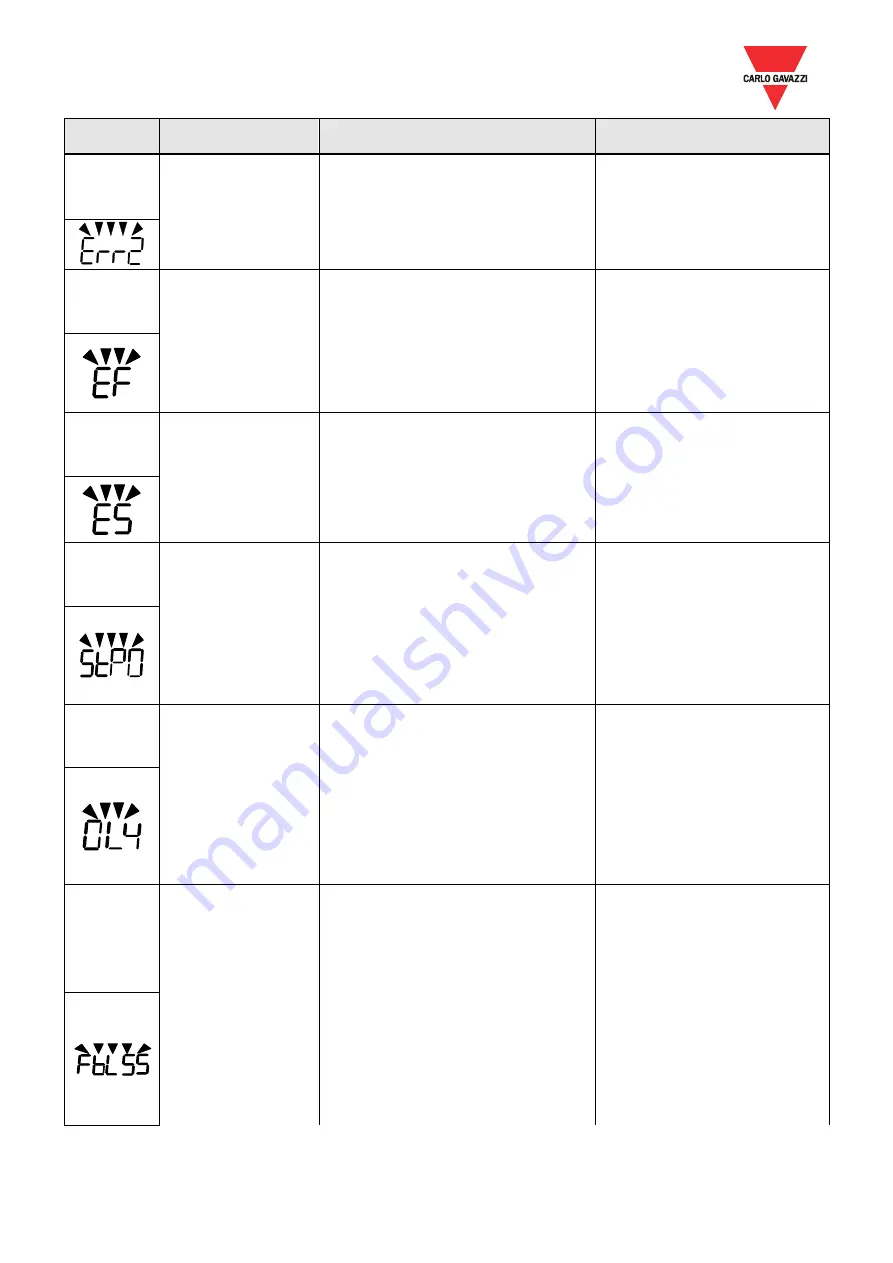
Motor Controllers AC Variable Frequency Drives
Type Variflex
3
RVFF
Specifications are subjected to change without notice.
81
LED
display
Description
Cause
Possible solutions
Password
Setting
Error
Password input at the
second
time
is
different from that at
the first time when the
password
lock
function enables.
•
Password input at the second time
is different from that at the first time
when the password lock function
enables.
•
Password input at the second
time is the same as that at
the first time when the
password lock function
enables.
Repeat
Run
Command
The inverter is only
allowed
unidirectional
operation and cannot
operate in reverse
direction
simultaneously.
•
Check if the external terminal is
given a run command in reverse
direction.
•
Cancel the run command in
reverse direction from the
external terminal.
External
Emergency
Stop
Function of external
emergency stop
starts.
•
Parameter 03-00~03-08 is set to 14
(Function of emergency stop is
enabled.)
•
Remove & shutdown the run
command of external
emergency stop and reset it
to multi-function digital input.
Zero Speed
Stop
Warning
The operation signal
is enabled but
frequency command
is lower than the
minimum output
frequency (01-08)
and DC brake is
disabled.
•
The frequency command is not set
up.
•
Set up the frequency
command.
Overload of
Air
Compressor
If
the
inverter
’
s
output
current
reaches OL4 current
level (23-69), OL4
Delay Time (23-70)
passed. When the
count is reached, the
inverter
will
automatically
decelerate to stop
and
displays
a
warning signal.
•
Since the current level (23- 69) is
set to be over low, the inverter’s
output current is higher than the
standard one or compressor’s
current is used to be over high.
•
Check if the compressor load
used is higher than the
standard one.
PID
feedback
signal loss
When 23-19 > 0, the
inverter will according
to feedback pressure
is less than (pressure
transmitter maximum
pressure (23-03) x
proportion
of loss
pressure
detection
(23-19)) value, if the
pressure
loss
detection time (23-
18) passed and 23-78
= 1 (loss of pressure
detection
function)
will
jump
warning
signal
•
23-19 proportion of loss pressure
detection is too big
•
Feedback sensor install failure or
not work normal.
•
Check 23-19 setting.
•
Make sure correct installation
and PID feedback signal.