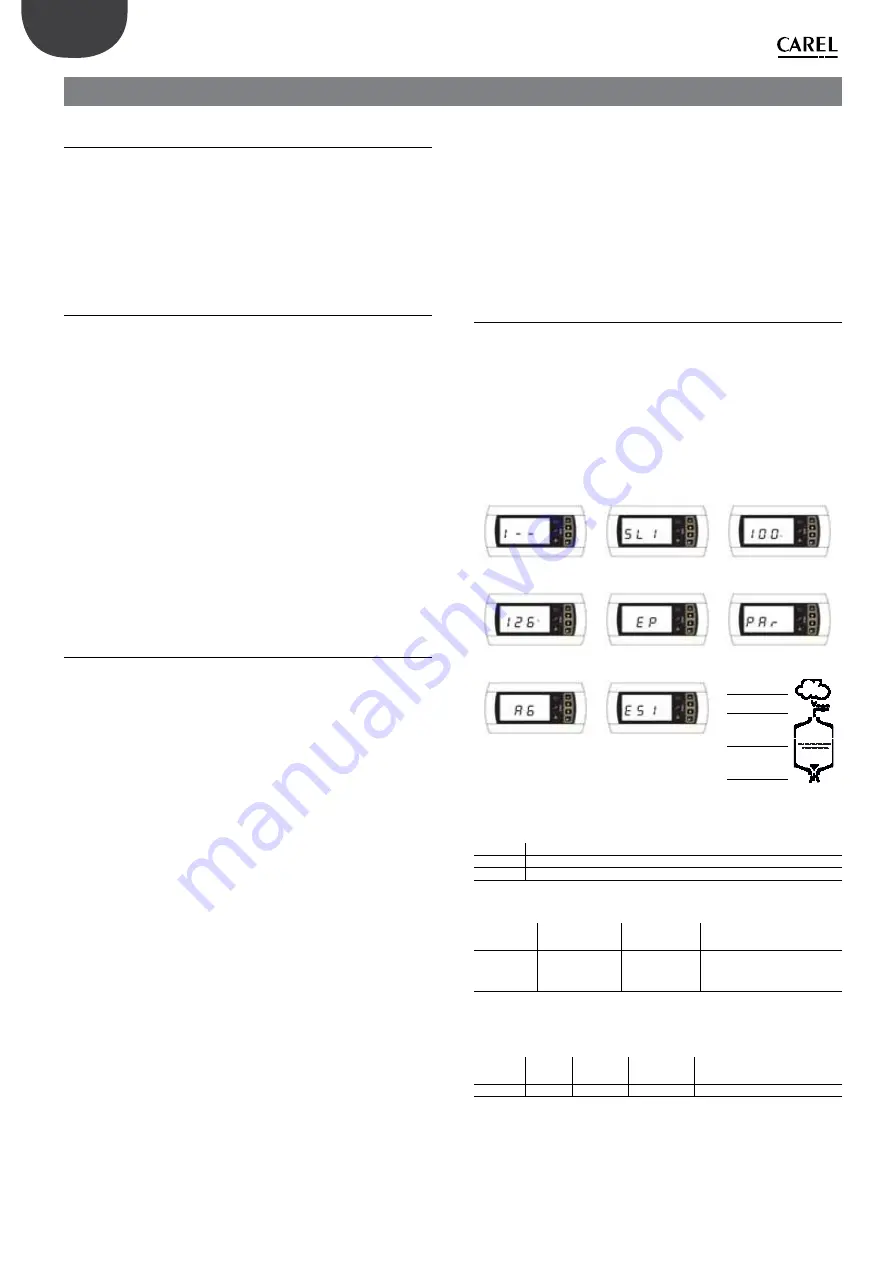
32
ENG
“Ultrasound for fancoil” +0300059IE - rel. 1.5 - 15.07.2019
14. NETWORK CONNECTION
14.1 Settings
The Master unit can control the operation of up to 3 Slave units connected
via tLAN network. For the electrical connections see the wiring diagram
on the next page. Dipswitches 1-3 on the Master unit must all be set to
OFF. Each Slave unit must be suitably confi gured using the dipswitches,
as follows:
1: Set ON for serial port (M11) conversion from RS485 to tLAN;
2/3: Slave address, as in the fi gure below.
14.2 Control logic
The Master unit controls each connected Slave unit via the following
parameters:
•
enable/disable operation;
•
level of atomised water production.
The control signals (probe/humidistat/external controller) are only read
and managed by the Master unit, which then controls operation of the
Slaves. The level of production on the Master unit is sent to all the Slaves:
Ex.1:
Master confi gured for proportional control (see chap. “Electrical
connections”) and request at 90%: the Master and each Slave will
modulate at 90% capacity (see chap. “Operating principles”).
Ex.2:
Master confi gured for control by room probe, set point 50 %rH:
when reaching the set point, the Master and all the Slaves will stop
atomised water production.
Each unit (Master or Slave) is independent as regards the atomised water
production control logic and all the other functions.
14.3 Management of Slaves from terminal
(Master)
From the main screen press PRG for 3 seconds and enter the password:
90. The terminal will display the status of the Slave connected, with the
following logic - starting from the digit on the left:
Unit 1, Unit 2, Unit 3.
The symbol 1 means “unit online”, while the symbol
means “unit offl
ine”.
Fig.1 shows an example of Unit 1 online (left digit 1) while Unit 2 and 3
offl
ine (central and right digit
).
Press ENTER on the terminal opens the menu for selecting the unit to be
controlled, using UP and DOWN to select the desired unit.
Fig.2 shows
the screen for selecting Unit 1.
Pressing ENTER accesses the menu for controlling the desired unit, UP
and DOWN scroll the following fi elds:
•
Percentage request sent to the Master
(Fig.3).
•
Operating hour counter
(Fig.4), resettable pressing UP+DOWN for 5
seconds (see “parameter d3”).
•
Unit alarms (
Fig.5, -- means no alarms are present), resettable pressing
UP+DOWN for 5 seconds.
•
humidifi er status (Enb = enabled): pressing ENTER disables the
humidifi er and dIS is shown on the main screen; to enable the unit
press ENTER again;
•
limit probe set point and proportional band (SL, bL), if enabled by
setting bH=1, parameter bH available in the list of parameters Par
•
Access parameter confi guration menu
(Fig.6).
The icons, in this display, indicate the status of the selected Slave
(Fig.9)
Pressing ENTER from parameter confi guration menu access screen opens
the list of parameters that can be set
(Fig.7).
For the meaning of the parameters see Confi guration parameters.
Parameter b8 is used as a timeout for recognising when a unit is offl
ine;
depending on the number of slaves connected, it may be necessary to
change this parameter, set by default to 10 s.
A
larms
From the main screen the Master displays any alarms present on a certain
slave with the code ESX, where X is the address of the slave with the
active alarm (Fig. 8, Slave 1 alarm).
For details of the current alarm access the menu for the slave in question.
Each unit is independent in managing its own alarms, except for those
relating to the control signals connected to the Master, which aff ect the
entire network of humidifi ers (see Tab.14.a).
14.4 Control via supervisor (Carel/Modbus®)
Supervisor variables I62 and I63 (Modbus® 189 and 190) can be used to
display and set the slave parameters. Variable I62 (Modbus 189) must be
written as shown in Tab. 14.b.
To read the variable, the value will be saved for variable I63 (Modbus 190)
after writing I62, while to write the variable, the value written will then be
available for variable I63.
E.g.: write parameter P0 for Slave 2 to 70
•
Write I63 to 70
•
Write I62 to 50224 (see the example in Tab. 14.b).
Fig. 1
Fig. 2
Fig. 3
Fig. 4
Fig. 5
Fig. 6
Production
Fill
Water presence
Drain
Fig. 7
Fig. 8
Fig. 9
Code
Description
PU
External control signal not connected
OFL
Supervisor disconnected and Master in request from serial mode
Tab. 14.d
Bit 15 Mode Bit 13-14 Slave
address
Bit 8-12
Variable type
Bit 0-7
CAREL supervisor address
0=Read
1=Write
01 = Slave 1
10 = Slave 2
11 = Slave 3
00100=Int.
01000=Analog
10000=Dig
E.g.: 0000 1000=8
Tab. 14.e
Example:
Write
Slave 2
Integer
variable
P0=
address 48
1
10
00100
00110000
=1100010000110000=50224