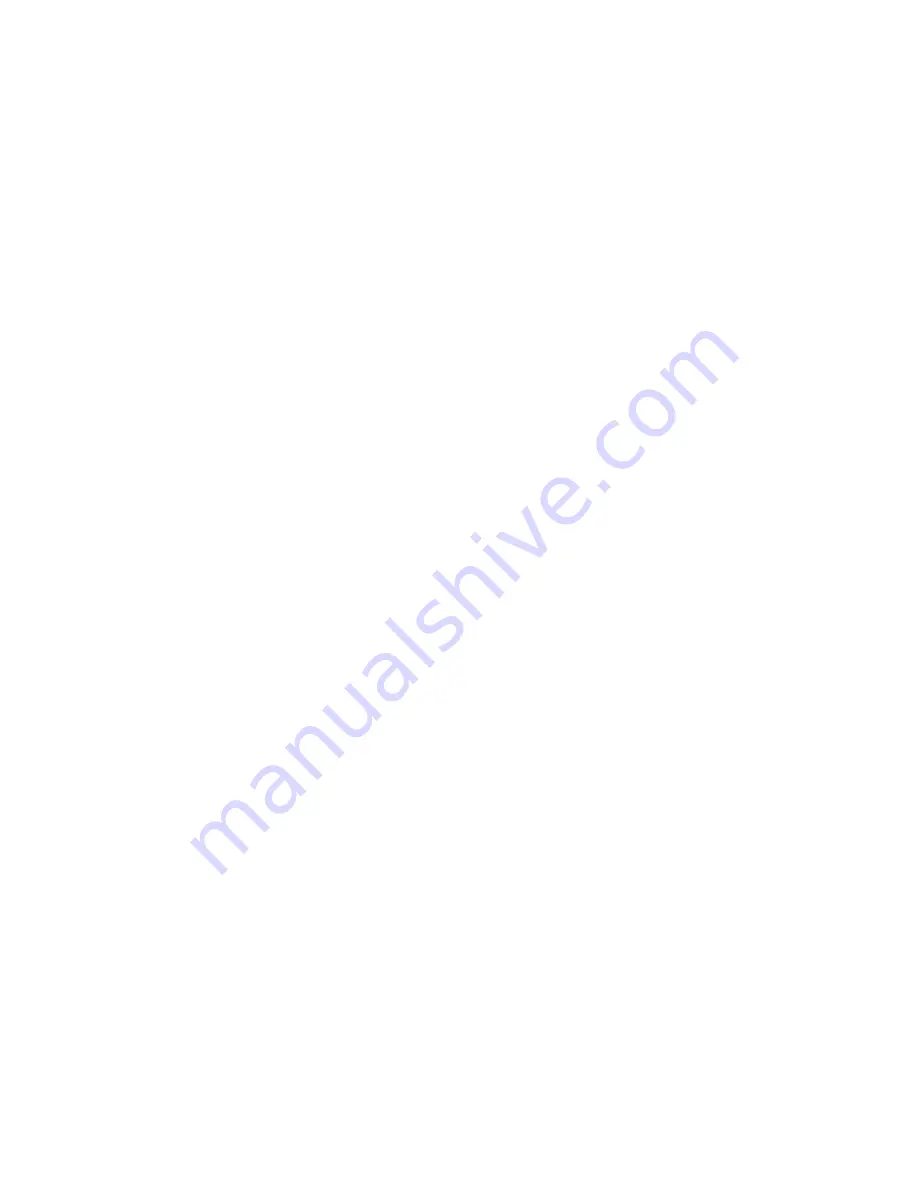
49
b) Placing the Boiler in Operation
Pre-Start Check List
1) Review the location of the boiler, clearances
from combustible surfaces and available
service clearances.
2) Review Part 2 Venting. Ensure that all vent
components are fabricated from the correct
category of materials with adequate clearance
from combustibles.
3) Fill the condensate collector with fresh water
until water begins to pour out the drain.
4) Ensure that the boiler condensate drain and all
vent system condensate drains are properly
routed to an acceptable floor drain.
5) Review the vent termination point for proper
location and clearances.
6) If a separate combustion air pipe is used,
ensure that it is properly sized, sealed and
terminated.
7) Review the water piping from the boiler to the
system. The boiler must be installed in a
primary/ secondary piping system. Review the
diameter and equivalent length of the installed
piping to and from the boiler to ensure proper
flow.
8) Ensure that a properly sized system pump is
installed with an expansion tank.
9) Check system pressure. Ensure a minimum of
18-20 PSIG with the system hot and not more
than 90% of the rated pressure of the relief
valve.
10) Review the installed gas piping from the meter
to the boiler. Ensure that the gas pipe, meter
and any regulators are adequately sized.
11) Review the field wiring and electrical service
for the boiler controls. Ensure that the electrical
service(s) is adequately sized.
Boiler Set-Up
1) Ensure that the boiler and piping system are
full of water. Bleed all air from the pump
housing and secondary loop.
2) Check system for any water leaks.
3) Check system for installation of glycol or water
treatment where required. Where glycol has
been used to maintain the temperature rise
across the appliance confirm that the
recommended flow for pure water has been
increased by 15% and the head loss by 20%.
Boiler Operational Checks
1) Turn the boiler main power switch to the “ON”
position.
2) Verify operation of the text display on the front
panel.
3) Program the adjustable points.
4) Push the reset button if a lockout error is
displayed.
5) Install a manometer on the gas supply to the
boiler and verify minimum gas supply pressure
as the burner fires at 100% of rated input.
6) Verify operation of safeties as necessary (low
water cut-off, high limit, gas pressure, etc.).
Boiler Operation
1) Appliance should begin the start-up process for
the sequence of operation.
2) The boiler will fire at 50% of rated input on
initial start-up and adjust input as required to
meet system demand.
3) Based on system demand, the appliance will
modulate accordingly.
4) As system demand is satisfied, the burner will
fire at minimum fire for the given demand and
the boiler will cycle off when the demand
ceases or is interrupted. When this occurs the
combustion air fan will decelerate at a pre-
programmed rate before the appliance shuts
down.
12.8
DOMESTIC HOT WATER WITH STORAGE
TANK
Hot water heaters are designed for installation with a storage
tank. The piping between the tank and heater and the control
of water velocity, as explained below, are important for
correct operation of your hot water heater.
12.9
DOMESTIC HOT WATER WITH PLATE
HEAT EXCHANGER
The piping between the plate heat exchanger in the
DynaMax boiler and to an outlet tap is important for correct
operation of the plate heat exchanger. The following
procedure should be followed for setting the domestic hot
water tuning valve:
1) There is a temperature tuning valve inside the
Dynamax jacket on the domestic hot water outlet
from plate exchanger . This valve can be set for
field conditions .
2) First identify the highest domestic hot water load .
For example in some cases it may be the bath tub
and in some cases it may be the clothes washer.
3) Allow the Dynamax to fire up and reach full fire
under maximum hot water load demand conditions .
4) Observe the outlet water temperature and close the
tuning valve gradually as outlet temperature starts
to drop . Allow the system to reach equilibrium
between adjustments to the tuning valve .
5) Once the tuning valve is properly set , outlet
temperatures will never drop below
desired minimum temperature.
6) Seal stem of tuning valve with silicone to prevent
unauthorized tampering .
Summary of Contents for DMC 753
Page 20: ...16 ...
Page 63: ...59 PART 14 EXPLODED VIEW PARTS LIST DYNAMAX WALL HUNG ...
Page 64: ...60 DYNAMAX FLOOR MOUNT ...
Page 71: ...67 PART 15 ELECTRICAL DIAGRAMS 15 1 DM 80 250 INTERNAL WIRING DIAGRAM WALL HUNG MODELS ...
Page 72: ...68 15 2 DM 210 750 INTERNAL WIRING DIAGRAM FLOOR MOUNT MODELS ...