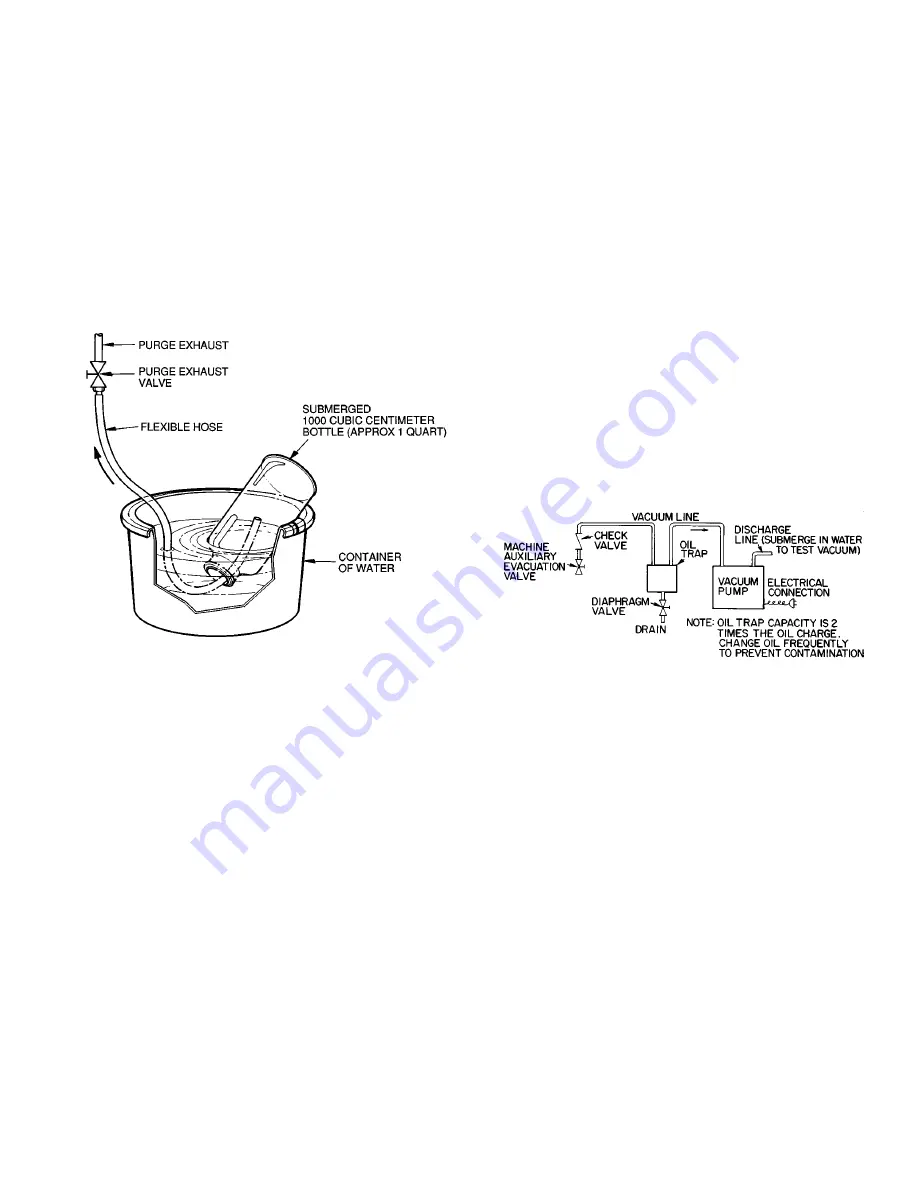
6. Close exhaust valve and mark liquid level on inverted bottle.
Remove bottle from container.
7. Return purge to normal operation. Replace exhaust bottle
(Fig. 25). Open solution return valve (Fig. 8 and 9).
8. Measure the amount of noncondensables removed. If a
graduated bottle is used, the amount (volume) of noncon-
densables removed is indicated by mark on bottle. If a
nongraduated bottle is used, empty the bottle and then fill
the bottle with liquid to the exhaust mark. Pour the liquid
into a graduated container to measure the volume dis-
placed.
9. If the operating accumulation rate has increased substan-
tially from previous rates, machine has an air leak or re-
quires additional inhibitor. Have a solution sample ana-
lyzed (see Solution Analysis section, page 34, to determine
the proper corrective action. If a leak is indicated, it must
be found and repaired as soon as possible to minimize
internal corrosion damage.)
Machine Leak Test —
All joints welded at machine
installation must be leak tested before initial start-up of ma-
chine. Joints must also be leak tested after repair. If there is
any indication of air leakage, leak test the entire machine.
1. Be sure auxiliary evacuation valve, purge exhaust valve,
and all pump service valves are closed.
2. Break machine vacuum with dry nitrogen. Pressurize ma-
chine to 6 psig (40 kPa) with tracer gas. Charge the ni-
trogen and refrigerant through the auxiliary evacuation
valve.
3. Use dry nitrogen to raise machine pressure to 12 psig
(80 kPa). Do not exceed 12 psig (80 kPa).
4. Leak test all joints with an electronic leak detector.
5. Correct all leaks; retest to ensure repair.
6. Release
machine
pressure
and
perform
machine
evacuation.
Machine Evacuation —
Evacuation is required for the
removal of excessive noncondensables from the machine. The
machine must be evacuated after air has entered the machine
during service work or when absorber loss is greater than
5° F (3° C) during operation.
1. Connect an auxiliary evacuation device to the auxiliary
evacuation valve (Fig. 28). Use a line size at least equal
to the connection size on the auxiliary device and keep
the line as short as possible. A check valve must be used
on the suction lines. Be sure all connections are vacuum
tight.
A vacuum pump oil trap can also serve as a cold trap if
it has a center well to hold dry ice or a mixture of salt and
ice. Any water vapor that can contaminate the oil in the
vacuum pump is condensed and removed by the cold trap.
The cold trap reduces the time required for evacuation
and eliminates the need for frequent replacement of the
pump oil charge.
2. Start evacuation device. After one minute, open auxiliary
evacuation valve. If the machine is not operating, reduce
machine absolute pressure to the pressure equivalent of
the saturation temperature of the refrigerant. If the ma-
chine is operating, evacuate until absorber loss is 5° F
(3° C) or less.
3. Close auxiliary evacuation valve and turn off the auxil-
iary evacuation device.
4. Machine evacuation can remove octyl alcohol. Check a
solution sample for the presence of octyl alcohol and add
if necessary (see Adding Octyl Alcohol, page 35.)
Fig. 27 — Collecting Noncondensables
Fig. 28 — Machine Evacuation Device
33
Summary of Contents for 16JT Series
Page 11: ...Fig 10 Typical Wiring Diagram 11 ...
Page 12: ...Fig 10 Typical Wiring Diagram cont 12 ...
Page 13: ...Fig 11 Typical Control Wiring 13 ...
Page 43: ......