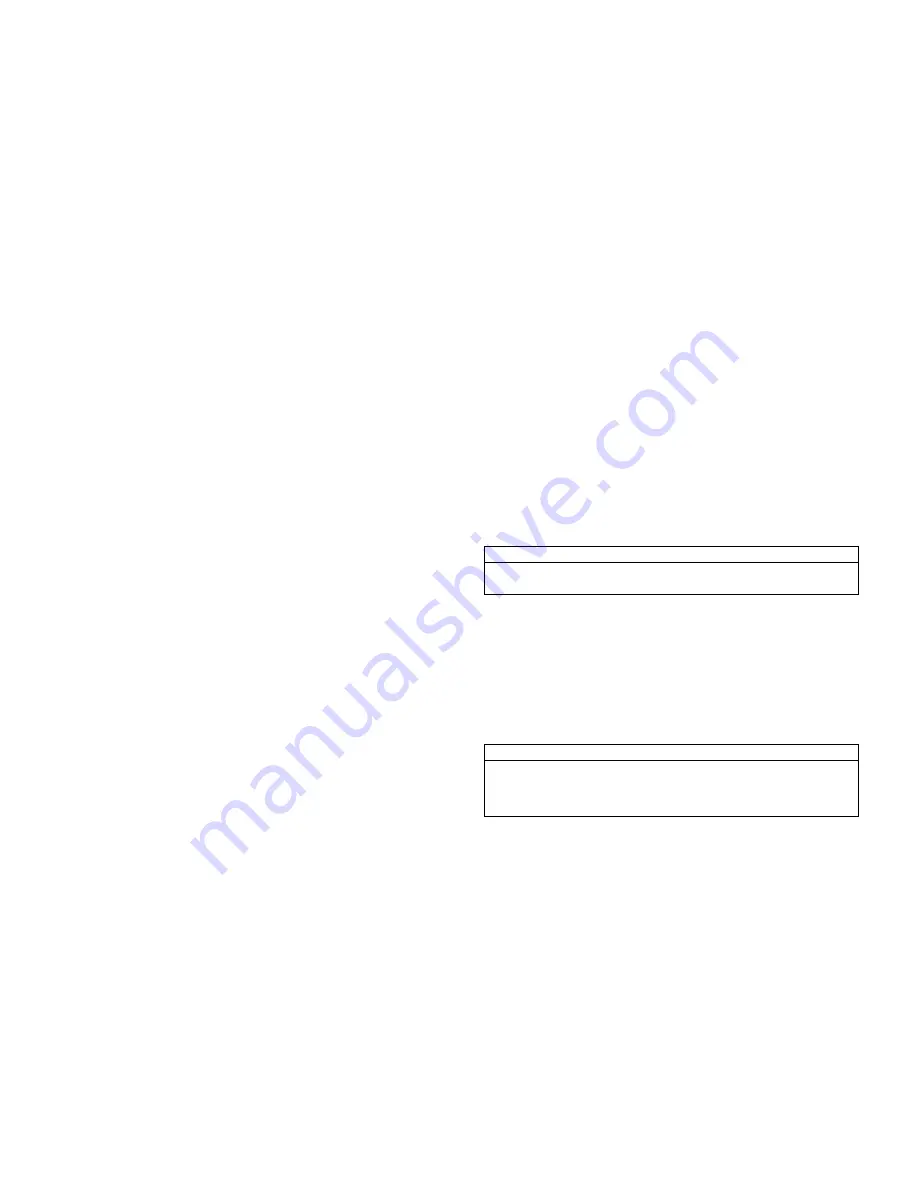
3
1.7
WARRANTY
•
Factory warranty (shipped with unit) does not
apply to units improperly installed or improperly
operated.
•
Factory warranty shall apply only when the
appliance is installed in accordance with local
plumbing and building codes, ordinances and
regulations, the printed instructions provided with it
and good industry practices.
•
Excessive water hardness causing a lime build-
up in the stainless steel coils or tubes is not a fault
of the appliance and is not covered by warranty.
Consult the factory for recommendations for use in
hard water areas.
(See Water Treatment and
Water Chemistry)
•
Using or storing corrosive chemicals in the
vicinity of this appliance can rapidly attack the
stainless steel venting and heat exchanger coils
and voids warranty.
•
Damage caused by freezing or dry firing voids
warranty.
•
This appliance is not to be used for temporary
heating of buildings under construction.
•
The manufacturer shall NOT be held liable for any
personal injury or property damage due to ice
formation or the dislodging of ice from the vent
system or the vent termination
1.8
REMOVAL OF EXISTING APPLIANCE
When an existing appliance is removed from a common
venting system, the common venting system is likely to be
too large for proper venting of the appliances remaining
connected to it .At the time of removal of an existing
appliance, the following steps must be followed with each
appliance remaining connected to the common venting
system placed in operation, while the other appliances
remaining connected to the common venting system are
not in operation.
•
Seal any unused openings in the common venting
system.
•
Visually inspect the venting system for proper size
and horizontal pitch and determine that there is no
blockage, restriction, leakage, corrosion or other
deficiency, which could cause an unsafe condition.
•
Insofar as is practical, close all building doors and
windows and all doors between the spaces in
which the appliances remaining connected to the
common venting system are located and other
spaces of the building. If applicable turn on the
clothes dryers and any appliances not connected
to the common venting system. Turn on any
exhaust fans, such as range hoods and bathroom
exhausts, so they will operate at maximum speed.
Do not operate a summer exhaust fan. Close
fireplace dampers.
•
Place in operation the appliance being inspected.
Follow the lighting instructions. Adjust thermostat
so that appliance operates continuously.
•
After it has been determined that each appliance
remaining connected to the common venting
system properly vents when tested as outlined
above, return doors, windows, exhaust fans,
fireplace dampers and any other gas-burning
appliance to their previous condition of use.
•
Any improper operation of the common venting
system should be corrected so that the installation
conforms to the National Fuel Gas Code, ANSI
Z223.1 and/or CAN/CGA B149, Installation Codes.
When resizing any portion of the common venting
system, the common venting system should be
resized to approach the minimum size as
determined using the appropriate tables in Part 11
of the National Fuel Gas Code, ANSI Z223.1 and
/or CAN/CGA B149, Installation Codes.
Heat exchanger surfaces and vent piping should be
checked every six months for deterioration and carbon
deposits. Remove all soot or other obstructions from the
chimney and flue, which might impede draft action. Replace
any damaged or deteriorated parts of the venting system.
A qualified service technician should follow this procedure
when inspecting and cleaning the heat exchanger and vent
pipe.
1) Turn off electrical power and main manual gas shut-off
and allow appliance to cool down.
2) Remove the vent pipe at connection to heat exchanger
and check heat exchanger and vent for obstruction and
clean as necessary.
3) Remove burner from appliance and carefully clean as
required. Never brush or wipe the knitted metal fiber
surface. Use a garden hose or gently wash under the
tap. Vacuum out any deposits found in the heat
exchanger.
CAUTION
Never use a pressure washer or compressed air to clean
the burner.
4) Reinstall parts removed in steps 2 and 3. Be sure that
vent pipe has proper pitch and is properly sealed.
Replace any damaged gasket or refractory. Tighten fan
flange mounting nuts to 3 ft-lb.
5) Restore electrical power and gas supply to appliance.
6) Place appliance in operation using lighting instructions
provided.
7) Confirm proper operation of all safety devices
8) Check for gas leaks and proper vent operation.
NOTE
Experience has shown that improper installation or
system design, rather than faulty equipment, is the
cause of most operating problems
1.9 BOILER/FURNACE ROOM OPERATING
CONDITION
•
Due to low jacket losses from the appliance,
temperatures in the vicinity of the boiler room may drop
significantly; supplemental heat is required to maintain
ambient temperature at minimum of 40ºF.
Summary of Contents for DMC 753
Page 20: ...16 ...
Page 63: ...59 PART 14 EXPLODED VIEW PARTS LIST DYNAMAX WALL HUNG ...
Page 64: ...60 DYNAMAX FLOOR MOUNT ...
Page 71: ...67 PART 15 ELECTRICAL DIAGRAMS 15 1 DM 80 250 INTERNAL WIRING DIAGRAM WALL HUNG MODELS ...
Page 72: ...68 15 2 DM 210 750 INTERNAL WIRING DIAGRAM FLOOR MOUNT MODELS ...