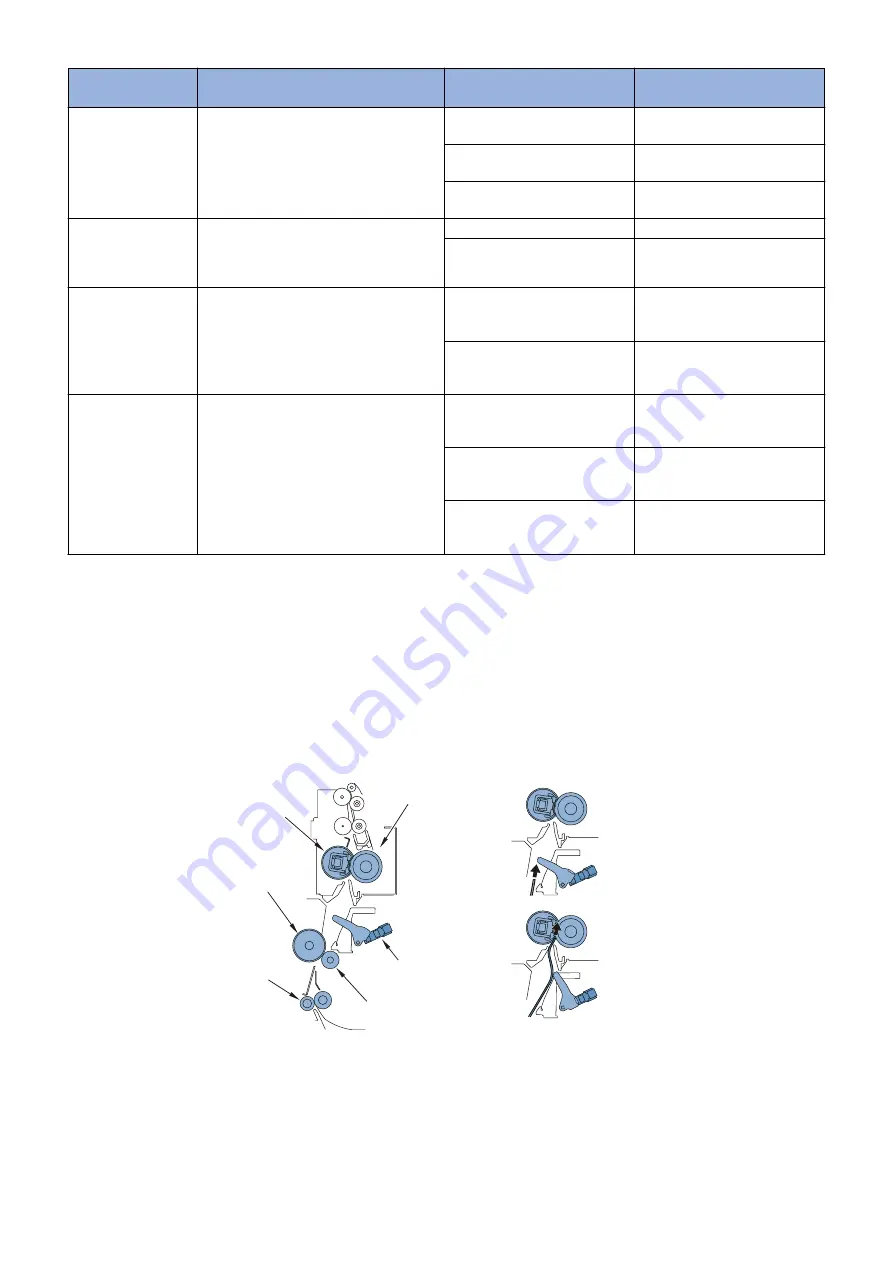
User mode
Summary
Setting value
Temperature control/produc-
tivity
Special Mode P (To
prevent a curl of thin
paper/ recycle paper)
The fixing mode is changed when either of
the plain/ recycled/ color/ 3-hole paper is
selected in the control panel. The produc-
tivity is reduced and fixing grade is im-
proved.
Off (Default)
Normal temperature control
(Plain paper mode)
Medium (Fixing grade is im-
proved)
Thin paper mode temperature
control
High (Fixing grade is improved) S-thin paper mode temperature
control
Special Mode G (To
increase the fixing
grade for heavy pa-
per)
The productivity is reduced and fixing grade
is improved.
Off (Default)
Normal control
On (Fixing grade is improved)
The productivity is reduced by 4
sheets or 5 sheets.
Special Mode G (To
increase the produc-
tivity during down se-
quence)
The down sequence time is reduced when
switching the paper size. The fixing grade
is reduced and productivity is improved.
(*3)
Off (Default)
Temperature difference between
the main and sub thermistors to
start the paper feeding: 20 deg C
On (Productivity is improved)
Temperature difference between
the main and sub thermistors to
start the paper feeding: 30 deg C
Special Mode F (To
reduce the wait time
during rotation/ colla-
tion adjustment
mode)
The down sequence time is reduced in the
collation adjustment mode. The fixing
grade is reduced and productivity is im-
proved.
Image Priority (Default)
Temperature difference between
the main and sub thermistors to
start the paper feeding: 20 deg C
Speed Priority 1 (Productivity is
improved)
Temperature difference between
the main and sub thermistors to
start the paper feeding: 40 deg C
Speed Priority 2 (Productivity is
improved more)
Temperature difference between
the main and sub thermistors to
start the paper feeding: 60 deg C
*1. N1 mode: "Normal temperature control" -24 deg C (when the cassette feeding, and the fixing temperature is 100 deg C or
more at the start of warm-up control.)
*2. N3 mode: "Normal temperature control" -48 deg C (when the cassette feeding, and the fixing temperature is 100 deg C or
more at the start of warm-up control.)
*3. The setting of rotation/collation mode is given priority to over this setting.
■ Paper loop amount control before fixing
Purpose:
• To get a proper image by avoiding a shock when the trailing edge of paper comes out of the registration roles, an appropriate
paper loop is formed between transfer roller and fixing roller.
Pressure roller
Fixing film
Drum
Loop sensor(S6)
Transfer roller
Registration
roller
Sensor: OFF
Sensor: ON
Starting conditions:
• This control is performed at every paper feeding.
Operation:
2. Technical Explanation
74
Summary of Contents for imageRUNNER 2520 Series
Page 1: ...Revision 9 0 imageRUNNER 2530 2525 2520 Series Service Manual ...
Page 62: ...No Part name 3 Laser unit 2 Technical Explanation 52 ...
Page 119: ...Periodical Service 3 Consumable Parts and Cleaning Parts 110 Cleaning Parts 115 ...
Page 125: ...Cleaning Parts Fixing guide Transfer guide 3 Periodical Service 115 ...
Page 136: ...List of Sensors S18 S17 S16 TS2 HU1 S9 S8 S19 TS1 S11 S12 4 Disassembly Assembly 126 ...
Page 165: ...5 Remove the idler gear 1 claw 1x 4 Disassembly Assembly 155 ...
Page 172: ... 1 4 2 3 2 2 Remove the scanner motor 4 screws 4x 4 Disassembly Assembly 162 ...
Page 186: ...3 Remove the RAM PCB Release the hook 4 Disassembly Assembly 176 ...
Page 187: ...Adjustment 5 Overview 178 Basic Adjustment 180 Adjustment when Replacing the Parts 182 ...
Page 209: ...Error Jam Alarm 7 Outline 200 Error Code 201 Jam Code 213 Alarm Code 219 ...
Page 231: ...Service Mode 8 Overview 222 Details of Service Mode 225 Remote UI Service Mode 302 ...
Page 314: ...Example of report display 8 Service Mode 304 ...
Page 387: ...APPENDICES Service Tools 378 General Circuit Diagram 379 ...