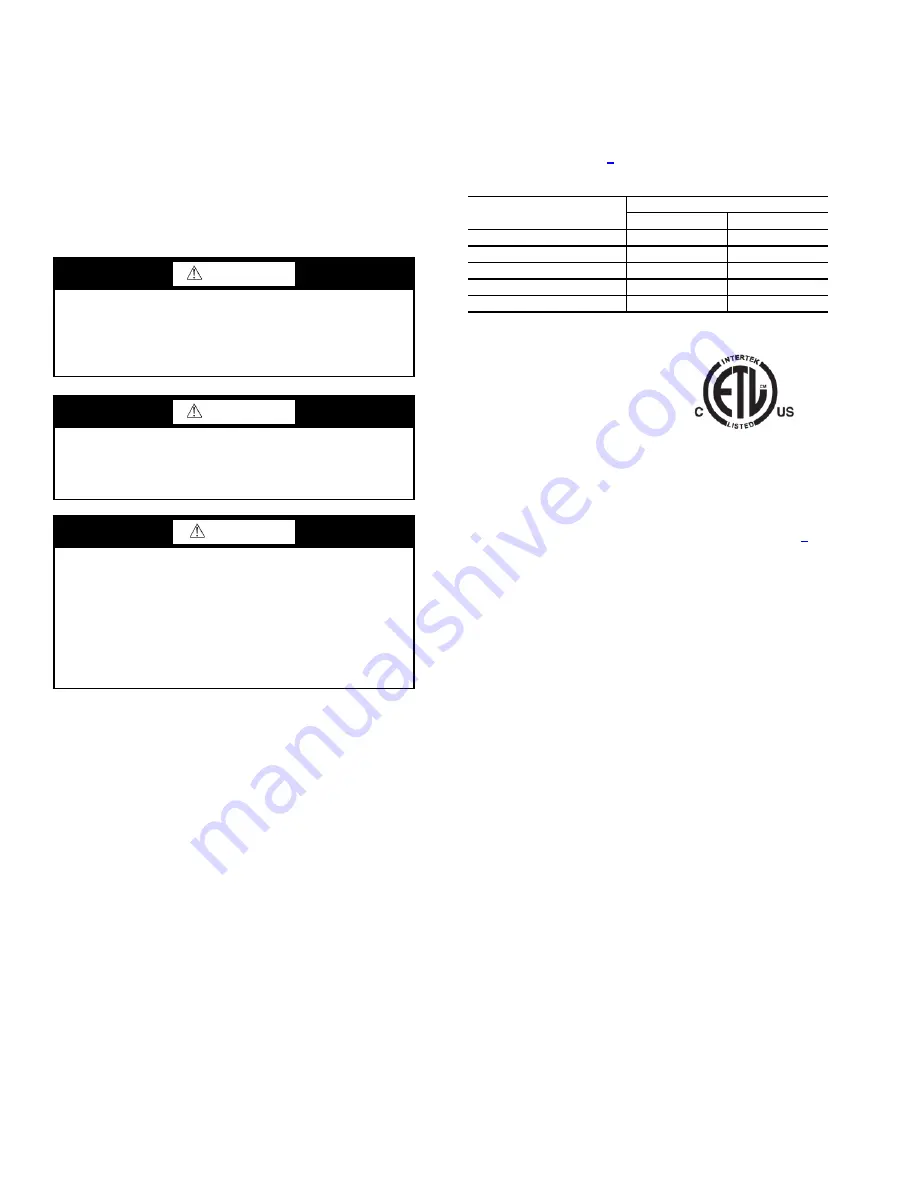
6
• Before insulating the suction and liquid refrigeration
pipes, perform pressure and leak tests. For details, see
the outdoor unit installation manual. Insulating both suc-
tion and liquid refrigerant pipes is required.
• Vacuuming and charging of the system should be carried
out as described in the outdoor unit installation manual.
Step 5 — Complete Electrical Connections —
Installation of wiring must conform with local building codes,
or in the absence of local codes, with the National Electric
Code ANSI/NFPA 70, current editions. Units must be electri-
cally grounded in conformance with the code. In Canada, wir-
ing must comply with CSA C22.1, Electrical Code.
This equipment in its standard form is designed for an elec-
trical supply of 208/230-1-60. Any damage to or failure of
units caused by incorrect wiring or voltage is not covered by
warranty.
Electric wiring must be sized to carry the full load amp
draw of the motor, starter, and any other controls that are used
with the unit. See Table 2 for electrical data.
Table 2 — 40WAV Electrical Data
LEGEND
After the pipe work is complete, the electrical supply can be
connected by routing the cable through the appropriate casing
holes or knockouts and connecting the supply and ground
cables to the unit’s power terminal.
Be sure the power wiring and control wiring do not cross, as
this might cause disturbance on the controls side. See Fig. 5 for
wiring diagram.
NOTE: The indoor unit requires its own power supply. Indoor
units are not powered from outdoor units.
WARNING
Electrical shock can cause personal injury and death. Dis-
connect power supply before making wiring connections.
There may be more than one disconnect switch. Tag all dis-
connect locations to alert others not to restore power until
work is completed.
WARNING
All units must be wired strictly in accordance with the wir-
ing diagram furnished with the unit. Any wiring different
from the wiring diagram could result in personal injury and
property damage.
CAUTION
Any original factory wiring that requires replacement must
be replaced with wiring material having a temperature rat-
ing of at least 221 F (105 C).
Ensure supply voltage to the unit, as indicated on the serial
plate, is not more than 10% over the rated voltage or 10%
under the rated voltage.
Failure to follow these recommendations may result in
equipment damage.
40WAF UNIT SIZE
POWER SUPPLY
MCA
MOPD
018
3.8
15
024
3.8
15
030
3.8
15
036
5.3
15
048
5.3
15
MCA
— Minimum Circuit Amps
MOPD — Maximum Overcurrent
Protective Device