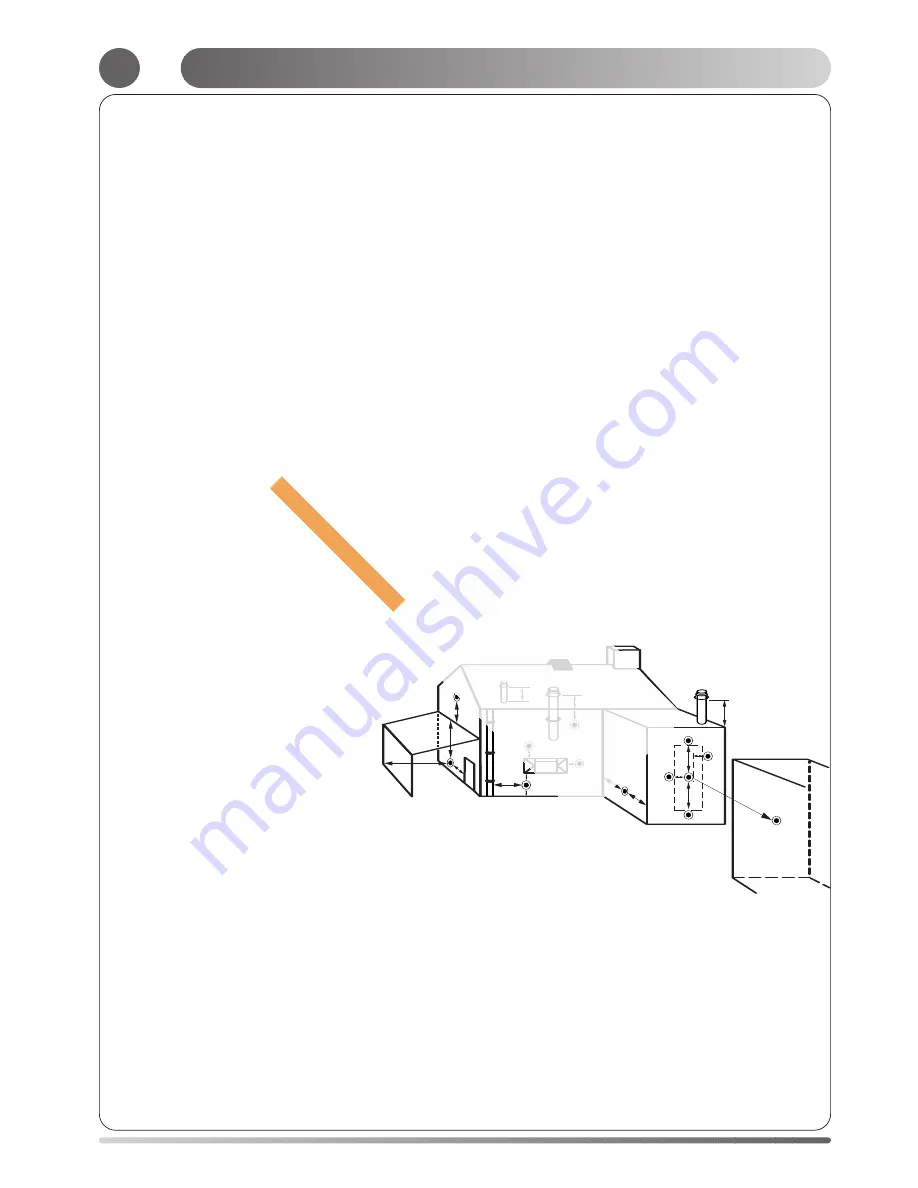
7
4
Location
The boiler can be installed on any suitable internal wall.
Provision must be made to allow the correct routing of the flue
and siting of the terminal to allow the safe and efficient
removal of the flue products. A compartment or cupboard may
be used provided that it has been purpose-built or modified for
the purpose. It is not necessary to provide permanent
ventilation for cooling purposes. Detailed recommendations
are given in BS 5440 pt 2. If it is proposed that it is installed in
a timber framed building then reference must be made to
British Gas Document DM2, or advice sought from CORGI.
Avoid to install the boiler where the air inlet can be polluted
by chemical products such as chlorine (swimming pool aera),
or ammonia (hair dresser), or alcalin products (launderette)
Flue
Detailed information on flue assembly is contained in the
appropriate starter pack.
The boiler must be installed so that the flue terminal is
exposed to the free passage of external air at all times. It must
not be allowed to discharge into another room or space such
as an outhouse or closed lean-to. The minimum acceptable
clearances are shown below:
- A Directly below an opening, window, etc
300 mm
- B Above an opening, window, etc
300 mm
- C Horizontally to an opening, window, etc
300 mm
- D Below gutters, soils pipes or drain pipes
75 mm
- E Below eaves
200 mm
- F Below balconies or car port roof
200 mm
- G From a vertical drain pipe or soil pipe
150 mm
- H From an internal or external corner
300 mm
- I Above ground roof or balcony level
300 mm
- J From a surface facing the terminal
600 mm
- K From a terminal facing the terminal
1200 mm
- L From an opening in the car port into the dwelling 1200 mm
- M Vertically from a terminal on the same wall
1500 mm
- N Horizontally from a terminal on the same wall
300 mm
- Q Fixed by Ubbink Rolux 4 GM flue terminal
It may be necessary to protect the terminal with a
guard. Reference should be made to the Building
Regulations for guidance. Suitable guards may be
obtained from the following manufacturer:
Quinnel Barret & Quinnel Wireworks
Old Kent Road
London SE15 1NL
Tel: 0171 639 1357
Ventilation
The room in which the boiler is installed does not require specific
ventilation. If it is installed in a cupboard or compartment
permanent ventilation is not required for cooling purposes.
Gas Supply
The gas installation and soundness testing must be in
accordance with the requirements of BS 6891.The boiler
requires a 22 mm supply. Ensure that the pipe size is
adequate for demand including other gas appliances on the
same supply.
Combustion system protection
The sulphur level contained in the gas should comply with
the européan Standards which are :
- maximum 150 mg/m3 for a short period in a year
- average level of 30 mg/m3 during one year
Electrical Supply
The appliance requires an earthed 230V - 50 Hz supply and
must be in accordance with current I.E.E. It must also be
possible to be able to completely isolate the appliance
electrically. Connection should be via a 3 amp fused double-
pole isolating switch with contact separation of at least 3 mm
on both poles. Alternatively, a fused 3 Amp. 3 pin plug and
unswitched socket may be used, provided it is not used in a
room containing a bath or shower. It should only supply the
appliance.
The boiler is suitable for sealed systems only. The maximum
working pressure for the appliance is 10 bar. All fittings and
pipework connected to the appliance should be of the same
standard. If there is a possibility of the incoming mains
pressure exceeding 10 bar, particularly at night, then a
suitable pressure limiting valve must be fitted.
The boiler is designed to provide hot water on demand to
multiple outlets within the property. If there is a requirement
for greater demands, for example if the property has several
bathrooms and cloakrooms, a vented or unvented hot water
storage system may be used.
Showers
Any shower valves used with the appliance should be of a
thermostatic or pressure balanced type. Refer to the shower
manufacturer for performance guidance and suitability.
Flushing and Water Treatment
The performance of the appliance could be impaired by
system debris or the effects of corrosion. The system must
be flushed thoroughly to remove metal filings, solder,
machining oils and other fluxes and greases before
connecting the boiler. If it is an existing system, an
appropriate flushing and descaling agent should be used.
Refer to BS 7593 (1992) for guidance. For more information
on the use of corrosion inhibitors, flushing and descaling
agents, advice can be sought from the manufacturers of
water treatment products such as:
Betz Dearborn Ltd
Foundry Lane
Widnes
Cheshire
WA8 8UD
Tel: 0151 424 5351
Fernox Manufacturing
Britannica Works
Clavering
Essex
CB11 4QZ
Tel: 01799 550811
System Controls
The boiler is electrically controlled and is suitable for most
modern electronic time and temperature controls. The
addition of such external controls can be beneficial to the
efficient operation of the system. The boiler connections for
external controls are 24V and so only controls of 24V or that
have voltage free contacts should be used.
Fig. 7
A
B
G
H
J
C
L
M
N
K
I
D,E
F
Q
H
N
M
Q
Q
I
Installation Requirements