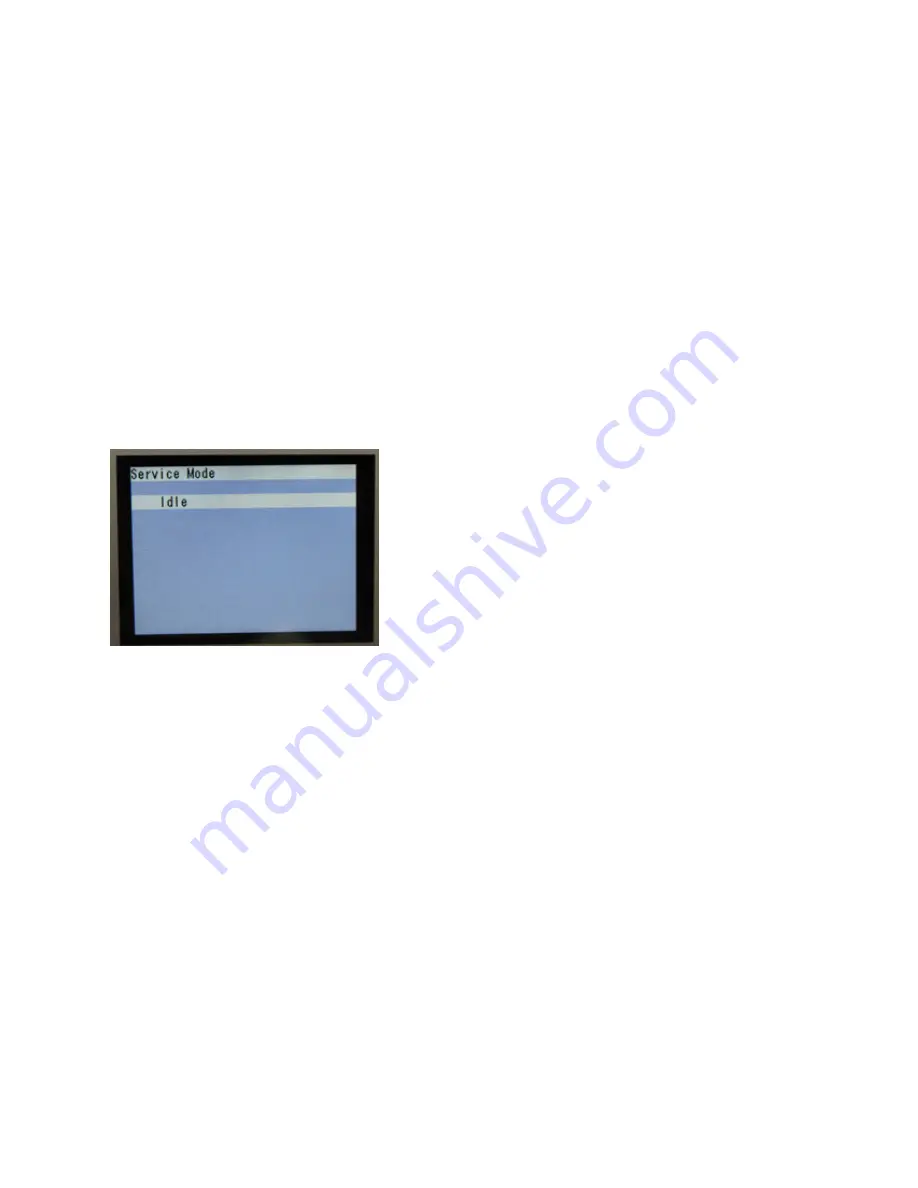
4-2. Service Mode
(1) Service mode operation procedures
Use the Service Tool on the connected computer.
1) Start the machine in the service mode.
i. With the machine power turned off, while pressing the Stop button, press and hold the ON button. (DO
NOT release the buttons.)
ii. When the Power LED lights in green, while holding the ON button, release the Stop button.
(DO NOT release the ON button.)
iii. While holding the ON button, press the Stop button 2 times, and then release both the ON and
Stop buttons. (Each time the Stop button is pressed, the Alarm and Power LEDs light
alternately, Alarm in orange and Power in green, starting with Alarm LED.)
iv. When the Power LED lights in green and the machine displays "Service Mode Idle," the
machine is ready for the service mode operation.
LCD ready for the service mode operation:
2) Start the Service Tool on the connected computer.
i. When a button is clicked in the Service Tool dialog box, that function is performed. During operation
of the selected function, all the Service Tool buttons are dimmed and inactive.
ii. When the operation is completed, "A function was finished." is displayed, and another function
can be selected.
iii. If a non-supported function is selected, "Error!" is displayed. Click
OK
in the error message
dialog box to exit the error.
47 / 64
Summary of Contents for MP560 - PIXMA Color Inkjet
Page 8: ...5 64 ...
Page 33: ... Remove 4 screws then the operation panel board Remove a set of buttons 30 64 ...
Page 51: ... 2 Service Tool functions Service Tool screen Version 1 05 48 64 ...
Page 59: ...56 64 ...
Page 64: ... 2 Service test print Service test print sample MP550 First page 61 64 ...
Page 65: ... Second page 62 64 ...
Page 66: ... 3 Ink absorber counter value print Print sample 4 5 Verification Items 63 64 ...