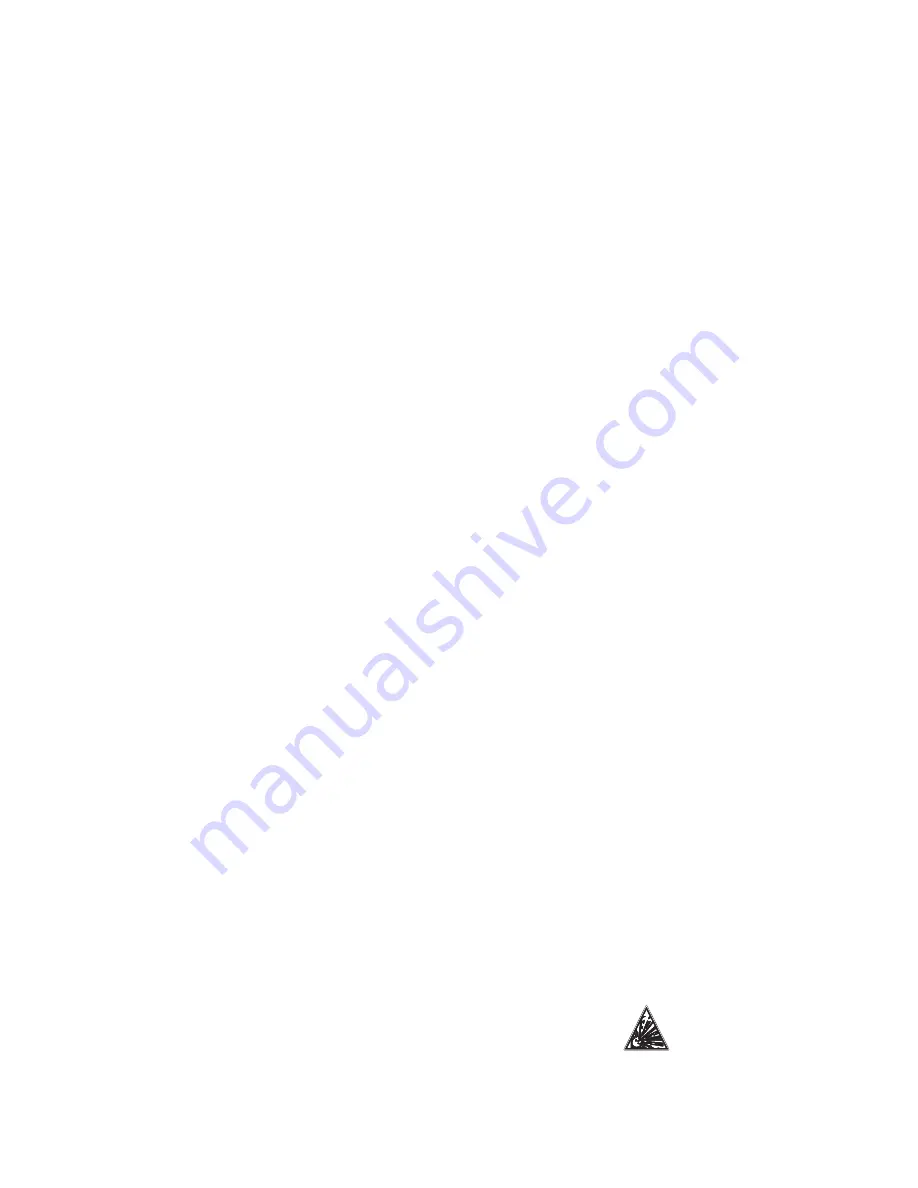
6
1.5 - Maintenance safety considerations
Engineers working on the electric or refrigeration compo-
nents must be authorized, trained and fully qualified to do so
(e.g. electricians trained and qualified in accordance with
IEC 60364 Classification BA4).
All refrigerant circuit work must be carried out by a trained
person, fully qualified to work on these units. He must have
been trained and be familiar with the equipment and the
installation. All welding operations must be carried out by
qualified specialists.
Aquasnap units use high-pressure R-410A refrigerant (the
unit operating pressure is above 40 bar, the pressure at 35°C
air temperature is 50% higher than for R-22). Special
equipment must be used when working on the refrigerant
circuit (pressure gauge, charge transfer, etc.).
Any manipulation (opening or closing) of a shut-off valve
must be carried out by a qualified and authorised engineer,
observing applicable standards (e.g. during draining
operations). The unit must be switched off while this is
done.
NOTE: The unit must never be left shut down with the
liquid line valve closed, as liquid refrigerant can be trapped
between this valve and the expansion device and lead to
the risk of a pressure increase. This valve is situated on
the liquid line before the filter drier box.
During any handling, maintenance and service operations
the engineers working on the unit must be equipped with
safety gloves, glasses, shoes and protective clothing.
Never work on a unit that is still energized. Never work
on any of the electrical components, until the general
power supply to the unit has been cut.
If any maintenance operations are carried out on the unit,
lock the power supply circuit in the open position and
secure the machine upstream with a padlock.
If the work is interrupted, always ensure that all circuits
are still deenergized before resuming the work.
ATTENTION: Even if the unit has been switched off, the
power circuit remains energized, unless the unit or circuit
disconnect switch is open. Refer to the wiring diagram for
further details. Attach appropriate safety labels.
If any work is carried out in the fan area, specifically if
the grilles or casings have to be removed, cut the power
supply to the fans to prevent their operation.
It is recommended to install an indicating device to show
if part of the refrigerant has leaked from the valve. The
presence of oil at the outlet orifice is a useful indicator that
refrigerant has leaked. Keep this orifice clean to ensure that
any leaks are obvious. The calibration of a valve that has
leaked is generally lower than its original calibration. The
new calibration may affect the operating range. To avoid
nuisance tripping or leaks, replace or re-calibrate the valve.
OpErATINg ChECKs:
•
ImpOrTANT INfOrmATION rEgArDINg
ThE rEfrIgErANT usED:
This product contains fluorinated greenhouse gas
covered by the Kyoto protocol.
refrigerant type: r-410A
global Warming potential (gWp): 1975
Periodic inspections for refrigerant leaks may be
required depending on European or local legislation.
Please contact your local dealer for more information.
•
During the life-time of the system, inspection and tests
must be carried out in accordance with national
regulations.
protection device checks:
•
If no national regulations exist, check the protection
devices on site in accordance with standard EN378:
once a year for the high-pressure switches, every five
years for external safety valves.
If the machine operates in a corrosive environment, inspect
the protection devices more frequently.
Regularly carry out leak tests and immediately repair any
leaks.
Ensure regularly that the vibration levels remain accept-
able and close to those at the initial unit start-up.
Before opening a refrigerant circuit, transfer the refrigerant
to bottles specifically provided for this purpose and consult
the pressure gauges.
Change the refrigerant after an equipment failure, following
a procedure such as the one described in Nf E29-795 or
carry out a refrigerant analysis in a specialist laboratory.
If the refrigerant circuit remains open for longer than a day
after an intervention (such as a component replacement),
the openings must be plugged and the circuit must be
charged with nitrogen (inertia principle). The objective is to
prevent penetration of atmospheric humidity and the result-
ing corrosion on the internal walls and on non-protected
steel surfaces.
1.6 - Repair safety considerations
All installation parts must be maintained by the personnel in
charge to avoid deterioration and injury. Faults and leaks
must be repaired immediately. The authorized technician
must have the responsibility to repair the fault immediately.
After each unit repair check the operation of the protection
devices and create a 100% parameter operation report.
Comply with the regulations and recommendations in unit
and HVAC installation safety standards, such as: EN 378,
ISO 5149, etc.
rIsK Of EXpLOsION
Never use air or a gas containing oxygen during leak tests to
purge lines or to pressurise a machine. Pressurised air
mixtures or gases containing oxygen can be the cause of an
explosion. Oxygen reacts violently with oil and grease.
Summary of Contents for 30RQ 039 Series
Page 49: ......