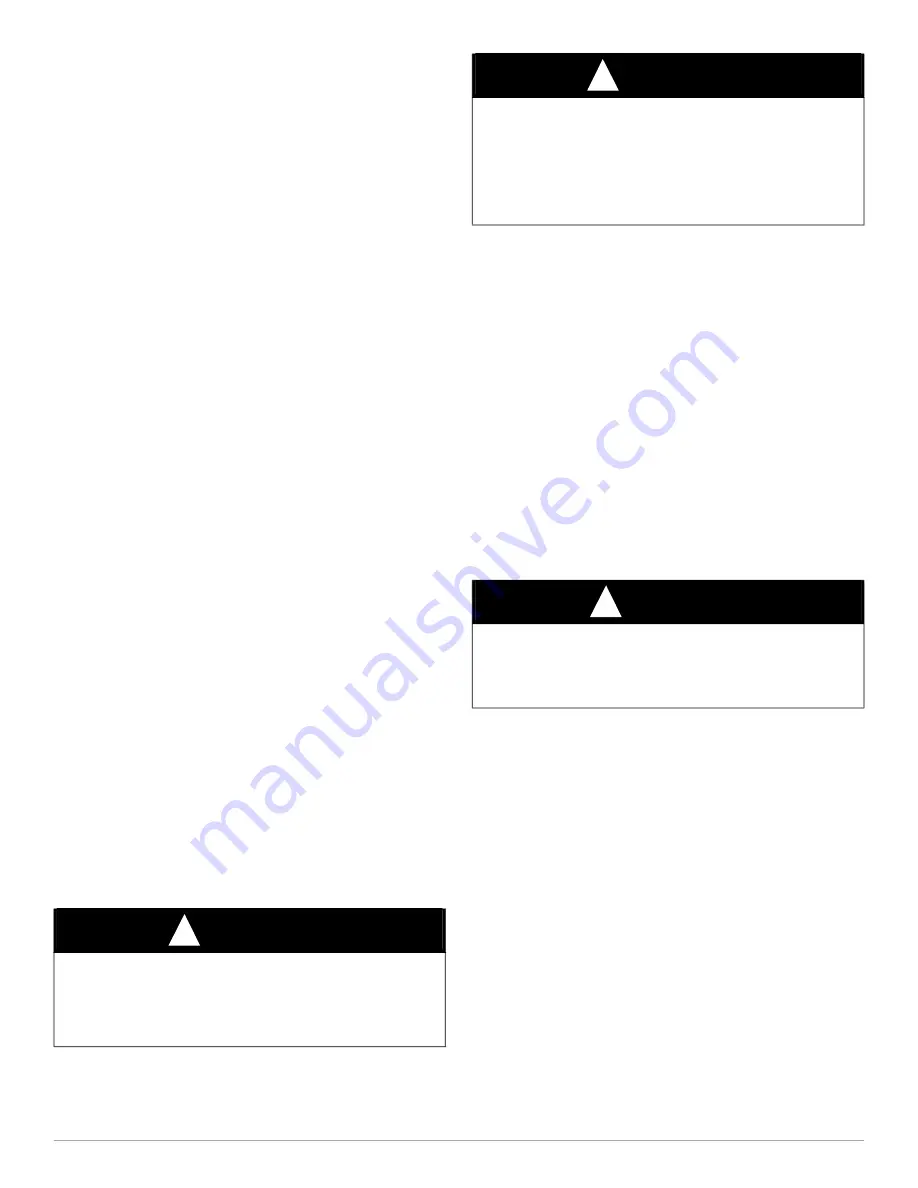
: Service Manual
Manufacturer reserves the right to change, at any time, specifications and designs without notice and without obligations.
18
2. Temperature of windings must be as specified, usually about 70_F
(21.1ºC) .
3. Resistance measuring instrument must have an accuracy within ±
5-10 percent. This requires an accurate ohmmeter such as a
Wheatstone bridge or null balance-type instrument.
4. Motor must be dry or free from direct contact with liquid
refrigerant.
Make This Critical Test
(Not advisable unless above conditions are met.)
1. Be sure all power is off.
2. Discharge all capacitors.
3. Remove wires from terminals C, S, and R.
4. Place instrument probes together and determine probe and lead wire
resistance.
5. Check resistance readings from C-R, C-S, and R-S.
6. Subtract instrument probe and lead resistance from each reading.
If any reading is within ±20 percent of known resistance, motor is
probably normal. Usually a considerable difference in reading is noted if
a turn-to-turn short is present.
System Clean-Up After Burnout
Turn off all power to unit before proceeding. Wear safety glasses and
gloves when handling refrigerants. Acids formed as a result of motor
burnout can cause burns.
NOTE:
To analyze level of suspected contamination from compressor
burnout, use Total Test™. See your distributor/branch.
Some compressor electrical failures can cause motor to overheat. When
this occurs, byproducts, which include sludge, carbon, and acids,
contaminate system. If burnout is severe enough, system must be
cleaned before replacement compressor is installed. The 2 types of
motor burnout are classified as mild or severe.
In mild burnout, there is little or no detectable odor. Compressor oil is
clear or slightly discolored. An acid test of compressor oil will be
negative. This type of failure is treated the same as mechanical failure.
Liquid line strainer should be removed and liquid line filter drier
installed.
In a severe burnout, there is a strong, pungent, rotten egg odor.
Compressor oil is very dark. Evidence of burning may be present in
tubing connected to compressor. An acid test of compressor oil will be
positive. Complete system must be reverse flushed with refrigerant.
Metering device must be cleaned or replaced. In a heat pump,
accumulator and reversing valve are replaced. These components are
also removed and bypassed during reverse flushing procedure. Remove
and discard liquid line strainer. After system is reassembled, install
liquid and suction line filter driers. Run system for 2 hrs. Discard both
driers and install new liquid line drier only.
Compressor Removal and Replacement
Once it is determined that compressor has failed and the reason
established, compressor must be replaced.
1. Shut off all power to unit.
2. Remove and recover all refrigerant from system until pressure
gages read zero psig. Use all service ports.
3. Disconnect electrical plug from compressor. Disconnect or remove
crankcase heater (if equipped) and remove compressor holddown
nuts and washers.
4. Cut compressor from system with tubing cutters. Do not use
brazing torch for compressor removal. Oil vapor may ignite when
compressor is disconnected.
5. Scratch matching marks on stubs in old compressor. Make
corresponding marks on replacement compressor.
6. Use torch to remove stubs from old compressor and to reinstall
them in replacement compressor.
7. Use copper couplings to tie compressor back into system.
8. Evacuate system, recharge, and check for normal system operation.
9. Compressors have copper plated steel suction ports. Excess heat
during brazing will burn off copper plating. See Brazing section for
additional information.
Outdoor Fan Adjustment
1. Shut off unit power supply and install lockout tag.
2. Remove outdoor-fan assembly (grille, motor, motor cover, and fan)
by removing screws and flipping assembly onto unit top cover.
3. Inspect the fan blades for cracks or bends.
4. If fan needs to be removed, loosen the setscrew and slide the fan off
the motor shaft.
5. When replacing fan blade, position blade as shown in
Tighten setscrews.
Fan Motor
The fan motor rotates the fan blade that draws air through the outdoor
coil to exchange heat between the refrigerant and the air. Motors are
totally enclosed to increase reliability. This eliminates the need for a rain
shield. For the correct position of fan blade assembly, the fan hub should
be flush with the motor shaft. Replacement motors and blades may vary
slightly.
WARNING
!
PERSONAL INJURY HAZARD
Failure to follow this caution may result in personal injury. Wear safety
glasses, protective clothing, and gloves when handling refrigerant and
observe the following:
The high flow service valve is equipped with Schrader valves.
WARNING
!
PERSONAL INJURY AND ENVIRONMENTAL HAZARD
Failure to follow this warning could result in personal injury or death.
Relieve pressure and recover all refrigerant before system repair or
final unit disposal. Use all service ports and open all flow-control
devices, including solenoid valves. Federal regulations require that you
do not vent refrigerant to the atmosphere. Recover during system repair
or final unit disposal.
CAUTION
!
UNIT OPERATION HAZARD
Failure to follow this caution may result in damage to unit components.
Keep the condenser fan free from all obstructions to ensure proper
cooling operation. Never place articles on top of unit.