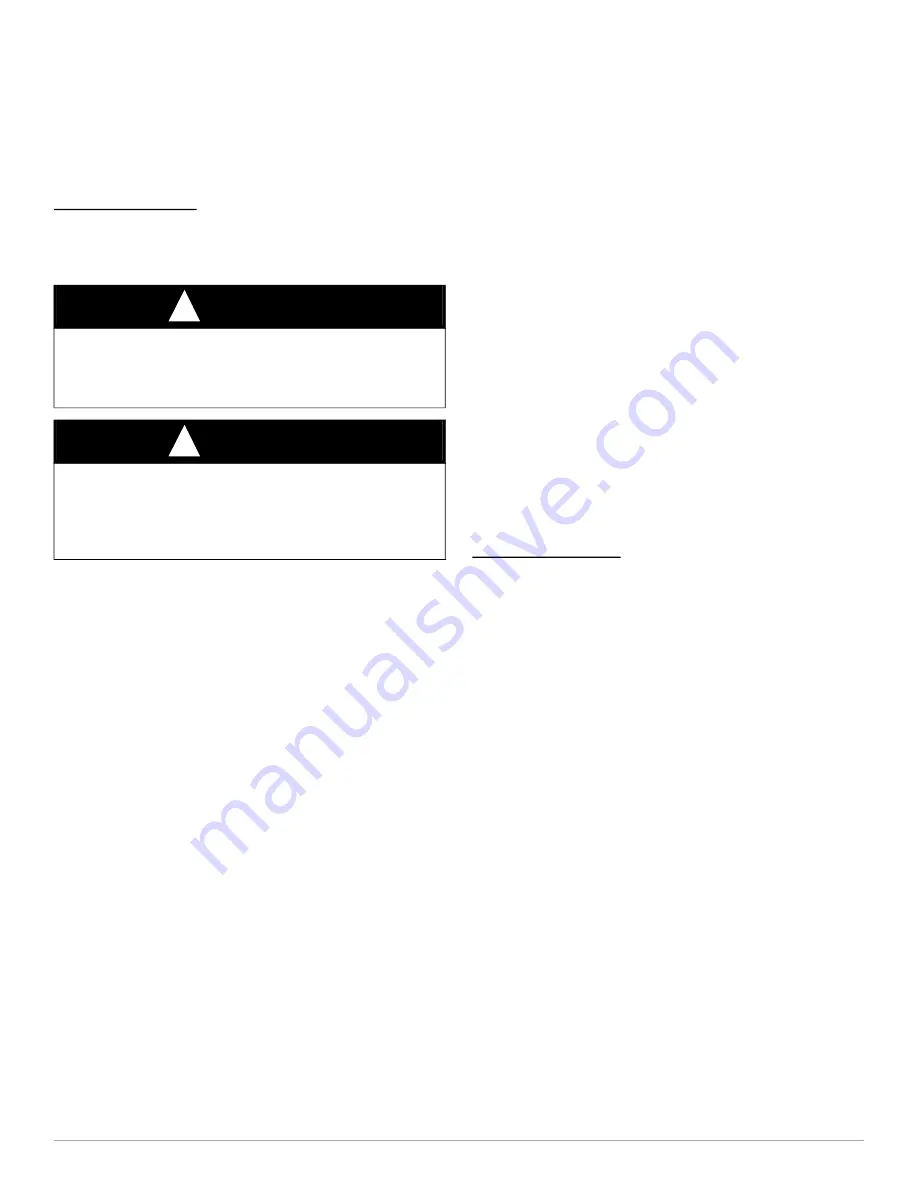
: Service Manual
Manufacturer reserves the right to change, at any time, specifications and designs without notice and without obligations.
15
extreme high pressure. The relief port has an operating range between
550 to 625 psig differential pressure (Copeland) and 550 to 650 psig
differential pressure (Danfoss) for R-410A refrigerant. Scrolls have a
variety of shut down solutions, depending on model, to prevent
backward rotation and eliminate the need for cycle protection.
Compressor Failures
Compressor failures are classified in 2 broad failure categories;
mechanical and electrical. Both types are discussed below.
Mechanical Failures
A compressor is a mechanical pump driven by an electric motor
contained in a welded or hermetic shell. In a mechanical failure, motor
or electrical circuit appears normal, but compressor does not function
normally.
Locked Rotor
In this type of failure, compressor motor and all starting components are
normal. When compressor attempts to start, it draws locked rotor current
and cycles off on internal protection. Locked rotor current is measured
by applying a clamp-on ammeter around common (blk) lead of
compressor. Current drawn when it attempts to start is then measured.
Locked rotor amp (LRA) value is stamped on compressor nameplate.
If compressor draws locked rotor amps and all other external sources of
problems have been eliminated, compressor must be replaced. Because
compressor is a sealed unit, it is impossible to determine exact
mechanical failure. However, complete system should be checked for
abnormalities such as incorrect refrigerant charge, restrictions,
insufficient airflow across indoor or outdoor coil, etc., which could be
contributing to the failure.
Runs, Does Not Pump
In this type of failure, compressor motor runs and turns compressor, but
compressor does not pump refrigerant. A clamp-on ammeter on common
leg shows a very low current draw, much lower than rated load amp
(RLA) value stamped on compressor nameplate. Because no refrigerant
is being pumped, there is no return gas to cool compressor motor. It
eventually overheats and shuts off on its internal protection.
Noisy Compressor
Noise may be caused by a variety of internal and external factors.
Careful attention to the “type” of noise may help identify the source.
The following are some examples of abnormal conditions that may
create objectionable noise:
1. A gurgling sound may indicate a liquid refrigerant floodback during
operation. This could be confirmed if there is no compressor
superheat. A compressor superheat of “0” degrees would indicate
liquid refrigerant returning to the compressor. Most common
reasons for floodback are: loss of evaporator blower, dirty coils, and
improper airflow.
2. A rattling noise may indicate loose hardware. Inspect all unit
hardware including the compressor grommets.
3. An internal “thunking”, “thumping”, “grinding” or “rattling” noise
could indicate compressor internal failures and may be verified by
comparing the compressor amperage to what the compressor should
be drawing according to a manufacturer’s performance data.
4. A whistling or squealing noise during operation may indicate a
partial blockage of the refrigerant charge.
5. A whistle on shut down could indicate a partial leak path as
refrigerant is equalizing from high to low side. On occasion, an
in-line discharge check valve has prevented this sound.
6. If a compressor hums but won’t start it could indicate either a
voltage or amperage issue. Verify adequate voltage and operational
start components if installed. If it is drawing excessive amperage
and voltage doesn’t appear to be the problem it may be assumed a
locked condition. Ensure refrigerant has had ample time to
equalize and boil out of the compressor before condemning.
7. When a heat pump switches into and out of defrost, a ”swooshing”
noise is expected due to the rapid pressure change within the
system. Check that the defrost thermostat or thermistor is operating
properly. Insulating the defrost sensing device may also help.
Electrical Failures
The compressor mechanical pump is driven by an electric motor within
its hermetic shell. In electrical failures, compressor does not run
although external electrical and mechanical systems appear normal.
Compressor must be checked electrically for abnormalities.
Before troubleshooting compressor motor, review this description of
compressor motor terminal identification.
Single-Phase Motors
To identify terminals C, S, and R:
1. Turn off all unit power.
2. Discharge run and start capacitors to prevent shock.
3. Remove all wires from motor terminals.
4. Read resistance between all pairs of terminals using an ohmmeter
on 0-10 ohm scale.
5. Determine 2 terminals that provide greatest resistance reading.
Through elimination, remaining terminal must be common (C). Greatest
resistance between common (C) and another terminal indicates the start
winding because it has more turns. This terminal is the start (S). The
remaining terminal will be run winding (R).
NOTE:
If compressor is hot, allow time to cool and internal line break
to reset. There is an internal line break protector which must be closed.
All compressors are equipped with internal motor protection. If motor
becomes hot for any reason, protector opens. Compressor should always
be allowed to cool and protector to close before troubleshooting. Always
turn off all power to unit and disconnect leads at compressor terminals
before taking readings.
Most common motor failures are due to either an open, grounded, or
short circuit. When a compressor fails to start or run, 3 tests can help
determine the problem. First, all possible external causes should be
eliminated, such as overloads, improper voltage, pressure equalization,
defective capacitor(s), relays, wiring, etc. Compressor has internal line
break overload, so be certain it is closed.
WARNING
!
ELECTRICAL SHOCK HAZARD
Failure to follow this warning could result in personal injury or death.
Do not supply power to unit with compressor terminal box cover
removed.
WARNING
!
ELECTRICAL SHOCK HAZARD
Failure to follow this warning could result in personal injury or death.
Exercise extreme caution when reading compressor currents when
high-voltage power is on. Correct any of the problems described below
before installing and running a replacement compressor.