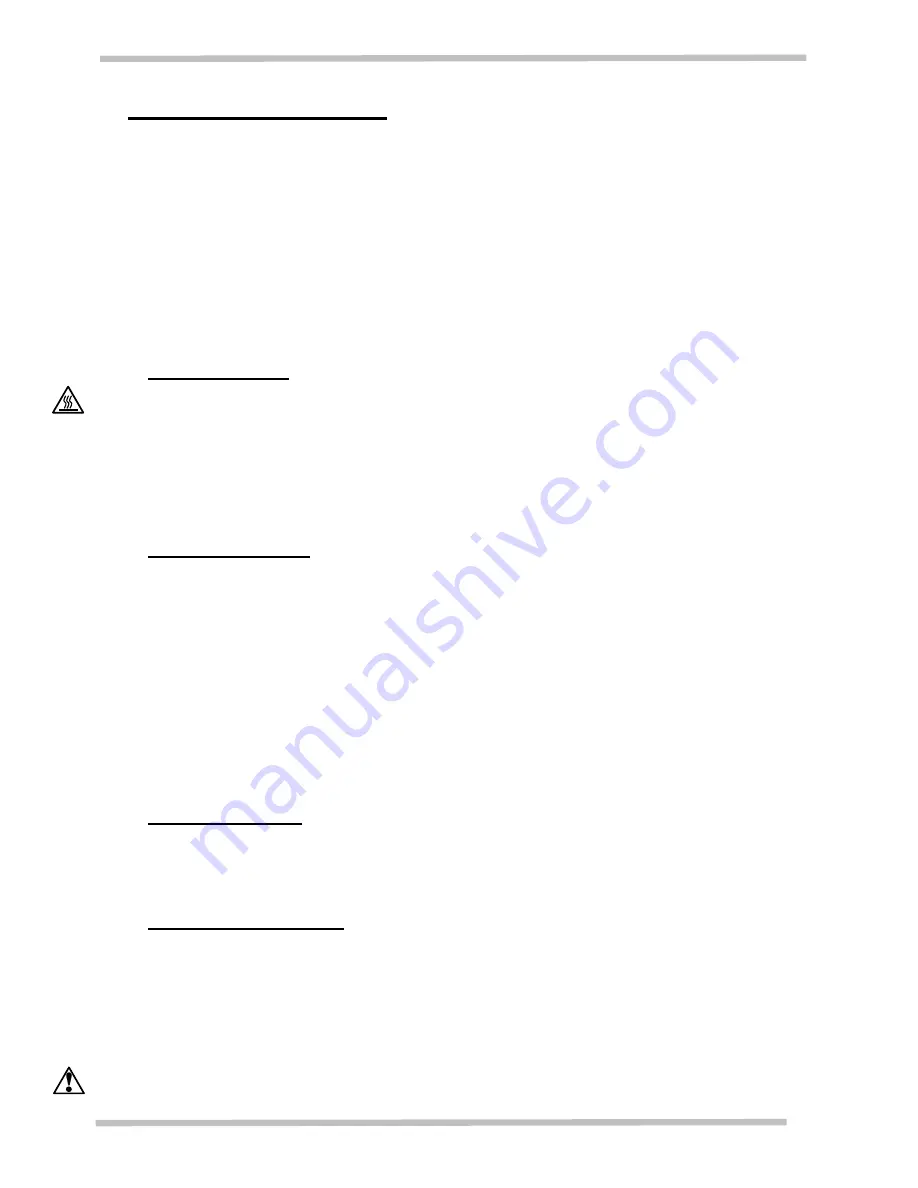
MRF 16/22
14
MF 55-GB 1.21
4 General operating notes
This manual explains how to operate and maintain the MRF 16/22.
Heating element life is shortened by use at temperatures close to maximum, so avoid leaving
the furnace at high temperatures when not required. The furnace can be cycled between room
temperature and maximum without a detrimental effect on element life. The maximum
temperature is 1600°C.
Operating the furnace below 600°C for long periods may cause pesting of the elements. See
section 12.6.
Insulation life will be shortened if heat up rates are used in excess of 500°C/hr (8.33°C/min)
up to 1200°C and 300°C/hr (5°C/min) from 1200°C up to 1600°C.
4.1
Opening the door
Take great care when loading or unloading the furnace chamber. Also read the safety
precautions in sections 2.3 and 2.4.
•
At all times operate the door gently to avoid mechanical shock. The heating elements and
the insulation are very susceptible to mechanical shock.
•
Opening the door when the furnace is very hot can cause hot air to be drawn towards the
thermal cut out and activate it
[See section 4.6].
4.2
Loading the furnace
When loading the furnace ensure that nothing is placed within 25mm of the elements, and
avoid shielding the thermocouple from the heating elements.
The thermocouple is designed to sense the temperature near the heating element, but if a
large object is placed in the chamber it may record the average temperature of the object and
the elements, which can lead to overheating of the elements. Allow large objects to gain heat
at a lower temperature and then reset the controller to a temperature close to the desired
maximum.
Avoid placing large objects within 50mm of the back wall. The microwave power enters the
chamber at the centre of the back wall.
Take care that nothing touches the elements when loading or unloading.
4.3 Insulation
cracking
The insulation material is susceptible to surface cracking arising from high temperature cycling;
this is a normal occurrence and such cracking is not detrimental to the performance of the
furnace.
4.4
Thermocouples - ageing
Regular use at high temperatures will cause the thermocouples to deteriorate resulting in false
readings, this is known as ‘ageing’. This will cause the furnace to run at a higher temperature
than indicated.
Customers are advised periodically to check the thermocouple output, either by a calibration
test or by comparing the output with a new reference thermocouple at the required process
temperature.
Failure to check the thermocouple regularly may result in overheating of the work and the