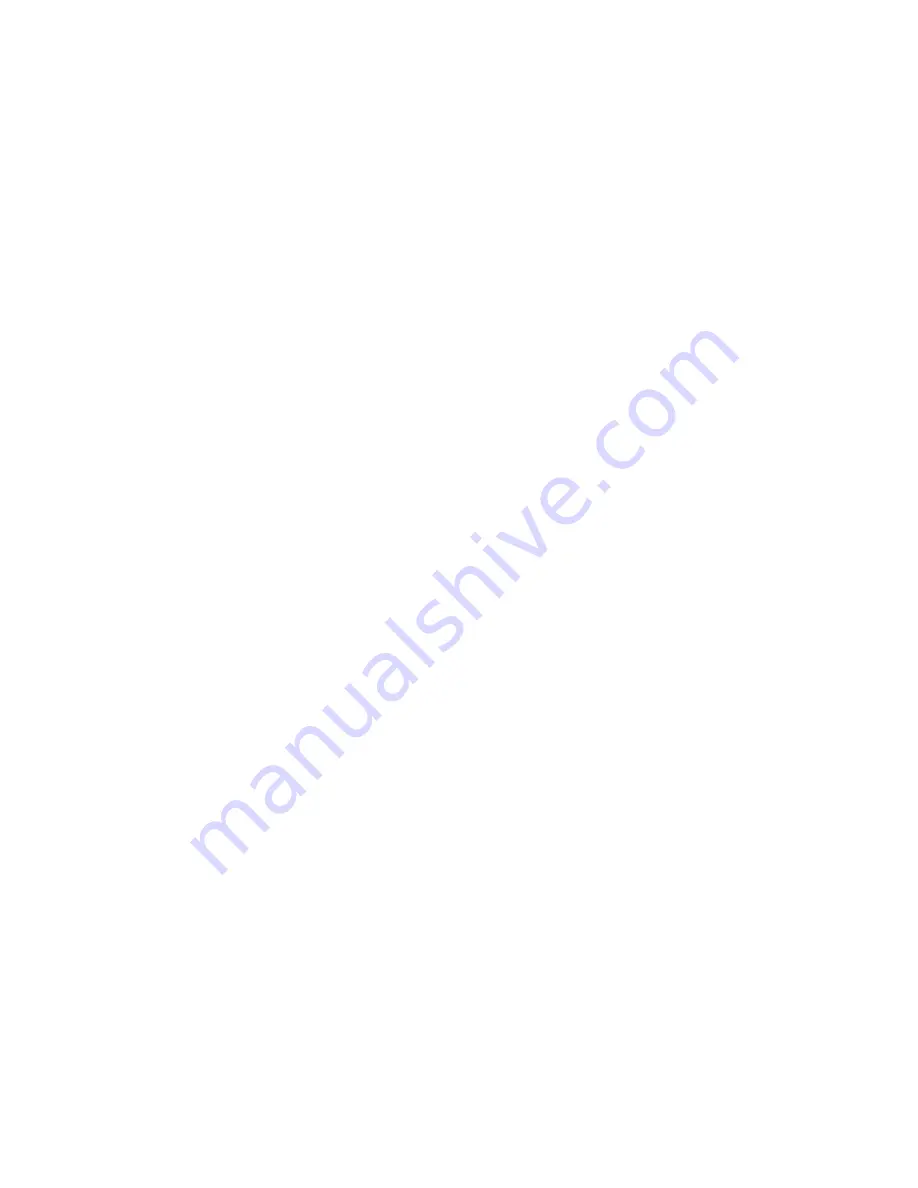
51
result in element overheating and possible limit switch
opening. This condition may result in the heater cycling on the
high-limit thermal cutout. Sheath heaters have automatic reset
switches only. Open strip heaters have an automatic reset
switch with a backup, high-limit thermal switch. Automatic
reset switch resets automatically after the heater has cooled
down. High limit thermal switch must be replaced once the
circuit has been broken. The high-limit thermal cutout device is
a safety device only and is not intended for continuous
operation. With proper unit application and operation, the high-
limit thermal cutout will not operate. This device only operates
when a problem exists, and ANY condition that causes high-
limit cutout MUST be corrected immediately. High supply
voltage also causes excessive amperage draw and may trip the
circuit breaker or blow the fuses on the incoming power
supply.
After proper airflow and supply power are assured, regular
filter maintenance is important to provide clean air over the
heater. Dirt that is allowed to deposit on the heating element
will cause hot spots and eventual element burn through. These
hot spots will normally not be enough to trip the high-limit
thermal cutout device and may not be evident until actual heat-
er element failure.
Filters —
The type of throwaway filter most commonly
used on fan coil units should be replaced on a regular basis.
The time interval between each replacement should be estab-
lished based on regular filter inspection and should be recorded
in the log for each unit. Refer to product catalog for recom-
mended filter size for each product type and size. If the replace-
ment filters are not purchased from the factory, the filter used
should be of same type and size as those furnished from or rec-
ommended by the factory. Pleated media or extended surface
filter should not be used since the high air pressure drop en-
countered with these type of filters is not compatible with the
type of fan coil unit covered in the manual.
A maintenance schedule for permanent filters should be de-
veloped in the same manner as throwaway filters. Unlike
throwaway filters, permanent filters may be cleaned and rein-
stalled in the unit instead of being discarded when dirty. The
optional factory permanent filter may be cleaned in hot soapy
water to remove any trapped dirt the set aside on edge to dry.
Before replacing the filter in the unit, it should be recharged
with some type of entrapment film. The filter should be
sprayed on both sides or submerged in the film to assure com-
plete coverage. The filter should not be allowed to soak in the
film but should be immediately removed and the excess film
drained from the filter before re-installation in the unit.
NOTE: Permanent filters normally have less static pressure
loss than throwaway filters.
Clean or Replace Air Filters —
Lock open and tag
unit electrical service switch.
At the start of each cooling season and after each month of
operation (more or less depending on operating conditions) re-
place throwaway filter or clean permanent filter.
THROWAWAY FILTER — The type of throwaway filter
most commonly used on fan coil units should be replaced on a
regular basis. The time interval between each replacement
should be established based on regular inspection of the filter
and should be recorded in the log for each unit. Replace filter
with a good quality filter of the size shown in Tables 1-4. Do
not attempt to clean and reuse disposable filters. If the replace-
ment filters are not purchased from the factory, the filters used
should be the same type and size as those furnished from or
recommended by the factory. Consult the factory for
applications using filter types other than the factory standard or
optional product. Filters with high arc pressure drops are gen-
erally not compatible with the fan coil units in this manual.
PERMANENT FILTER — A maintenance schedule for per-
manent filters should be developed in the same manner as
throwaway filters. Unlike throwaway filters, permanent filters
may be cleaned and re-installed in the unit instead of being dis-
carded when dirty.
1. Tap on solid surface to dislodge heavy particles.
2. Wash in hot water. If needed, use mild solution of com-
mercial solvent such as sal soda or trisodium phosphate.
3. Set filter on end so that water drains out through slots in
frame. Allow filter to dry thoroughly.
4. Recharge filter with recharging oil. Three ounces is suffi-
cient for medium size filter. Oil may be applied by insect
spray gun. For easier spraying, the oil can be warmed.
If the filter is dipped in the recharging oil, remove it im-
mediately and allow draining through slots in frame.
5. Replace filter in unit.
If another type of filter is used, follow the filter manufacturer's
instructions.
Electrical Wiring and Controls —
The electrical
operation of each unit is determined by the components and
wiring of the unit. This may vary from unit to unit. Consult the
wiring diagram attached to the unit for the actual type and
number of controls provided on each unit.
The integrity of all electrical connections should be verified
at least twice during the first year of operation. Afterwards, all
controls should be inspected regularly for proper operation.
Some components may experience erratic operation or failure
due to age. Wall thermostats may also become clogged with
dust and lint and should be periodically inspected and cleaned
to provide reliable operation.
When replacing any components such as fuses, contractors,
or relays, use only the exact type, size and voltage component
as furnished from the factory. Any deviation without factory
authorization could result in personal injury or damage to the
unit. This will also void all factory warranties. Only factory-
supplied replacement parts ensure that the warranty and agency
status remain in effect. All repair work should be done in such
a manner as to maintain the equipment in compliance with
governing codes, ordinances and testing agency listings.
More specific information regarding the use and operating
characteristics of the standard controls offered by the
manufacturer are contained in other manuals.
Valves and Piping —
No formal maintenance is re-
quired on the valve-package components most commonly used
with fan coil units other than a visual inspection for possible
leaks in the course of other normal periodic maintenance. In the
event that a valve should need replacement, the same
precautions taken during the initial installation to protect the
valve package from excessive heat should also be used during
replacement.
Warranty —
All equipment and components sold through
the Parts Department are warranted under the same conditions
as the standard manufacturer’s warranty with the exception
that the warranty period is thirty (30) days unless the compo-
nent is furnished as a warranty replacement. Parts furnished as
warranty replacements are warranted for the remaining term of
the original unit warranty or not less than thirty (30) days.