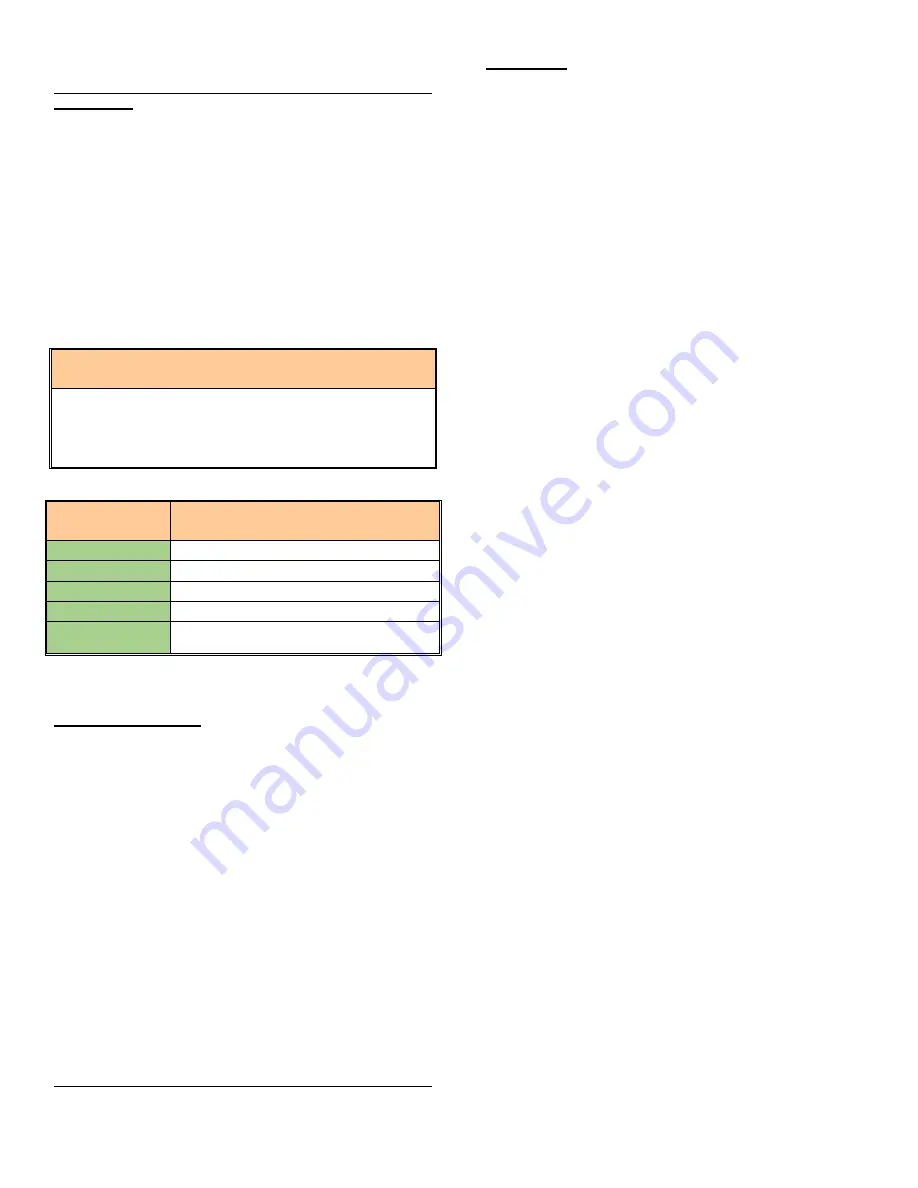
13
2.1.3
APPROVED VENTING MATERIALS
Exhaust Vent for Use for Dynaforce® Category ll or lV
Installations
1 Manufactured prefabricated UL/ ULC listed vent of AL29-
4C or equivalent, Single or Double Wall.
2 316L stainless steel is limited to use in applications where
there is no possibility of contaminants in the air such as
refrigerants, chlorine etc.
3 “BH” type.
4 PVC and CPVC Schedule 40 or 80 approved to ULC S636
5 PVC-DWV approved to comply with ANSI/ASTM D2665
(US Jurisdictions ONLY when permitted)
6 PVC Schedule 40 approved to comply with ANSI/ASTM
D1785 (US Jurisdictions ONLY when permitted)
7 CPVC Schedule 40 approved to comply with ANSI/ASTM
F441. (US Jurisdictions ONLY when permitted)
8 Polypropylene approved to comply with ULC S636 up to 12”
diameter.
NOTE
1) Use of cellular core PVC (ASTM F891), cellular core
CPVC or Radel® (polyphenosulfone) in venting systems
is prohibited.
2) Covering non-metallic vent pipe and fittings with thermal
insulation is prohibited.
Table 4: Maximum Flue Temperature for Various Vent Materials
Vent Material
Maximum Flue Temperature [
o
F]
PVC
149
CPVC
194
Polypropylene
230
AL29-4C
300+, limited only by rating of seals
316L Stainless
Steel
300+, limited only by rating of seals
Stack temperature is 10-15
o
F above boiler inlet temperature
when operating at steady-state.
Vent material selection
When selecting vent material take into consideration that
appliances installed near a corrosive or potentially corrosive air
supply must be isolated from it or they will suffer damage to the
appliance and the venting system.
The corrosion resistance of AL29-4C is typically higher than that
of 316L. Always choose the venting system which best satisfies
the requirements of the application
.
This recommendation does not supersede local codes or
the provision of the B149 in Canada or the National Fuel
Gas Code in the United States
Single wall air intake pipes are to be insulated 5 feet from wall
toward the interior of the building to minimize external sweating.
Intake Air (Supply Air, or Fresh Air) Piping for Direct Vent
Applications
Air intake material must be of a type listed by a nationally
recognized testing agency.
1
PVC
Non Foam Core Pipe.
2
CPVC
Non Foam Core Pipe.
3
Polypropylene
4
ABS
(Acrylonitrile-Butadiene-Styrene).
Single wall vent pipes to be insulated 5 feet from wall toward the
interior of the building to minimize external sweating.
2.1.4
VENT TERMINATION CLEARANCES
•
Do not terminate the vent in a window well, stairwell, alcove,
courtyard or other recessed area. The vent cannot
terminate below grade. The bottom of the vent terminal shall
be located at least 12 inches (30cm) above grade and
above normal snow levels. In all cases the appliance shall
be installed in accordance with local codes.
•
The vent outlet MUST NOT terminate below a forced air
inlet at any distance.
•
The vent cannot terminate below grade. Position the vent
termination where vapours will not damage walls or plants
or may otherwise be objectionable.
•
The vent terminal shall not be installed closer than 3 feet (1
m) from an inside corner of an L-shaped structure, window
well, stairwell, alcove, courtyard or other recessed area as
wind eddies could affect boiler performance or cause
recirculation.
•
DO NOT terminate closer than 4 feet (1.25m) horizontally
and vertically from any electric meter, gas meter, regulator,
relief valve, or other equipment. In all cases local codes
take precedence
•
Position terminations so they are not likely to be damaged
by foreign objects, or exposed to a build-up of debris.
•
The vent piping must terminate in an elbow pointed outward
or away from the air inlet.
•
To avoid a blocked flue condition, keep the vent
cap/terminal clear of snow, ice, leaves, debris, etc.
•
Flue gases from this appliance may contain large amounts
of water vapour that will form a white plume in winter. Plume
could obstruct a window view.
•
Flue gas condensate can freeze on exterior walls or on the
vent cap. Frozen condensate on the vent cap can result in
a blocked flue condition. Some discoloration to exterior
building surfaces can be expected. Adjacent brick or
masonry surfaces should be protected with a rust resistant
sheet metal plate.
2.1.5
INLET CAP FOR ROOFTOP TERMINATION
The air inlet cap consists of two 90° elbows installed at the point
of termination for the air inlet pipe. The first 90° elbow is installed
on the rooftop at the highest vertical point of the air inlet pipe
and turned horizontal; the second 90° elbow is screened and is
installed on the horizontal outlet of the first elbow and turned
down. A 90° elbow and a 90° street elbow may be used to make
this assembly. If a straight piece of pipe is used between the two
elbows, it should not exceed 6" (150mm) in length.
2.1.6
LOCATION OF A ROOFTOP AIR INLET AND VENT
CAPS
•
The point of termination for the combustion air inlet cap
MUST be at least 3 feet (0.91M) below the point of flue gas
termination (vent cap) if it is located within a 5 foot (1.5M)
radius of the flue outlet. Use care to ensure that the 90°
elbow assembly is properly installed on the air inlet pipe.
Summary of Contents for Dynaforce Series
Page 2: ...99 0171 REV 0 9...
Page 35: ...35...
Page 48: ...48...
Page 67: ...67 PART 12 EXPLODED VIEW 19 1 2 3 4 5 6 7 8 9 10 11 12 13 14 15 16 17 18 20...
Page 68: ...68 21 22 23 24 26 35 34 33 32 31 30 29 28 27 25 36 37 38 39 40 42 43 56...
Page 75: ...75 PART 13 ELECTRICAL DIAGRAMS...
Page 76: ...76...
Page 77: ...77...
Page 78: ...78...
Page 79: ...79...