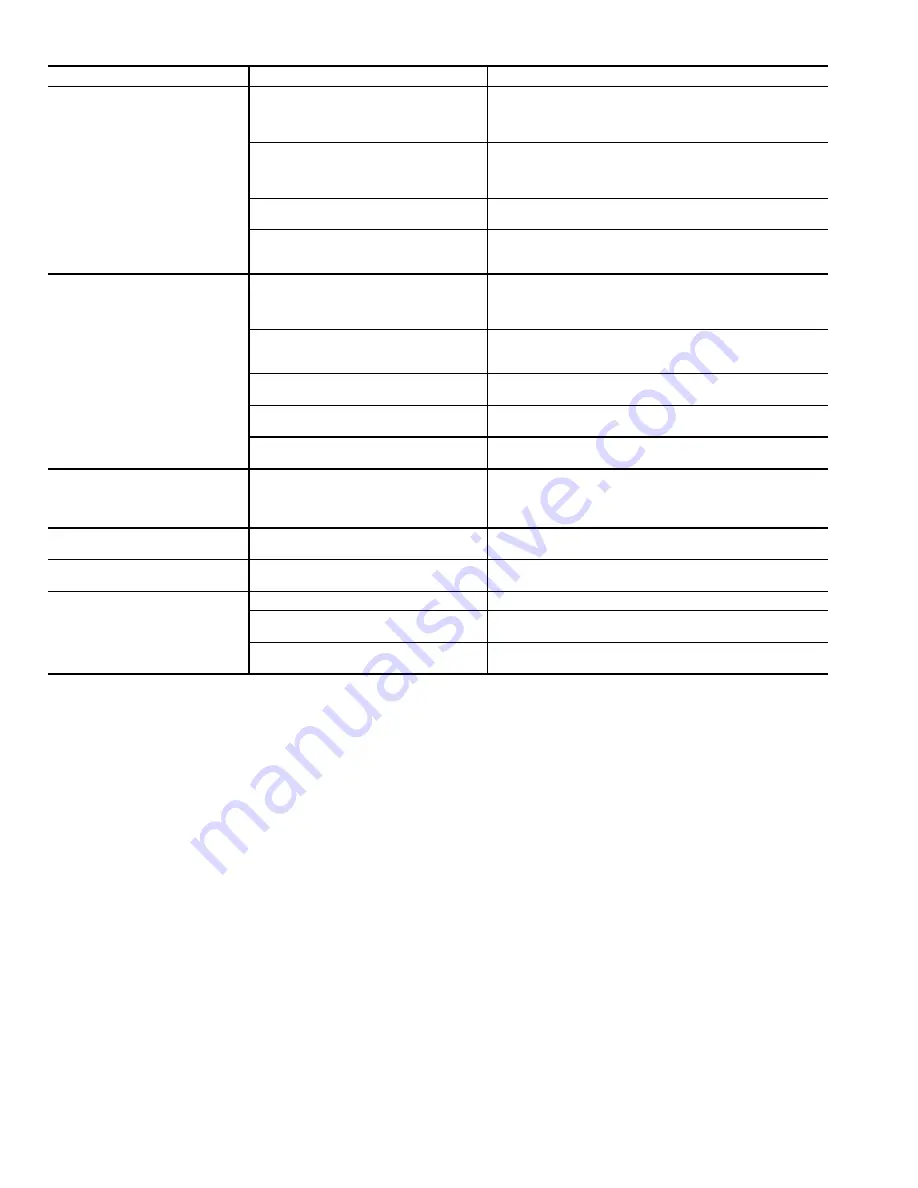
TROUBLESHOOTING GUIDE (cont)
PROBLEM/SYMPTOM
PROBABLE CAUSE
REMEDY
Inadequate Purging
(Low machine capacity and
high absorber loss — see
Absorber Loss Determination,
page 31.)
Air leakage in vacuum side of machine
(high noncondensable accumulation rate)
Have solution analyzed for indication of air leaks. Leak test
and repair if necessary (see Noncondensable Accumu-
lation Rate, Solution Analysis, and Machine Leak Test
sections on pages 31, 34, and 31, respectively).
Inhibitor depleted (high noncondensable
accumulation rate)
Have solution analyzed. Add inhibitor and adjust solution
alkalinity if necessary (see Noncondensable Accumulation
Rate, Solution Analysis, and Inhibitor sections on pages 31,
32, respectively).
Purge valves not positioned correctly
Check valve positions (see Purge Manual Exhaust Procedure
section on page 31).
Purge solution supply lines crystallized
(not able to exhaust purge)
Heat solution supply lines (see Purge Manual Exhaust proce-
dure and Solution Decrystallization sections on pages 31
and 40).
Solution Crystallization During
Operation
(Strong solution overflow
pipe hot.)
Cycle-Guard™ control malfunction
(solution overconcentration)
Check refrigerant charge, thermoswitch calibration, and
transfer valve operation. (see Refrigerant Charge Adjust-
ment, Cycle-Guard System Operation, and Thermoswitch
Adjustment sections on pages 35, 35, and 36, respectively).
Noncondensables in machine
(high absorber loss)
Check absorber loss (see Absorber Loss Determination
section on page 31). If above 5° F (2.8° C), see Causes and
Remedies under Inadequate Purging above.
High steam pressure or hot water
temperature (above design)
See Machine Selection Data provided with the machine.
Set at design.
Absorber tubes fouled
(poor heat transfer)
Clean tubes. Determine if water treatment is necessary.
Octyl alcohol depletion
Check solution sample and add octyl alcohol if necessary
(see Adding Octyl Alcohol section on page 35).
Solution Crystallization at
Shutdown
(Crystallization symptoms when
machine is started.)
Insufficient solution dilution at shutdown
After shutdown, restart machine and measure concentration
of weak solution (see Solution or Refrigerant Sampling sec-
tion on page 34). If above 56%, check dilution level switch and
Cycle-Guard transfer valve.
Abnormal Noise from
Solution Pump
Cavitation of solution pump
(low solution level in absorber)
Open the Cycle-Guard valve manually (toggle switch
43-RV) for about 3 minutes while machine is running.
Abnormal Noise from
Refrigerant Pump
Temperature of cooling water
supply below 59 F (15 C).
Raise cooling water temperature above 59 F (15 C). Stop
the machine and then restart it about 20 minutes later.
Frequent Cycle-Guard
Operation
Fouled absorber or evaporator tubes
Clean tubes.
Excessive noncondensable gas
(high absorber loss)
See Inadequate Purging.
Refrigerant overcharge or tube leak.
Remove refrigerant to trim charge, per start-up instructions.
Repair tube leak.
42
Summary of Contents for 16JT Series
Page 11: ...Fig 10 Typical Wiring Diagram 11 ...
Page 12: ...Fig 10 Typical Wiring Diagram cont 12 ...
Page 13: ...Fig 11 Typical Control Wiring 13 ...
Page 43: ......