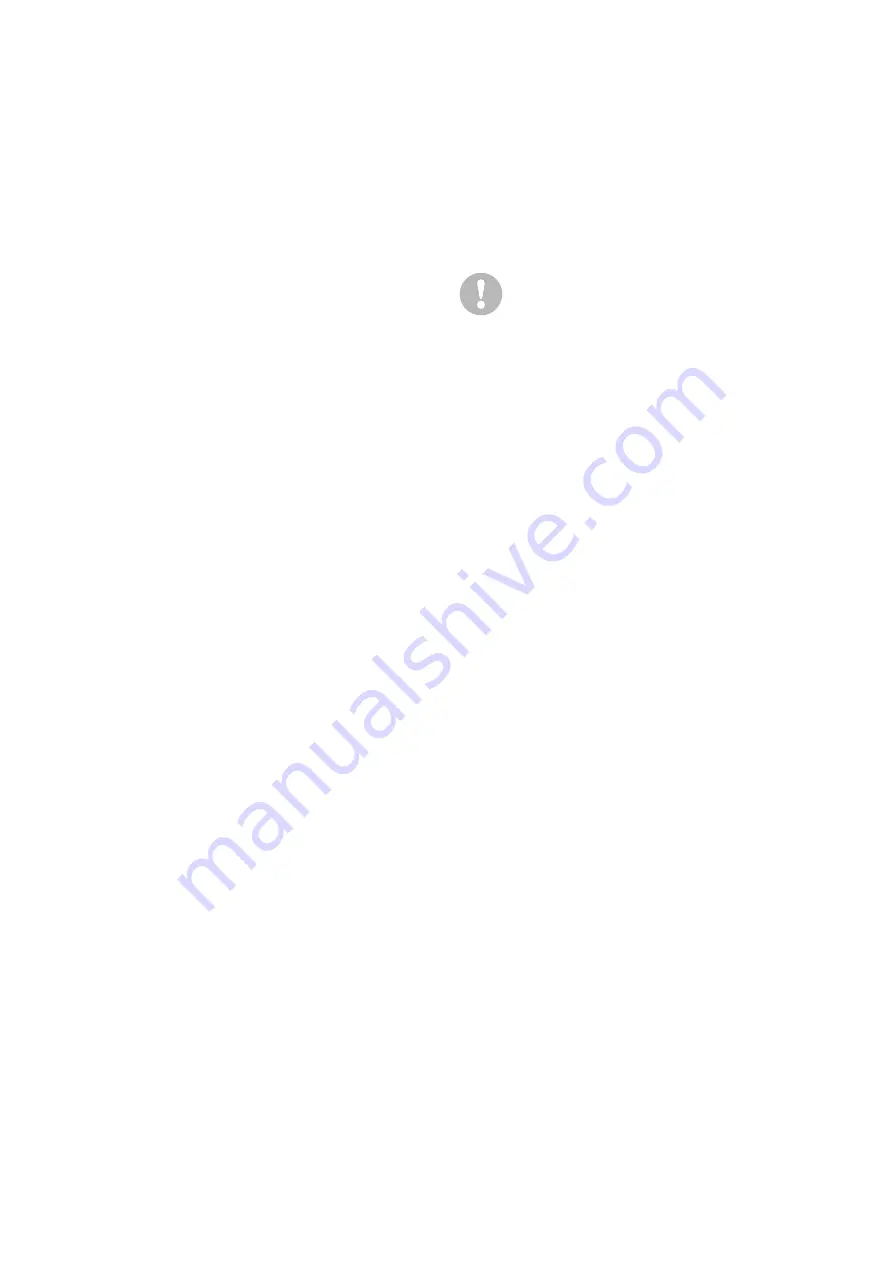
69
13.6 - Air-cooled exchanger
We recommend that coils are inspected regularly to check the
degree of fouling. This depends on the environment where the
unit is installed, in particular urban and industrial sites, and
for units installed near trees that shed their leaves.
Recommendations for maintenance and cleaning of micro-
channel coils (MCHE):
•
Regularly cleaning the coil surface is essential for correct
unit operation.
•
Eliminating contamination and removal of harmful
residue will increase the operating life of the coils and
the unit.
•
The maintenance and cleaning procedures below are part
of the regular maintenance to increase the operating life
of coils.
•
Specific recommendation in case of snow: For long term
storage, regularly check that no snow has accumulated
on the coil.
•
Clean the surface of the coil by spraying the coil regularly
and uniformly from bottom to top, orienting the water
jet at right angles to the surface. Do not exceed a water
pressure of 6200 kPa (62 bar) or an angle of 45° related
to the coil. The nozzle must be at least 300 mm away from
the coil surface.
•
Clean and scrub the entire connection with a flexible
Nylon, PolyPro
®
or Tynex
®
brush and low pressure tap
water.
Level 1 cleaning:
•
Remove all foreign objects or fragments/debris attached to
the coil surface or wedged between the chassis and the
supports.
•
Use a low pressure dry air jet to remove all traces of dust
from the coil.
Level 2 cleaning:
•
Carry out the level 1 cleaning operations.
•
Clean the coil using suitable products.
Use appropriate PPE including safety glasses and/or mask,
waterproof clothes and safety gloves. It is recommended to
wear clothing that covers the whole body.
Specific products approved by the manufacturer for cleaning
coils are available from the manufacturer's spare parts
network. The use of any other product is strictly prohibited.
After the cleaning product is applied, rinsing with water is
mandatory (see manufacturer's standard RW01-25).
IMPORTANT:
Never use a pressure water spray without a large diffuser.
Concentrated and/or rotating water jets are strictly forbidden.
Never use a fluid with a temperature above 45°C to clean the
air heat exchangers.
Correct and frequent cleaning (approximately every three
months) will prevent 2/3 of the corrosion problems. Protect
the electrics box during cleaning operations.
13.7 - Water type heat exchanger
Check that:
•
The insulation has not been detached or torn during
operations,
•
The heaters and probes are operating and correctly
positioned in their support,
•
The water-side connections are clean and show no sign
of leakage,
•
The periodic inspections required by the local regulations
have been carried out
13.8 - Variable frequency drive
Before any work on the frequency inverter, ensure that
the circuit is isolated and there is no voltage present
(reminder: the capacitors take approximately 5
minutes to discharge once the circuit breaker has been
opened). Only appropriately qualified personnel are
authorised to work on the frequency inverter.
In case of any alarm or persistent problem related to the
frequency inverter, contact the manufacturer's service.
The frequency inverters fitted on the units do not require a
dielectric test, even if being replaced: they are systematically
checked before delivery. Moreover, the filtering components
installed in the frequency inverter can falsify the measurement
and may even be damaged. If there is a need to test the
insulation of the unit components (fan motors and pumps,
cables, etc.), the variable frequency drive must be disconnected
at the power circuit.
13.9 - Refrigerant volume
It is essential to run the unit in cooling mode to find out
whether the charge is correct; this is done by checking the
actual subcooling.
Following a slight leak, it will be possible to feel a drop in the
refrigerant charge from the initial charge, and this will affect
the subcooling value obtained at the air-cooled exchanger
outlet; it cannot, however, be felt in heating mode.
IMPORTANT:
it is therefore not possible to optimise the charge in heating
mode following a leak. The unit must be run in cooling mode
if the charge needs topping up.
Summary of Contents for 30RBM 160
Page 75: ......