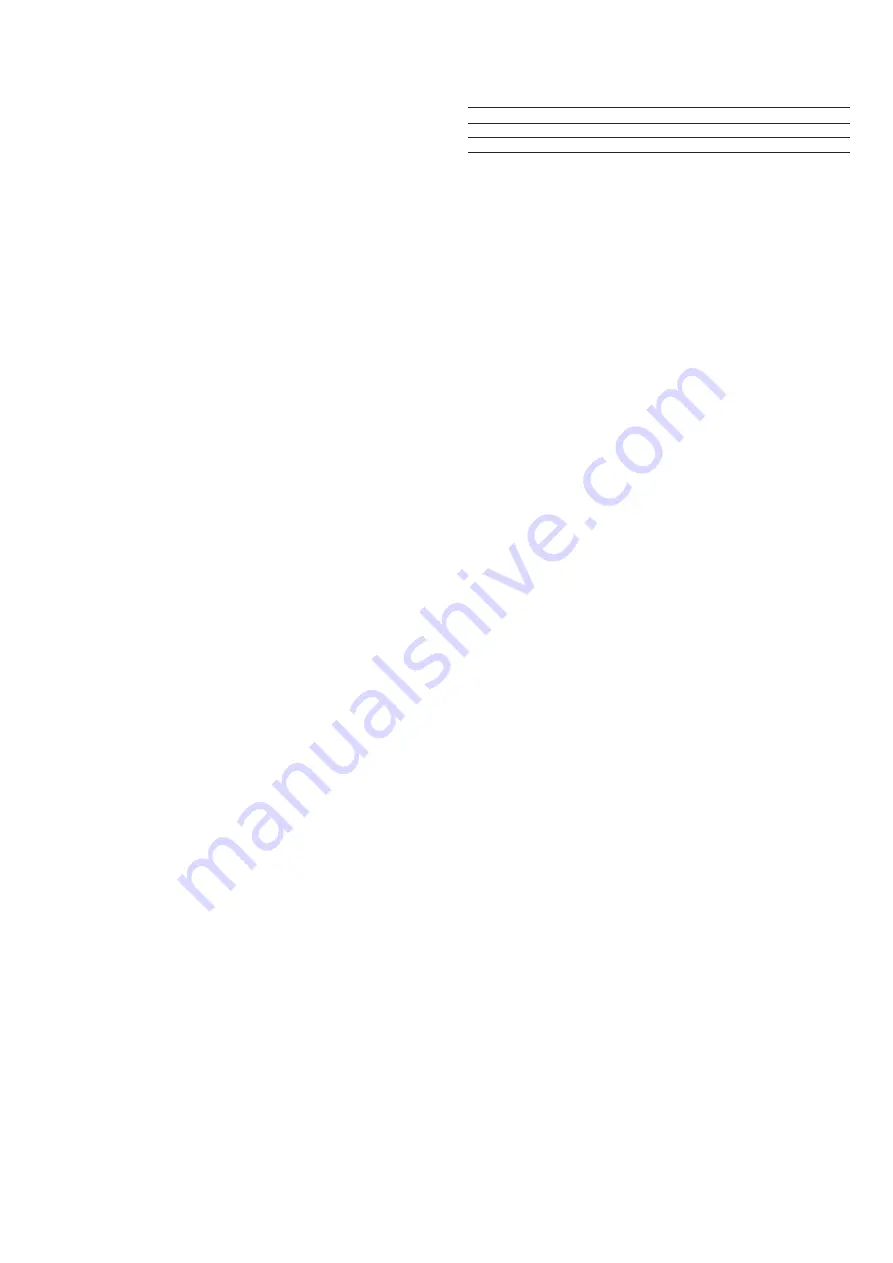
9
3 - saFety consIderatIons
3.1 - General
Installing, commissioning and servicing of the various com-
ponents which make up the different control loops can be
dangerous unless certain aspects of the installation, such as
the presence of mains electricity and hot or chilled-water
in the air conditioning equipment, are taken into account.
Only specially trained and qualified technicians and
installers who have been fully trained on the product con-
cerned are authorised to install, commission and service
this equipment.
During servicing work, it is essential to apply all recommen-
dations and instructions given in service leaflets, on labels
or in the instructions delivered with the equipment, and to
comply with any other relevant instructions.
Comply with all the safety rules and regulations currently
in force.
Wear eye protectors and work gloves.
Take care when moving or positioning equipment.
3.2 - Precautions against electrocution
Only electricians who are qualified to the level recom-
mended by the IEC (International Electrotechnical
Commission) in its standard IEC 364, corresponding to
Europe HD 384, France NFC 15 100 and UK IEE Wiring
Regulations, may have access to electrical components. In
particular it is obligatory to disconnect all electrical power
supplies to the unit and its accessories before carrying out
any work. Disconnect the main power supply with an
isolating device (not supplied by Carrier).
IMPORTANT: The components, which make up the
different control loops described in this manual include
electronic items. As such, they may generate or be harmed
by electromagnetic interference unless they are installed
and used in accordance with these instructions. The
components making up these control systems conform to
the requirements of electromagnetic compatibility in
residential and industrial areas. They also comply with
the low-voltage directive.
3.3 - General installation recommendations
IMPORTANT: The Carrier numeric controller, power
module, or in general units fitted with controls loops must
have an isolating device upstream (for example a double-
pole circuit breaker). If necessary, an easily operated
emergency stop device (such as a punch-button switch) must
cut off the power to all equipment. These safety devices
shall be sized and installed in accordance with IEC
Recommendation 364, corresponding to Europe HD 384,
France NFC 15 100 and UK IEE Wiring Regulations.
These devices are not supplied by Carrier.
In general terms the following rules must be applied:
•
Units must be provided with over-voltage protection
upstream (not supplied by Carrier)
upstream over-voltage protection
Unit without electric heater
T2A
Unit with electric heater
T16A
•
Units must be protected by a differential type earth
leakage current device (not supplied by Carrier).
•
The power disconnexion device must be clearly labelled
to identify which items of equipment are connected to
it.
•
The wiring of the components which make up the
different control systems and the communication buses
must be carried out in accordance with the latest rules
and regulations by professional installers.
•
The power supply cable must be doubly insulated and
fixed using a cable clamp. A hole is provided for this
purpose in the plastic Carrier controller housing. The
cable must be clamped on the outer insulation.
•
The control loop components must be installed in an
environment, which conforms to their index of protec-
tion (IP).
The maximum level of pollution is normally pollutant
(level ) and installation category II.
•
The low-voltage wiring (communication bus) must be
kept physically separate from the power wiring.
•
In order to avoid interference with the communication
links:
-
Keep low-voltage wiring away from power cables
and avoid using the same cable run (a maximum of
300 mm in common with the 30 VAC, 30 A cable)
-
Do not pass low-voltage wires through loops in
the power cables
-
Do not connect heavy inductive loads to the same
electrical supply (circuit breaker) used by the
controllers, power modules or speed controllers.
-
Use the screened cable type recommended by
Carrier and make sure all cables are connected to
the controllers and power modules.
3.4 - conformity
This equipment has been declared to be in conformity with
the main requirements of the directive by virtue of using
the following standards:
•
Electromagnetic compatibility: 89/336/EEC,
•
Low-voltage directive: 73/3/EEC.