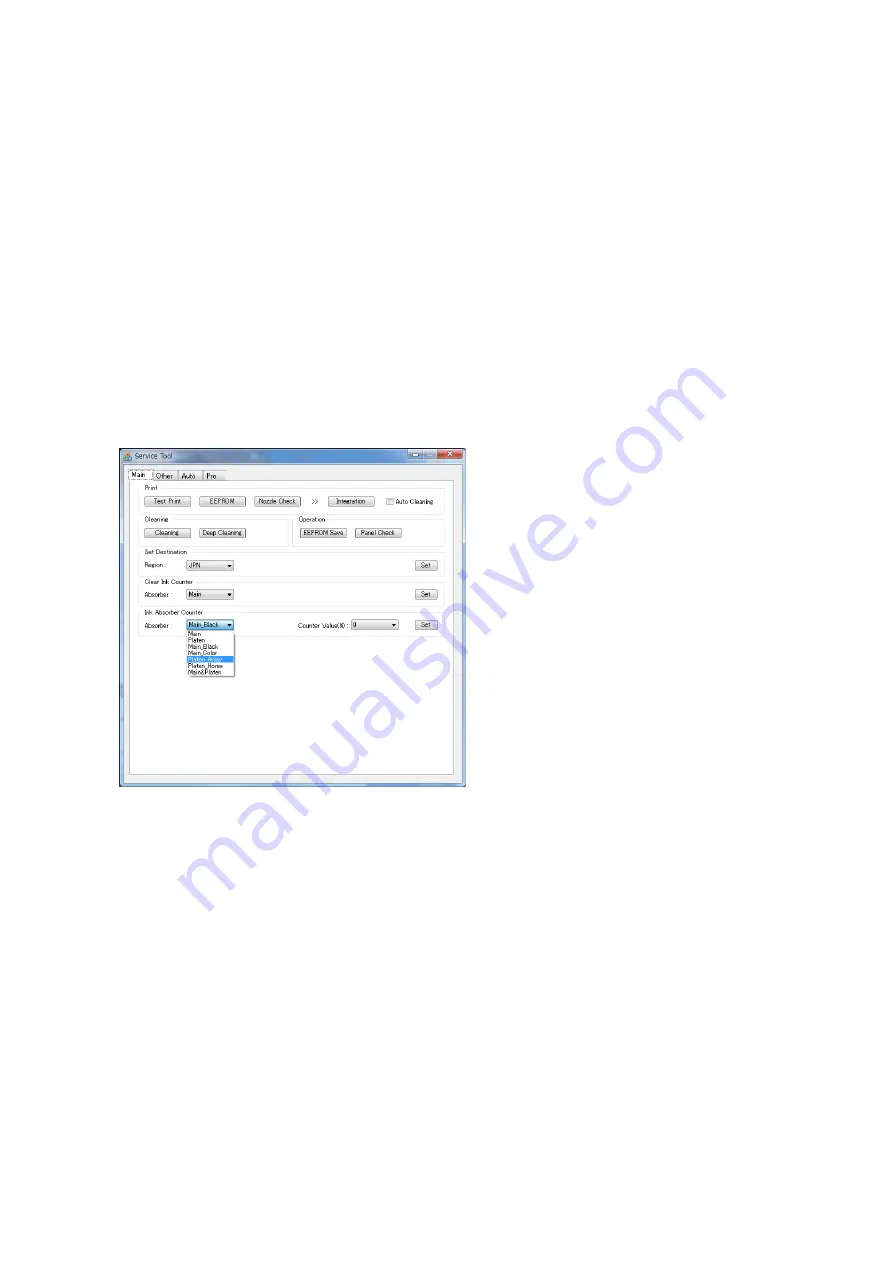
(54/80)
QY8-13EX-040
(4) Ink absorber counter setting
Set the ink absorber counter value to a new EEPROM after the main PCB ass’y is replaced in servicing.
1) Before replacement of the main PCB ass’y, check the ink absorber counter value in EEPROM
Information Print.
2) Replace the main PCB ass’y.
3) After replacement, the ink absorber counter value should be set in the service mode using the Service
Tool.
In the
Ink Absorber Counter
section of the Service Tool, select
Main
, from the
Absorber
pull-down
menu.
From the
Counter Value(%)
pull-down menu, select the value (in 10% increments) which is the
closest to the actual counter value confirmed before replacement of the main PCB ass’y, and click
Set
.
4) Print EEPROM information to confirm that the value is properly set to the EEPROM.
Set the ink absorber counter value to EEPROM after the ink absorber partial replacement.
1) Replace the Absorber Kit (Partial).
2) The ink absorber counter value should be set to 30% using the Service Tool.
In the
Ink Absorber Counter
section of the Service Tool, select
Main
, from the
Absorber
pull-down
menu.
From the
Counter Value(%)
pull-down menu, select
30
, and click
Set
.
easyfixs.blogspot.com
Summary of Contents for G2000 series
Page 43: ... 43 80 QY8 13EX 040 easyfixs blogspot com ...
Page 44: ...QY8 13EX 040 easyfixs blogspot com ...
Page 59: ... 59 80 QY8 13EX 040 2 8 9 7 6 9 5 easyfixs blogspot com ...
Page 76: ... 76 80 QY8 13EX 040 5 4 Main PCB Ass y Block Diagram 1 G1000 series easyfixs blogspot com ...
Page 77: ... 77 80 QY8 13EX 040 2 G2000 series easyfixs blogspot com ...
Page 78: ... 78 80 QY8 13EX 040 3 G3000 series easyfixs blogspot com ...