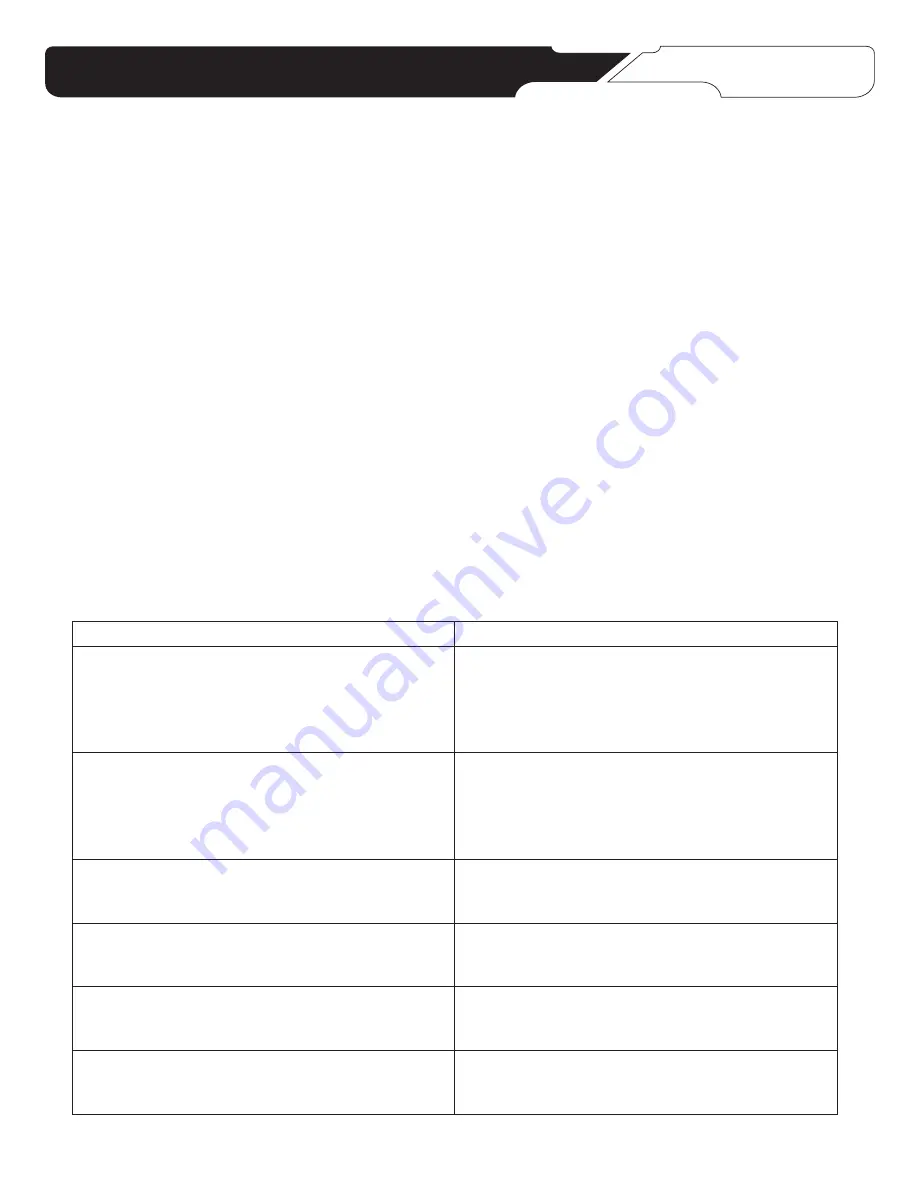
PROBLEM
SOLUTION
The motor will not start.
The band saw blade does not move although motor is running.
The blade will not cut or cuts slowly.
Sawdust fills inside the band saw.
Sawdust in motor housing.
Unable to get the blade to track in the driver of wheel.
1. Band saw is not plugged in.
2. A household circuit has blown a fuse or an open circuit breaker.
3. power cord is damaged. Replace.
4. Switch is not in the " ON" position.
5. Motor requires service.
1. Blade tension knob is not tight. Turn motor off, tighten knob and
restart the band saw.
2. Blade has slipped off pulley wheel. Open cover housing and
check.
3. Blade is broken. Replace.
1. Contact has dulled teeth with hardened steels or long usage.
Replace.
2. Blade mounted backwards.
1. This is normal, clean out periodically.
2. Remove cover housing. Use vacuum cleaner to remove dust.
1. Use a vacuum cleaner nozzle on air intake and exhaust grilles.
2. Keep workplace cleaner. Clean up excess sawdust frequently.
1. Backing bearing is not properly adjusted.
2. Tension wheel is not properly adjusted.
3. Bad blade, replace.
9. MAINTENANCE & TROUBLESHOOTING
p.
2
WARNING:
For your own safety, turn the switch " OFF" and remove plug of the power source before
maintaining your bandsaw.
TIRES
Pitch and sawdust that build up on the tires should be removed with a stiff brush or scarpe the sawdust with a
piece of wood.
NOTE:
To reduce the risk of damaging the tires, do not use a sharp knife or any kind of solvent.
When the tire becomes worn, they should be replaced. When replacing the tires, stretch them around the
wheels but do not glue them on.
GENERAL MAINTENANCE
Keep your band saw clean. Remove the sawdust from the inside. Vacuum or blow out frequently.
Do not allow residue to build up on the table, the guides or the back-up bearings. Clean them with gum and
pitch remover.
Note:
Do not immerse the back-up bearings in the gum and pitch remover. Put a thin coat of paste wax on the
table so that wood slides easily while cutting.
MOTOR
Frequently blow or vacuum out the sawdust from the motor.
CAUTION:
To reduce the risk of eye injury from blowing debris, wear safety glasses when blowing out dust.
LUBRICATION
All of the bearing are packed with grease at the factory. They require no further lubrication.
Summary of Contents for SBW-6300
Page 1: ...XM000557 BELAUC...
Page 16: ...S...
Page 23: ...p 23 MODEL NO 24 Inch Band Saw PART NO AB136464T UPPER WHEEL ASM...
Page 24: ...p 24 MODEL NO 24 Inch Band Saw PART NO AB136463T LOWER WHEEL ASM...
Page 25: ...p 25 MODEL NO 24 Inch Band Saw PART NO AB136421 TRUNNION BLOCK ASM...
Page 27: ...p 27 MODEL NO 24 Inch Band Saw PART NO AB136488 FENCE SET...
Page 28: ...p 28 MODEL NO 24 Inch Band Saw PART NO AB136508 LOWER BALL BEARING GUIDE ASM...
Page 29: ...p 29 MODEL NO 24 Inch Band Saw PART NO AB136550 UPPER GUIDE BAR ASM...
Page 30: ...p 30 MODEL NO 24 Inch Band Saw PART NO AB136564 UPPER BALL BEARING GUIDE ASM...
Page 31: ...p 31 MODEL NO 24 Inch Band Saw PART NO AB198110 MITER GAUGE ASM...