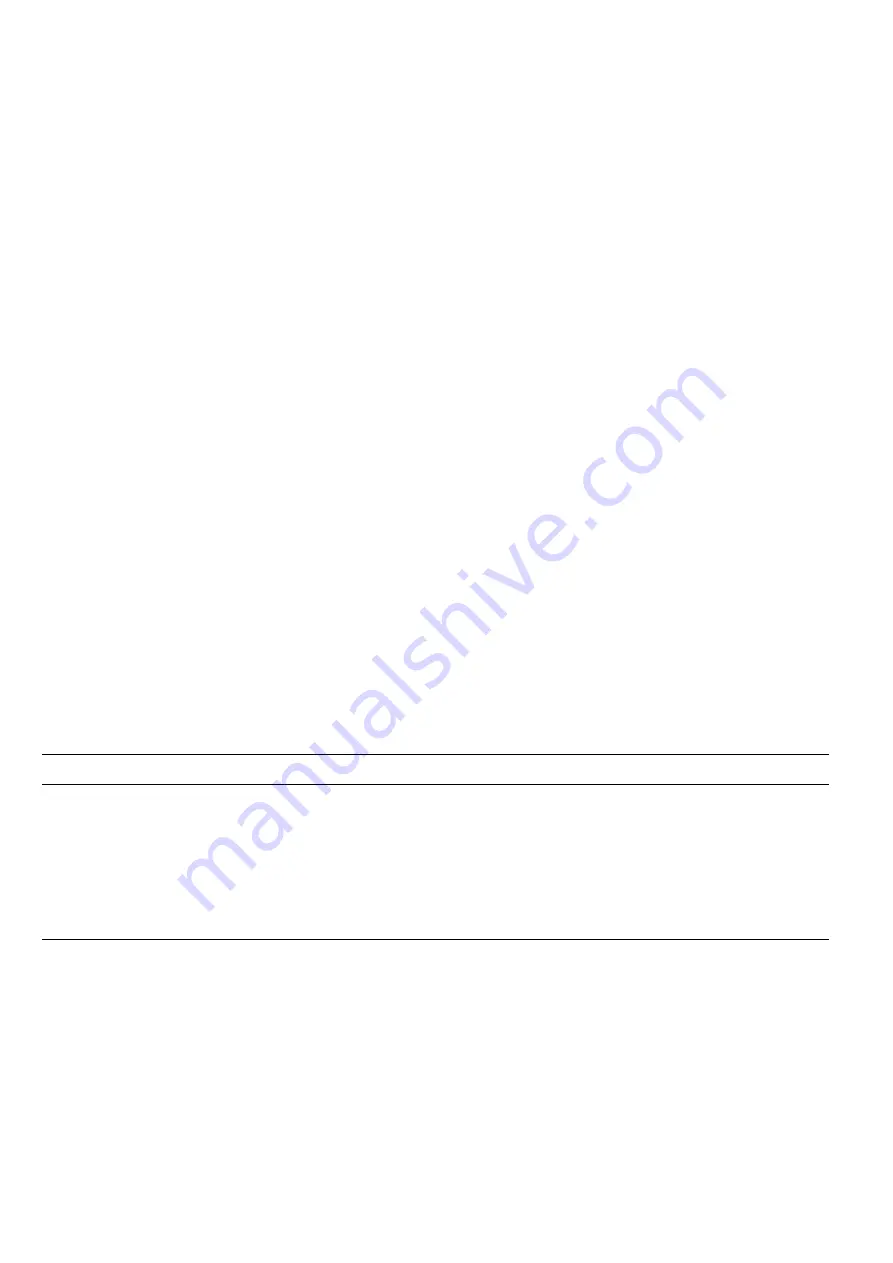
18
8 - RECOMMENDED WIRE SECTIONS
Wire sizing is the responsibility of the installer, and depends on
the characteristics and regulations applicable to each installation
site. The following is only to be used as a guideline, and does
not make Carrier in any way liable. After wire sizing has been
completed, using the certified dimensional drawing, the instal-
ler must ensure easy connection and define any modifications
necessary on site. The connections provided as standard for the
field-supplied power entry cables to the general disconnect/
isolator switch are designed for the number and type of wires,
listed in the table below.
The calculations are based on the maximum machine current
(see electrical data tables) and the standard installation practises,
in accordance with IEC 60364, table 52C.
-
For 30RA units, installed outside, the following standard
installation practises have been maintained:
No.17: suspended aerial lines, and No. 61: buried
conduit with a derating coefficient of 20.
The calculation is based on PVC or XLPE insulated
cables with copper core.
A maximum ambient temperature of 46°C has been
taken into consideration.
The given wire length limits the voltage drop to
< 5% (length L in metres - see table below).
IMPORTANT: Before connection of the main power cables
(L1 - L2 - L3) on the terminal block, it is imperative to check
the correct order of the 3 phases before proceeding to the
connection on the main disconnect/isolator switch.
Unit
S Min. (mm
2
)
Cable type
L (m)
S Max. (mm
2
)
Cable type
L (m)
by phase
by phase
30RA 040
1x 6
XLPE Cu
90
1x 16
PVC Cu
245
30RA 050
1x 6
XLPE Cu
80
1x 25
PVC Cu
300
30RA 060
1x 10
XLPE Cu
110
1x 25
PVC Cu
300
30RA 070
1x 10
XLPE Cu
100
1x 35
PVC Cu
310
30RA 080
1x 16
XLPE Cu
125
1x 50
PVC Cu
350
30RA 090
1x 16
XLPE Cu
115
1x 70
PVC Cu
380
30RA 100
1x 25
XLPE Cu
145
1x 70
PVC Cu
380
30RA 120
1x 25
XLPE Cu
135
1x 95
PVC Cu
410
30RA 140
1x 35
XLPE Cu
150
1x 120
PVC Cu
435
30RA 160
1x 50
XLPE Cu
180
1x 120
XLPE Cu
400
30RA 200
1x 70
XLPE Cu
180
1x 150
XLPE Cu
335
30RA 240
1x 70
XLPE Cu
180
1x 185
XLPE Cu
345
S
Power supply cable section (see the diagram in chapter: "Electrical connection")
8.1 - Field control wiring
For the field control wiring of the following elements please
refer to the 30RA/RH - RY/RYH “B” series Pro-Dialog Plus
Control manual, and the certified wiring diagram supplied with
the unit:
-
Unit start/stop
-
Heating/cooling selection
-
Set-point selection
-
Customer interlock - (example: auxiliary contact of the
chilled water pump contactor)
-
General alarm reporting, circuit A and circuit B
Summary of Contents for 30RA040B
Page 35: ...35...