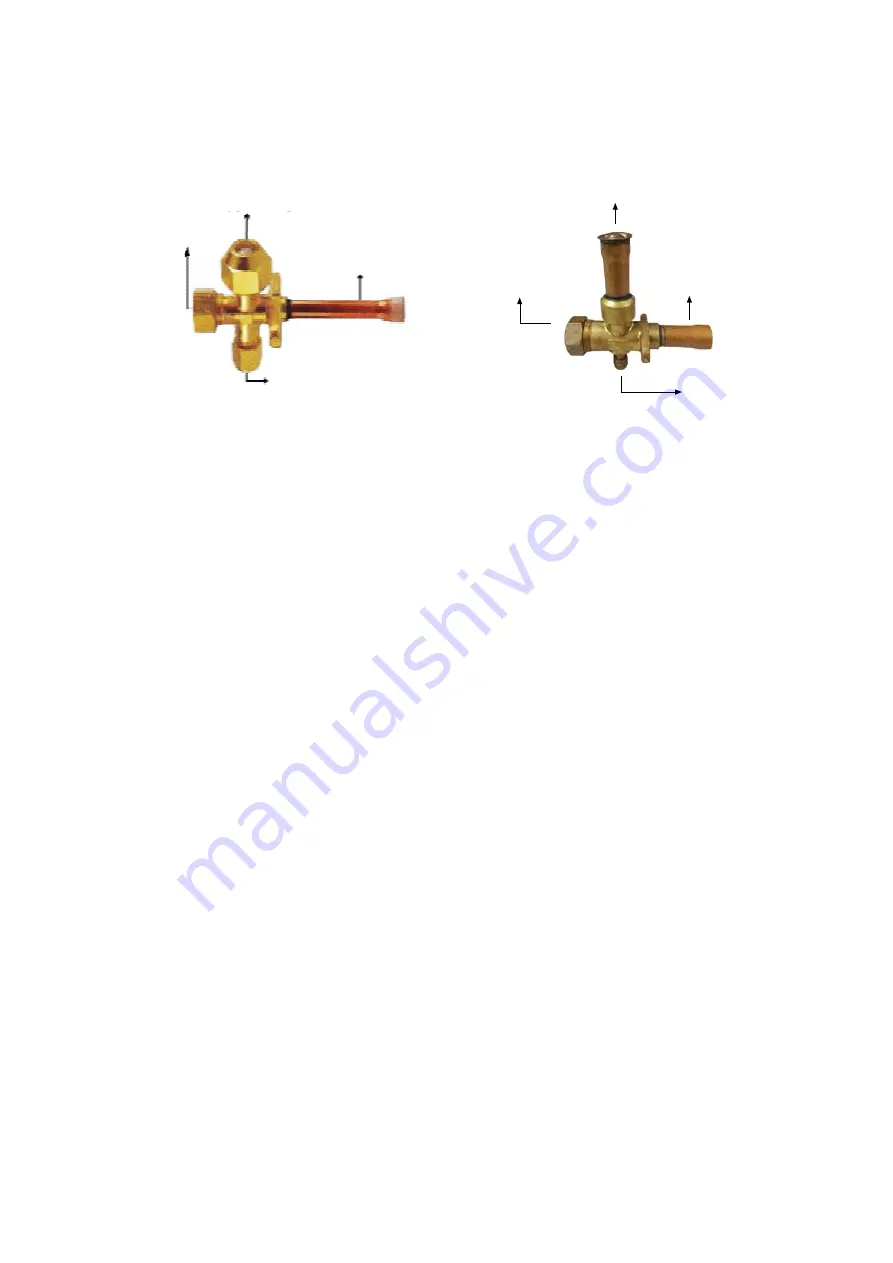
Piping Connections / Piping
Refer to Physical Data Table for correct piping sizes. The length of refrigerant pipe depends on the unit
placement and building structure – attempt to run pipes as
1. Refrigerant tubing between sections may be made using accessory tubing packages or field-supplied
tubing of refrigerant grade, correct size and condition.
2. Refrigerant suction tube must be insulated with closed-cell foam type insulation with a minimum wall
thickness of 3/8 in. Failure to properly insulate refrigerant tubes adequately will degrade system
performance and efficiency as well as permitting moisture or frost to form on the tubing surfaces during
operation.
3. Run refrigerant tubes as directly as possible, avoiding unnecessary turns and bends.
4. If tube bending is necessary, use only copper cutter to cut the copper tube and shape tube with a tube
bender so that the tube ends coincide with flare connections.
5. Carefully remove the flare nut fitting from indoor and outdoor sections tubing.
6. Thoroughly clean all tubing connection points to prevent foreign matter from entering the refrigerant
circuit.
7. Thread the 2 fittings by hand, making sure the threads fit smoothly and the flare seats evenly against the
union.
8. Tighten the 2 fittings securely.
9. Connect piping to the indoor and outdoor section.
10. Evacuate the system at lower 500-micron for at least 30 minutes.
11. Suspend refrigerant tubes so they do not damage insulation on liquid and vapor tubes and do not
transmit vibration to structure. Also, when passing refrigerant tubes through walls, seal opening so
vibration is not transmitted to structure. Leave some slack in refrigerant tubes between structure and units
to absorb vibration.
12. After evacuating the system, turn on both valves at the condensing unit to flow the refrigerant into the
system. Outdoor unit contains holding refrigerant charge to operate split system.
- 6 -
Service Valve (Blazing)
Service Valve (Flare)
CONNECTION TO
INDOOR PIPING (Brazing)
SERVICE PORT
(SCHRAEDER)
FACTORY-BRAZED
TO CONDENSING UNIT
SHUT-OFF PORT
CONNECTION TO
INDOOR PIPING (Flare)
FACTORY-BRAZED
TO CONDENSING UNIT
SERVICE PORT
(SCHRAEDER)
SHUT-OFF PORT