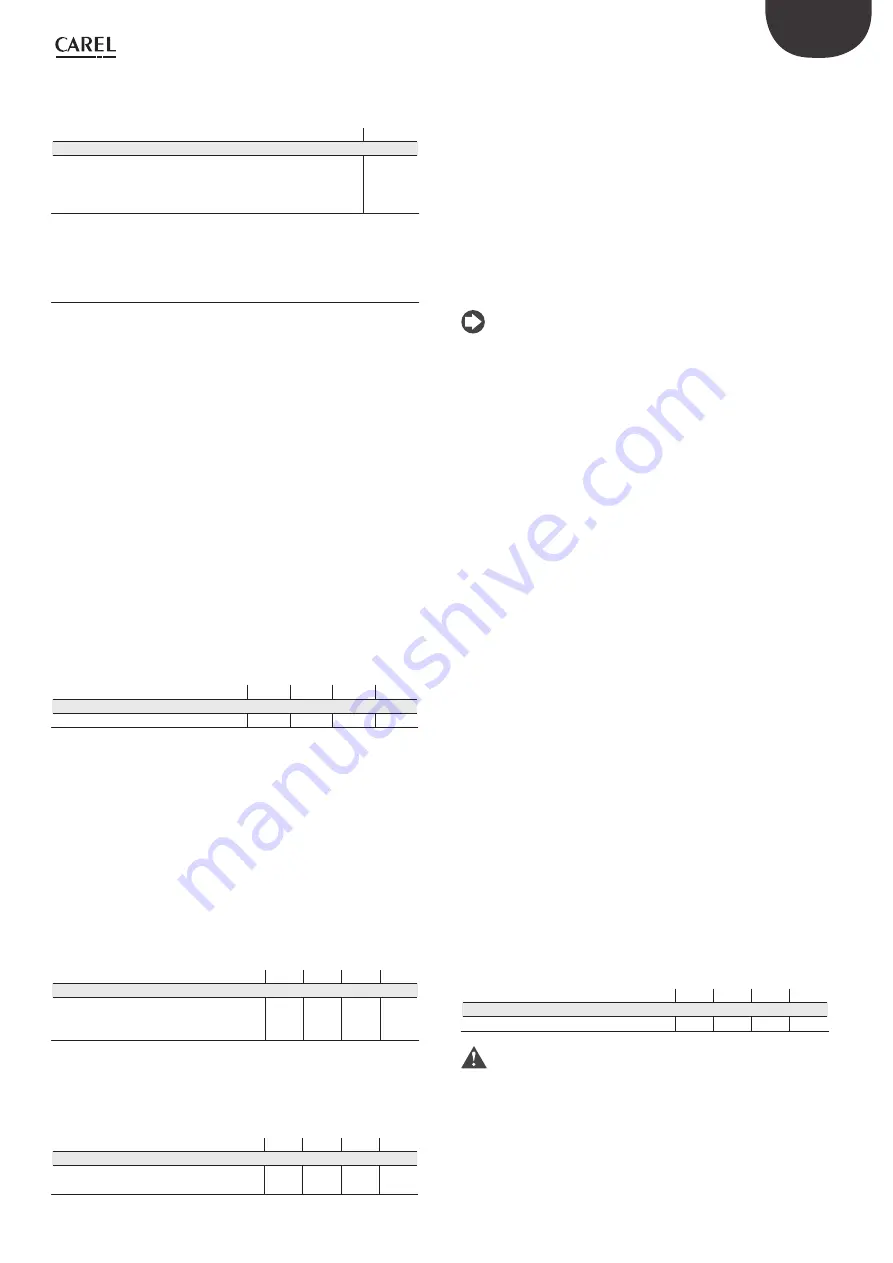
25
ENG
“EVD evolution” +030222041 - rel. 1.0 - 01.06.2008
Output
The relay output can be configured to control the solenoid valve or as an
alarm relay output. See the chapter on “Alarms”.
Parameter/description
Def.
Configuration
Relay configuration:
Disabled; Alarm relay (open when alarm active); Solenoid valve
relay (open in standby); Valve relay +alarm (open in standby
and control alarms)
Alarm
relay
Tab. 6.f
Control status
6.2
The electronic valve driver has 6 different types of control status, each
of which may correspond to a specific phase in the operation of the
refrigeration unit and a certain status of the driver-valve system.
The status may be as follows:
forced closing:
•
initialisation of the valve position when switching the
instrument on;
standby:
•
no temperature control, unit OFF;
wait:
•
opening of the valve before starting control, also called pre-
positioning, when powering the unit and in the delay after defrosting;
control:
•
effective control of the electronic valve, unit ON;
positioning:
•
step-change in the valve position, corresponding to the
start of control when the cooling capacity of the controlled unit varies
(only for pLAN EVD connected to a pCO);
stop:
•
end of control with the closing of the valve, corresponds to the
end of temperature control of the refrigeration unit, unit OFF.
Forced closing
Forced closing is performed after the driver is powered-up and
corresponds to a number of closing steps equal to the parameter “Closing
steps”, based on the type valve selected. This is used to realign the valve
to the physical position corresponding to completely closed. The driver
and the valve are then ready for control and both aligned at 0 (zero). On
power-up, first a forced closing is performed, and then the standby phase
starts.
Parametro/description
Def.
Min.
Max.
UOM
Valve
EEV closing steps
500
0
9999
step
Tab. 6.g
Standby
Standby corresponds to a situation of rest in which no signals are received
to control the electronic valve. This normally occurs:
when the refrigeration unit stops operating, either when switched
•
off manually (e.g. from the button, supervisor) or when reaching the
control set point;
during defrosts, except for those performed by reversing of the cycle
•
(or hot gas bypass).
In general, it can be said that the electronic valve driver is in standby
when the compressor stops or the control solenoid valve closes. The valve
is closed or open, delivering around 25% of the flow-rate of refrigerant,
based on the setting of the “valve open in standby” parameter.
In this phase, manual positioning can be activated.
Parameter/description
Def.
Min.
Max.
UOM
Valve open in standby
0=disabled=valve closed;
1=enabled = valve open 25%
0
0
1
-
Tab. 6.h
Pre-positioning/start control
If during standby a control request is received, before starting control the
valve is moved to a precise initial position.
Parameter/description
Def.
Min.
Max.
UOM
Control
Valve opening at start (evaporator/valve
capacity ratio)
50
0
100
%
Tab. 6.i
This parameter should be set based on the ratio between the rated
cooling capacity of the evaporator and the valve (e.g. rated evaporator
cooling capacity: 3kW, rated valve cooling capacity: 10kW, valve opening
= 3/10 = 33%).
If the capacity request is 100%:
Opening (%)= (Valve opening at start-up);
If the capacity request is less than 100% (capacity control):
Opening (%)= (Valve opening at start-up) · (Current unit cooling
capacity),
where the current unit cooling capacity is sent to the driver via pLAN
by the pCO controller. If the driver is stand-alone, this is always equal to
100%.
Note:
this procedure is used to anticipate the movement and bring the valve
•
significantly closer to the operating position in the phases immediately
after the unit starts;
if there are problems with liquid return after the refrigeration unit starts
•
or in units that frequently switch on-off, the valve opening at start-up
must be decreased. If there are problems with low pressure after the
refrigeration unit starts, the valve opening must be increased.
Wait
When the calculated position has been reached, regardless of the
time taken (this varies according to the type of valve and the objective
position), there is a constant 5 second delay before the actual control
phase starts. This is to create a reasonable interval between standby, in
which the variables have no meaning, as there is no flow of refrigerant,
and the effective control phase.
Control
The control request can be received by the closing of digital input 1 or
via the network (pLAN). The solenoid or the compressor are activated
when the valve, following the pre-positioning procedure, has reached
the calculated position. The following figure represents the sequence of
events for starting control of the refrigeration unit.
Control delay after defrost
Some types of refrigerating cabinets have problems controlling the
electronic valve in the operating phase after defrost. In this period (10 to
20 min after defrosting), the superheat measurement may be altered by
the high temperature of the copper pipes and the air, causing excessive
opening of the electronic valve for extended periods, in which there is
return of liquid to the compressors that is not detected by the sensors
connected to the driver. In addition, the accumulation of refrigerant in
the evaporator in this phase is difficult to dissipate in a short time, even
after the sensors have started to correctly measure the presence of liquid
(superheat value low or null).
The driver can receive information on the defrost phase in progress, via
digital input 2. The “Start delay after defrost” parameter is used to set a
delay when control resumes so as to overcome this problem. During
this delay, the valve will remain in the pre-positioning point, while all the
normal sensor alarms procedures, etc. managed.
Parameter/description
Def.
Min.
Max.
UOM
Control
Start delay after defrost
10
0
60
min
Tab. 6.j
Important:
if the superheat temperature should fall below the set
point, control resumes even if the delay has not yet elapsed.