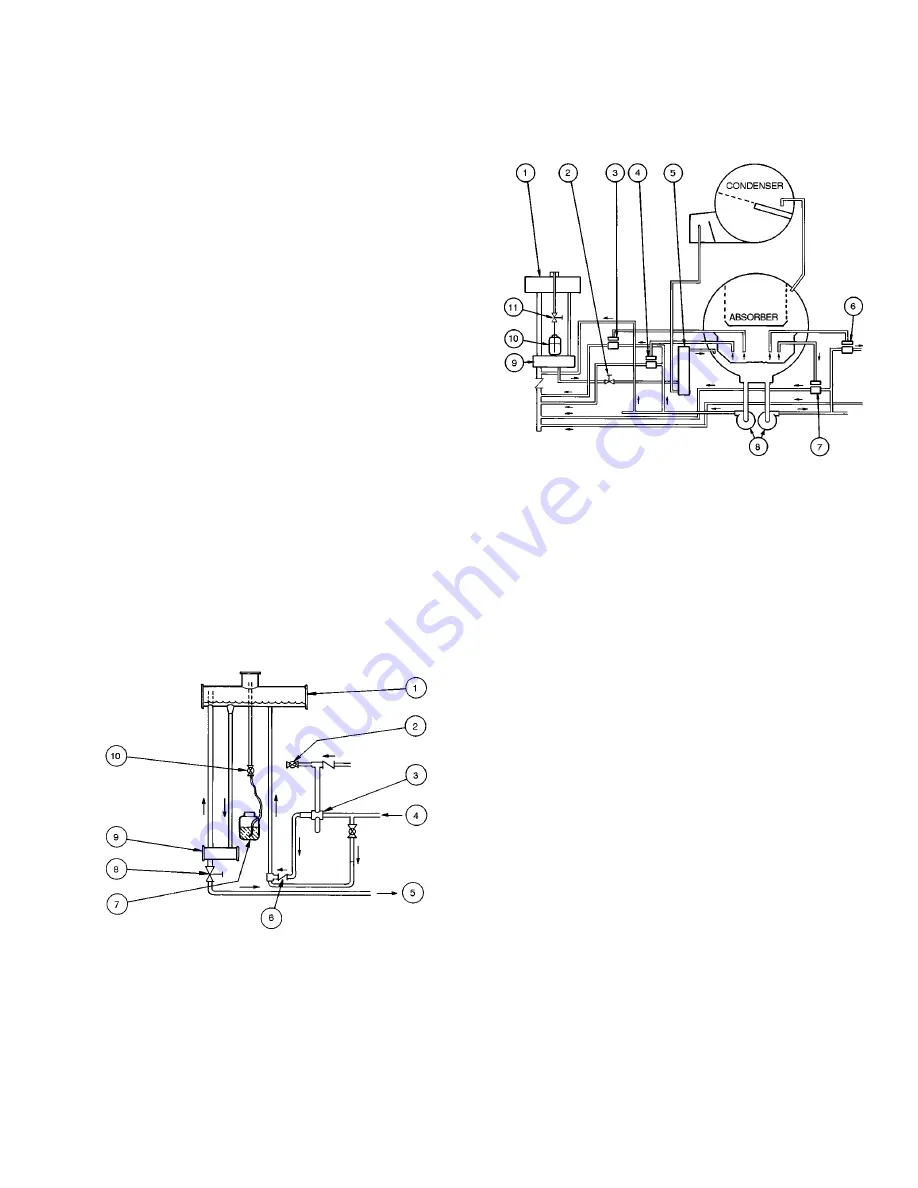
Purge System —
The basic components and flow cir-
cuits of the motorless purge are shown in Fig. 8 and 9.
The purge system automatically removes noncondens-
ables from the machine and transfers them to a storage cham-
ber where they cannot affect machine operation.
Noncondensables are gases such as N
2
, O
2
, and H
2
which
will not condense at the normal chiller operating tempera-
tures and pressures and, because they reduce the machine
vacuum, they reduce the machine capacity.
Some hydrogen (H
2
) gas is liberated within the machine
during normal operation and its rate of generation is con-
trolled by the solution inhibitor. The presence of most other
gases in the machine would occur either through a leak (the
machine is under a deep vacuum) or by entrainment in the
refrigerant and solution at initial charging. During opera-
tion, any noncondensables accumulate in the absorber, which
is the lowest pressure area of the machine.
For purging, the gases are continuously drawn from the
absorber into the lower pressure of eductors, where they are
entrained in solution flowing from the solution pump. The
mixture then continues on to the purge storage tank. The non-
condensables are released in a separator and the solution flows
back to the absorber by way of the generator overflow pipe.
Noncondensables accumulate in the purge storage tank where
they are isolated from the rest of the machine. The
storage chamber is initially filled with solution that is dis-
placed as the chamber gradually fills with noncondensables.
These gases then must be periodically exhausted from the
storage chamber by a manual procedure. This is begun by
closing a solution return valve to force solution from the pump
into the chamber to compress the noncondensables to above
atmospheric pressure. Then an exhaust valve is opened to
bleed the noncondensables to the atmosphere through solu-
tion in an exhaust bottle. This operation is described in the
Maintenance Procedures, Purge Manual Exhaust Procedure
section, page 31.
Some chillers also have an optional, permanently in-
stalled vacuum pump system (as shown in Fig. 5)
to remove noncondensables directly from the absorber for
machine evacuation at initial start-up and after service work.
The pump is wired into the chiller control circuit for power.
LEGEND
1 — Storage Chamber
6 — Check Valve
2 — Auxiliary Valve
7 — Exhaust Liquid Seal Bottle
3 — Eductor Device
8 — Solution Return Valve
4 — Solution from Solution
9 — Separation Chamber
Pump
10 — Exhaust Valve
5 — Solution Returning to
Absorber
Fig. 8 — Purge System, 16JT810-880
LEGEND
1 — Storage Chamber
7 — Eductor
2 — Solution Return Valve
8 — Hermetic Solution Pumps
3 — Eductor
9 — Separation Chamber
4 — Eductor
10 — Exhaust Bottle
5 — J-Loop Box
11 — Exhaust Valve
6 — Eductor
NOTE: Number of eductors varies from one on smaller sizes to 4 on
larger sizes.
Fig. 9 — Purge System, 16JT080-150, 080L-150L
9
Summary of Contents for 16JT Series
Page 11: ...Fig 10 Typical Wiring Diagram 11 ...
Page 12: ...Fig 10 Typical Wiring Diagram cont 12 ...
Page 13: ...Fig 11 Typical Control Wiring 13 ...
Page 43: ......