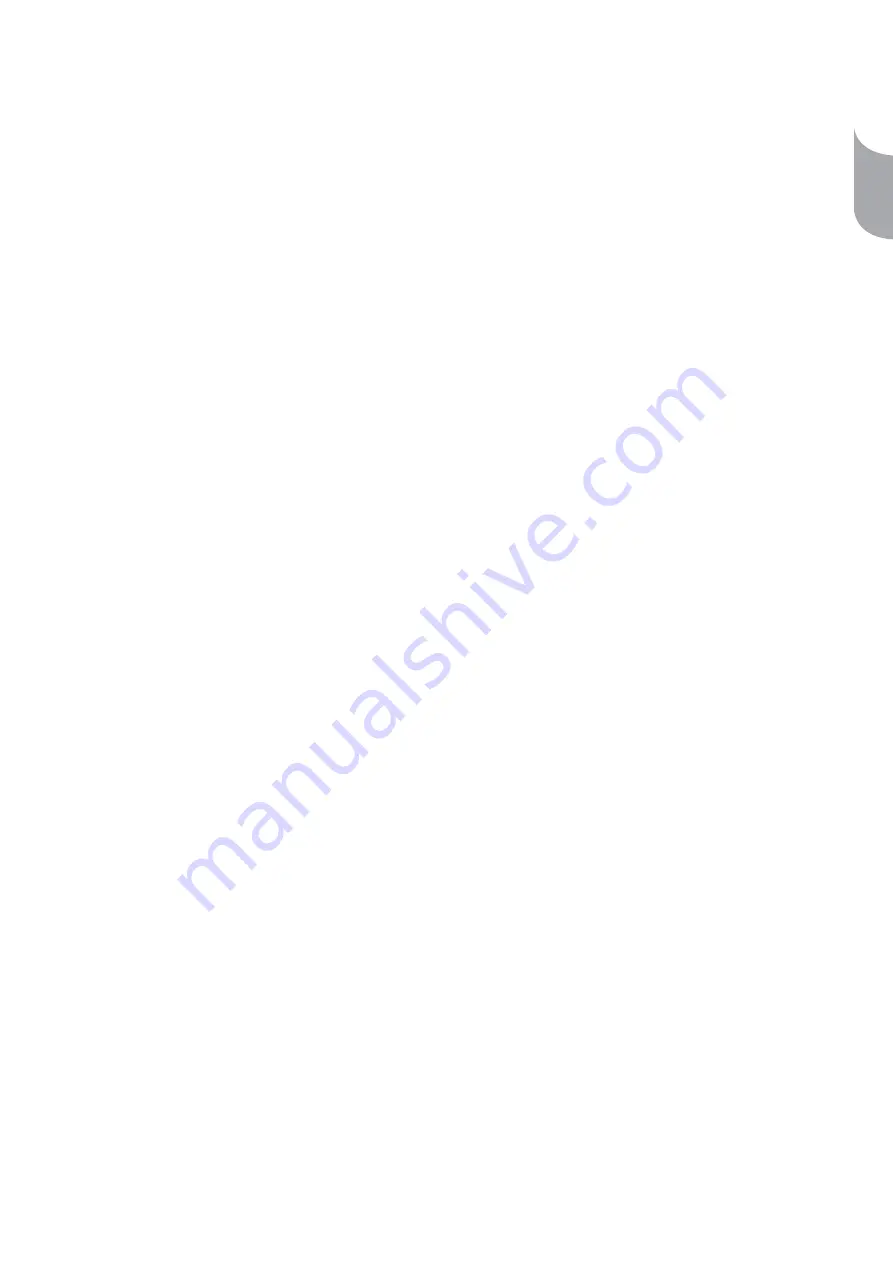
11
English
4.7 - Water flow control valves option
The bodies of the valves are designed to withstand an
operating pressure of 16 bar.
4.7.1 - Valve actuator
Carrier offers several types of actuator as a standard or
special option:
- On/Off 230 VAC.
-
3-Point 230 VAC.
- On/Off 24 VAC.
-
3-Point 24 VAC.
-
0-10 VDC, supplied with 24 VAC.
To enable the installation to be filled with water, the
pipework to be hydraulically balanced and the units to be
purged, the actuators must be powered so that valve
opening can be requested, either via the wall thermostats,
or by the BMS.
4.7.2 - Replacement procedure for the actuators
The valve actuators on both the chilled water and/or hot
water valves may be replaced if any fault is observed.
• Before any work, it is essential that the power supply
to the device is disconnected.
• Disconnect the actuator power supply cable:
-
Actuator used with the digital controller
Carrier:
Disconnect the power supply cable from the
actuator equipped with a quick connector
-
Actuator used with the electronic
thermostat:
Remove the protective plastic cover held in place
by 2 screws.
Disconnect the power supply cable from the
actuator connected to the quick connector; to do
so, press the tab on the terminal in question with
a screwdriver and pull out the wire.
• Remove the actuator and then refit in the reverse
order.
ATTENTION: Tighten the actuator on the valve body
using a maximum torque of 25 N
·
m.
4.7.3 - Replacement procedure for the valve bodies
CAUTION: Before any work, it is essential that the
power supply to the device is disconnected.
• Close the isolation valves in the pipework.
• Drain the isolated unit using the purge device
provided.
• Disconnect the hydraulic hoses by unscrewing the
union nuts.
• Uncouple the actuators, taking care to mark the cold
valve and hot valve.
• Disconnect the condensate drain hose held in place by
a collar (not supplied by Carrier).
• Remove the water flow control valve bodies.
Depending on the configuration of the device, the
valve coupling may be fitted with a hot/cold
changeover switch which must not be removed.
• Fit the new valve body to the coil (fit new gaskets).
• Refit the condensate pan/coil assembly.
• Refit the actuators, taking care to ensure that they are
correctly secured to the valve body.
•
Reconnect the flexible hoses by screwing the union
nuts back on. Tighten all the hydraulic connections
ensuring that all the gaskets have been replaced and
refitted (tightening torque: 20 Nm).
• Check that the water purge for the coil is in the closed
position.
• Open the isolation valve on the manifolds and purge
the coil.
• Power up the device once it has been confirmed that
no leaks have occurred.
ATTENTION: When fitting the new valve body, check
that the fluid flow is in the direction shown by the arrow
on the valve body. If fitted in the reverse direction, the
valve body will be damaged.
4.8 - Hose option
Ensure the following bend radii are respected:
•
Non-insulated hose: 72 mm,
•
Insulated hose: 106 mm.
4.9 - CO
2
sensors option
4.9.1 - Removal procedure for the Co
2
sensor
CAUTION: Before any work, it is essential that the
power supply to the device is disconnected.
• Open the grille: Fig. 10-11
• Remove the safety device: Fig 6
• Disconnect the cable from the sensor
• Remove the rivets holding the sensor in place.
• Replace the sensor
• Once work is complete, refit the assembly in the
reverse order to removal.
4.10 - Return air sensors option
4.10.1 - Removal procedure for the return air sensor
CAUTION: Before any work, it is essential that the
power supply to the device is disconnected.
• Open the grille: Fig. 10-11
• Remove the safety device: Fig 6
• Cut the cable ties securing the sensor in place
• Disconnect the sensor
• Replace the sensor
• Once work is complete, refit the assembly in the
reverse order to removal.
4.11 - Supply air sensors option
4.11.1 - Removal procedure for the supply air sensor
CAUTION: Before any work, it is essential that the
power supply to the device is disconnected.
• Open the grille: Fig. 10-11
• Remove the safety device: Fig 6
• Cut the cable ties securing the sensor in place
• Disconnect the sensor
• Replace the sensor
• Once work is complete, refit the assembly in the
reverse order to removal.
Summary of Contents for 36XB
Page 3: ...3 1 60 cm 60 cm 3 2 4 5 6 7 9 10 8 1 3 11...
Page 4: ...4 13 14 12 15...
Page 5: ...5 16a 18 17b 17a 16b...