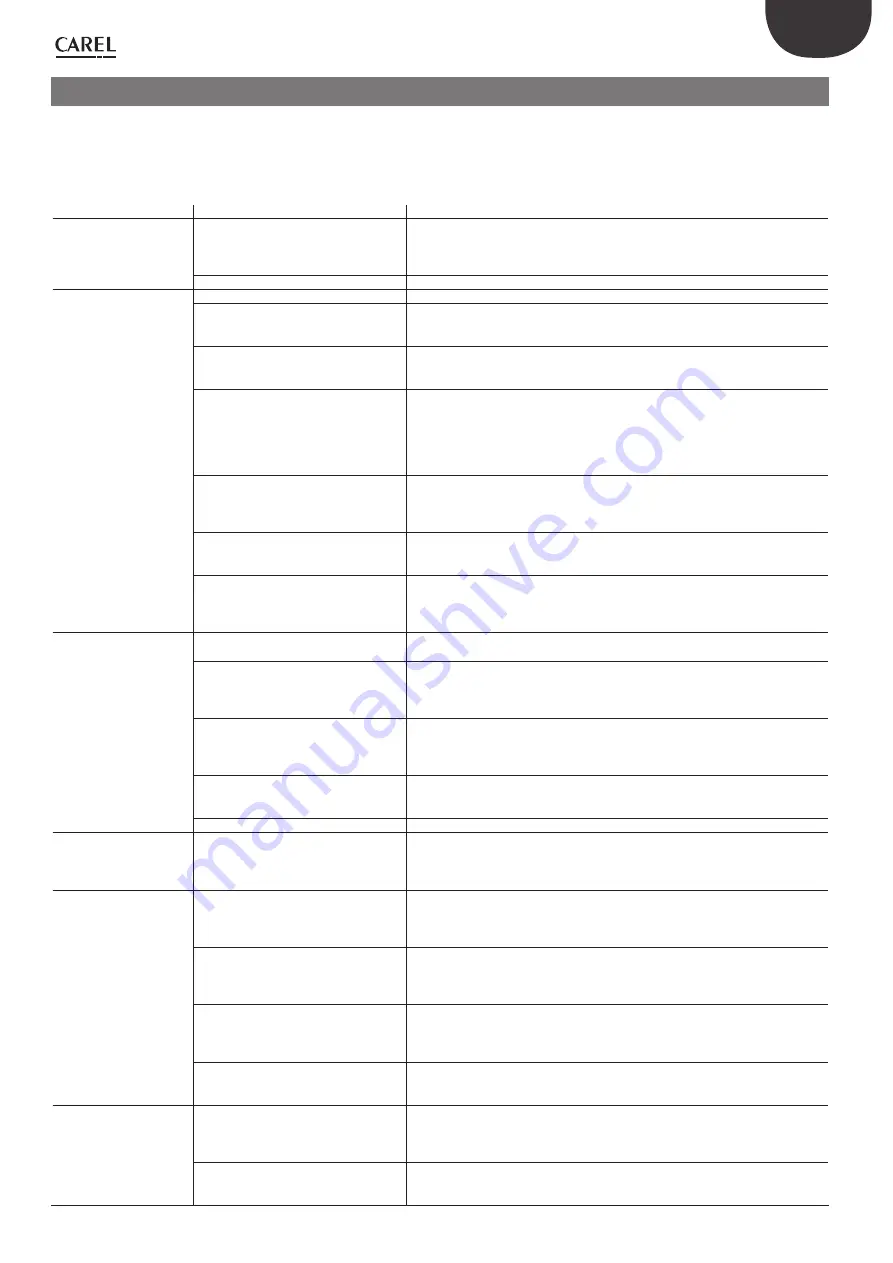
41
ENG
“EVD evolution” +030222041 - rel. 1.0 - 01.06.2008
TROUBLEShOOTING
10.
The following table lists a series of possible malfunctions that may occur
when starting and operating the driver and the electronic valve. These
cover the most common problems and are provided with the aim of
offering an initial response for resolving the problem.
PROBLEM
CAUSE
SOLUTION
The superheat value measu-
red is incorrect
The probe does not measure correct values Check that the pressure and the temperature measured are correct and that the probe
position is correct. Check that the minimum and maximum pressure parameters for the
pressure transducer set on the driver correspond to the range of the pressure probe
installed. Check the correct probe electrical connections.
The type of refrigerant set is incorrect
Check and correct the type of refrigerant parameter.
Liquid returns to the com-
pressor during control
The type of valve set is incorrect
Check and correct the type of valve parameter.
The valve is connected incorrectly (rotates
in reverse) and is open
Check the movement of the valve by placing it in manual control and closing or ope-
ning it completely. One complete opening must bring a decrease in the superheat and
vice-versa. If the movement is reversed, check the electrical connections.
The superheat set point is too low
Increase the superheat set point. Initially set it to 12 °C and check that there is no
longer return of liquid. Then gradually reduce the set point, always making sure there is
no return of liquid.
Low superheat protection ineffective
If the superheat remains low for too long with the valve that is slow to close, increase
the low superheat threshold and/or decrease the low superheat integration time.
Initially set the threshold 3 °C below the superheat set point, with an integration time
of 3-4 seconds. Then gradually lower the low superheat threshold and increase the low
superheat integration time, checking that there is no return of liquid in any operating
conditions.
Stator broken or connected incorrectly
Disconnect the stator from the valve and the cable and measure the resistance of the
windings using an ordinary tester.
The resistance of both should be around 36 ohms. Otherwise replace the stator. Finally,
check the electrical connections of the cable to the driver.
Valve stuck open
Check if the superheating is always low (<2 °C) with the valve position permanently at
0 steps. If so, set the valve to manual control and close it completely. If the superheat is
always low, check the electrical connections and/or replace the valve.
The “valve opening at start” parameter
is too high on many cabinets in which
the control set point is often reached (for
multiplexed cabinets only)
Decrease the value of the “Valve opening at start” parameter on all the utilities, making
sure that there are no repercussions on the control temperature.
Liquid returns to the com-
pressor only after defrosting
(for multiplexed cabinets
only)
The pause in control after defrosting is too
short
Increase the value of the “valve control delay after defrosting” parameter.
The superheat temperature measured
by the driver after defrosting and before
reaching operating conditions is very low
for a few minutes
Check that the LowSH threshold is greater than the superheat value measured and that
the corresponding protection is activated (integration time >0 s). If necessary, decrease
the value of the integration time.
The superheat temperature measured by
the driver does not reach low values, but
there is still return of liquid to the compres-
sor rack
Set more reactive parameters to bring forward the closing of the valve: increase the
proportional factor to 30, increase the integration time to 250 s and increase the deri-
vative time to 10 sec.
Many cabinets defrosting at the same time Stagger the start defrost times. If this is not possible, if the conditions in the previous
two points are not present, increase the superheat set point and the LowSH thresholds
by at least 2 °C on the cabinets involved.
The valve is significantly oversized
Replace the valve with a smaller equivalent.
Liquid returns to the com-
pressor only when starting
the controller (after being
OFF)
The “valve opening at start” parameter is
set too high
Check the calculation in reference to the ratio between the rated cooling capacity of
the evaporator and the capacity of the valve; if necessary, lower the value.
The superheat value swings
around the set point with an
amplitude greater than 4°C
The condensing pressure swings
Check the controller condenser settings, giving the parameters “blander” values (e.g.
increase the proportional band or increase the integration time). Note: the required sta-
bility involves a variation /- 0.5 bars. If this is not effective or the settings cannot
be changed, adopt electronic valve control parameters for perturbed systems
The superheat swings even with the valve
set in manual control (in the position cor-
responding to the average of the working
values)
Check for the causes of the swings (e.g. low refrigerant charge) and resolve where pos-
sible. If not possible, adopt electronic valve control parameters for perturbed systems.
The superheat does NOT swing with the
valve set in manual control (in the position
corresponding to the average of the
working values)
As a first approach , decrease (by 30 to 50 %) the proportional factor. Subsequently try
increasing the integration time by the same percentage. In any case, adopt parameter
settings recommended for stable systems.
The superheat set point is too low
Increase the superheat set point and check that the swings are reduced or disappear.
Initially set 13 °C, then gradually reduce the set point, making sure the system does not
start swinging again and that the unit temperature reaches the control set point.
In the start-up phase with
high evaporator tempe-
ratures, the evaporation
pressure is high
MOP protection disabled or ineffective
Activate the MOP protection by setting the threshold to the required saturated eva-
poration temperature (high evaporation temperature limit for the compressors) and
setting the MOP integration time to a value above 0 (recommended 4 seconds). To
make the protection more reactive, decrease the MOP integration time.
Refrigerant charge excessive for the system
or extreme transitory conditions at start-up
(for cabinets only).
Apply a “soft start” technique, activating the utilities one at a time or in small groups. If
this is not possible, decrease the values of the MOP thresholds on all the utilities.